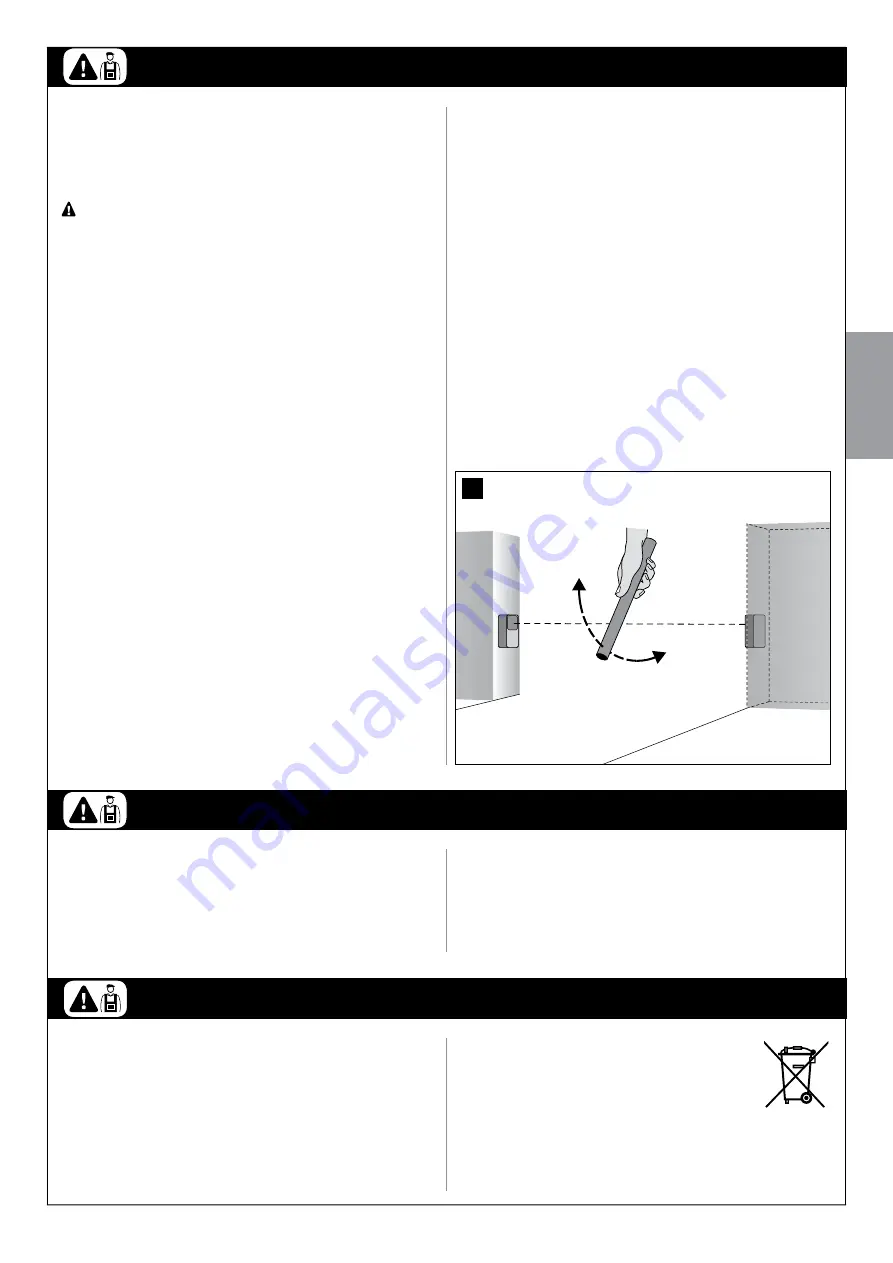
English –
11
English
TESTING AND COMMISSIONING
––– STEP 8 –––
Maintenance must be performed in strict observance of the safety
provisions in this manual and according to current legislation and
standards.
The automation devices do not require special maintenance. However a
check should be performed at least every six months to ensure complete
efficiency of all devices.
For this purpose, the tests and checks envisaged in paragraph 7.1 “Test-
ing” should all be performed, as well as all procedure in the paragraph
“Maintenance operations permitted for the user”.
If other devices are present, follow the instructions in the relative mainte-
nance schedule.
MAINTENANCE
7.2 - COMMISSIONING
Commissioning can only be performed after all test phases have
been successfully completed. Partial or “makeshift” commission-
ing is strictly prohibited.
01.
Draw up the technical dossier of the automation that should include
as a minimum: overall design (for example
fig. 1
), electrical connec-
tions wiring diagram (for example
fig. 6
), risk analysis and related
adopted solutions, manufacturer conformance declaration for all the
devices used (use Annex 1).
02.
Affix a dataplate on the door, specifying at least the following data:
type of automation, name and address of manufacturer (responsible
for commissioning), serial number, year of construction and CE mark.
03.
Permanently attach to the gate the label supplied in the pack, regard-
ing the procedure for manual locking/release of the gearmotor.
04.
Compile and provide the automation owner with the declaration of
conformity (use Annex 1).
05.
Prepare and provide the owner with the Maintenance schedule form,
containing all maintenance instructions for all devices in the automa-
tion.
06.
Before commissioning the automation, ensure that the owner is
properly informed of all associated risks and hazards.
This product is an integral part of the automation and therefore
must be disposed together with the latter.
As in installation, also at the end of product lifetime, the disassembly and
scrapping operations must be performed by qualified personnel.
This product is made of various types of material, some of which can be
recycled while others must be scrapped. Seek information on the recy-
cling and disposal systems required by local regulations in your area for
this product category.
Warning!
– some parts of the product may contain pollutants or hazard-
ous substances which, if disposed of in the environment, may cause seri-
ous damage to the environment or physical health.
As indicated by the symbol alongside, disposal of this
product in domestic waste is strictly prohibited. Sepa-
rate the waste into categories for disposal, according to
the methods set out by legislation in force in your area, or
return the product to the retailer when purchasing a new
version.
Warning!
– Local legislation may provide for severe fines for improper
disposal of this product.
PRODUCT DISPOSAL
––– STEP 7 –––
These are the most important phases when setting up an automation, in
order to guarantee maximum safety.
Testing can also be used as a periodic check of devices in the automa-
tion.
CAUTION! – The system must be tested by skilled and quali-
fied personnel, who is responsible for defining the tests adopted
in relation to the risks present, and for ensuring observance of all
legal provisions, standards and regulations, with particular ref-
erence to all requirements of the EN 13241-1, EN 12445 and EN
12453 standards which defines the test methods for testing gate
automations.
7.1 - TESTING
01.
Ensure that all instructions and warnings in STEP 1 have been
strictly observed.
02.
Using the selector or radio transmitter, test a gate closing and open-
ing cycle and ensure that the leaf movement corresponds to speci-
fications. A number of tests should be performed to ensure that the
gate moves smoothly and that there are no assembly defects, incor-
rect settings, or any points of friction.
03.
Check the proper operation of all the safety devices, one by one
(photocells, safety edges, etc.). In particular, each time a device trips,
the “ECSbus” led on the control unit emits a longer flash to confirm
control unit recognition of the event.
04.
To check the photocells and make sure that there is no interfer-
ence with other devices, pass a 5 cm diameter, 30 cm long cylinder
(
fig. 16
) on the optical axis, first near TX, then near RX and finally at
the mid-point between them and make sure that in all these cases
the device is triggered, switching from active status to alarm status
and vice versa; finally, make sure that it causes the intended action
in the control unit; for example, reversal of the movement during the
closing manoeuvre.
05.
Measure the force as specified in standard EN 12445. If the “motor
force” control is used as an auxiliary function for reduction of impact
force, test and identify the setting that obtains the best results.
16
Summary of Contents for CLB207
Page 2: ...Fran ais...
Page 9: ...Fran ais 7 Fran ais 8 7 1 Led SAFE 3 2 4 5 mm 01 03 05 02 04 9...
Page 10: ...8 Fran ais Fran ais 6 mm x4 05 B 6 mm x4 05 A 2 1 aerial flash 2 1 06 07 08 09 02 03 04 01 10...
Page 26: ...Fran ais...
Page 33: ...English 7 English 8 7 1 Led SAFE 3 2 4 5 mm 01 03 05 02 04 9...
Page 34: ...8 English English 6 mm x4 05 B 6 mm x4 05 A 2 1 aerial flash 2 1 06 07 08 09 02 03 04 01 10...
Page 50: ......
Page 57: ...Italiano 7 Italiano 8 7 1 Led SAFE 3 2 4 5 mm 01 03 05 02 04 9...
Page 58: ...8 Italiano Italiano 6 mm x4 05 B 6 mm x4 05 A 2 1 aerial flash 2 1 06 07 08 09 02 03 04 01 10...
Page 74: ...Fran ais...
Page 81: ...Polski 7 Polski 8 7 1 Led SAFE 3 2 4 5 mm 01 03 05 02 04 9...
Page 82: ...8 Polski Polski 6 mm x4 05 B 6 mm x4 05 A 2 1 aerial flash 2 1 06 07 08 09 02 03 04 01 10...