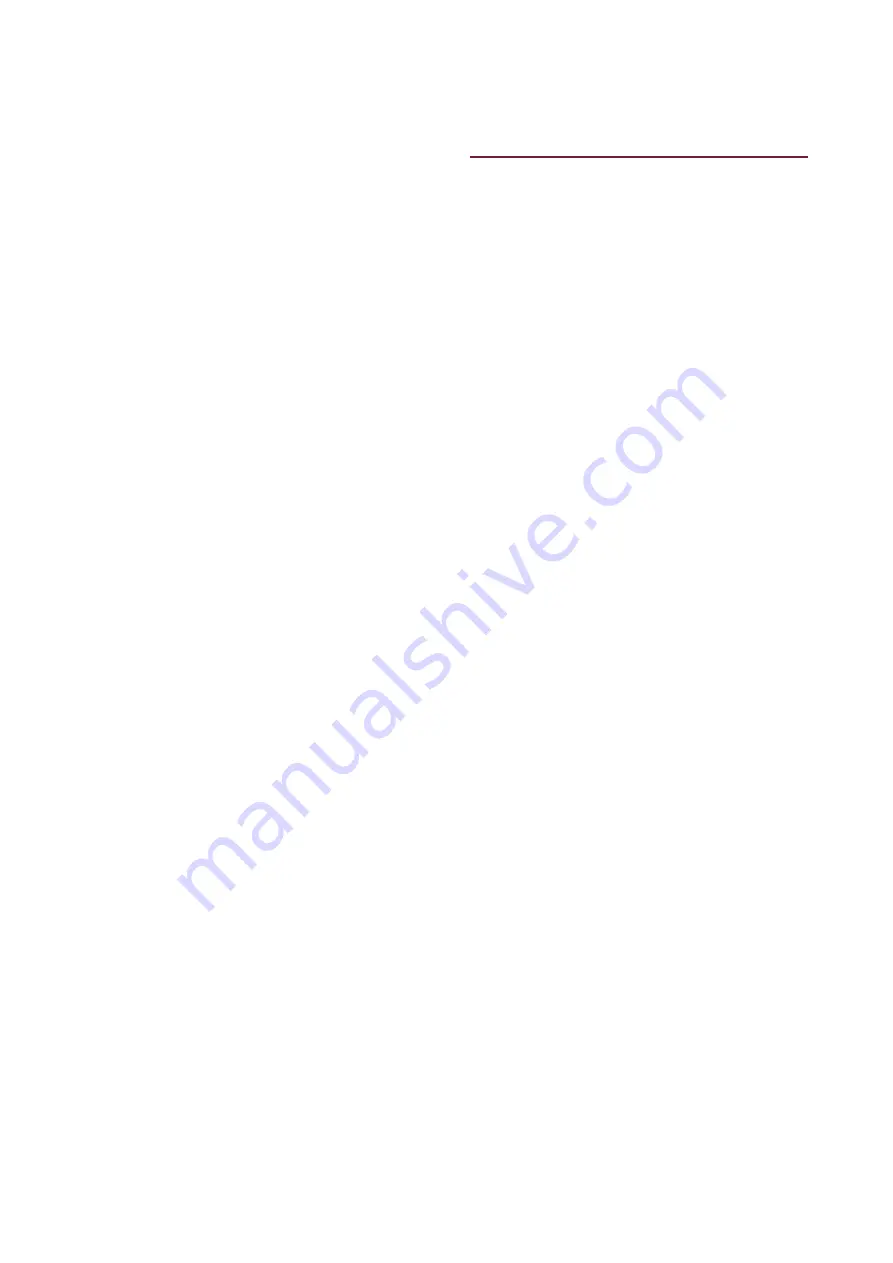
Reznor, FSE, Installation Manual, EN 2020-02, D301160 Iss H
• Open the room thermostat contact and
make sure that the burner stops
• Close the room thermostat contact
again and perform a new burner
ignition cycle
• Close the fuel shut-off valve and make
sure the burner stops
During the first start-up cycle, the burner
may stop due to the lack of fuel supply.
In this case, wait at least 30 seconds and,
after resetting the burner by pressing the
dedicated button, repeat the operation.
During the first few hours of operation, it
is common for fumes and odours to form
due to the heating of paints and seals. The
smell will fade by itself within a few hours,
but if it continues for a prolonged period of
time, please contact the manufacturer. It is
recommended to ventilate the room during
this time.
To Stop
To stop the air heater, use the room
thermostat only, by setting it to the
minimum temperature or by opening the
contact of the switch itself —if present— or
on stop.
Wait for the fan to stop (4 min.) and then,
if necessary, turn the power off from the
main switch.
Never stop the appliance by cutting off the
electrical power, the thermal energy stored
in the heat exchanger may cause dangerous
overheating situations, with possible
damage to the air heater.
Moreover the ‘LIMIT’ thermostat could
be triggered and it might be necessary to
release it manually.
Inspections
In order to ensure that the heater works
properly, some basic parameters should be
checked.
Turn the unit on and:
• Make sure that the fan unit starts within
60 seconds after the burner is turned
on.
With the unit steady
(After an approximate 20 minutes of
continuous use) perform the following
operations:
• Make sure there are no fuel leaks.
• Check the correct fuel flow rate by
weighing the diesel fuel or reading the
gas meter
• Check that the unit’s flue gas
temperature and the technical data are
similar with a tolerance of ± 10°C.
• Make sure that the manual resetting
safety thermostat calibration is correct.
• Check that the temperature near the
safety thermostat is correct (ambient
tempe air temperature).
• Check that no faults have been reported
on the safety thermostat.
• Check that no faults have been reported
on the safety devices present on the
machine.
• Make sure that the temperature
gradient is compliant to the value
specified in Table 2 on page 9 with a
±2°k tolerance.
• Re-activate the appliance. Simulate the
intervention of the safety thermostat
and check that the burner turns off. Do
not adjust the factory settings
Summary of Contents for Reznor FSE 100
Page 2: ......
Page 46: ...PAGE 42 Reznor FSE Installation Manual EN 2020 02 D301160 Iss H...
Page 51: ......
Page 52: ......