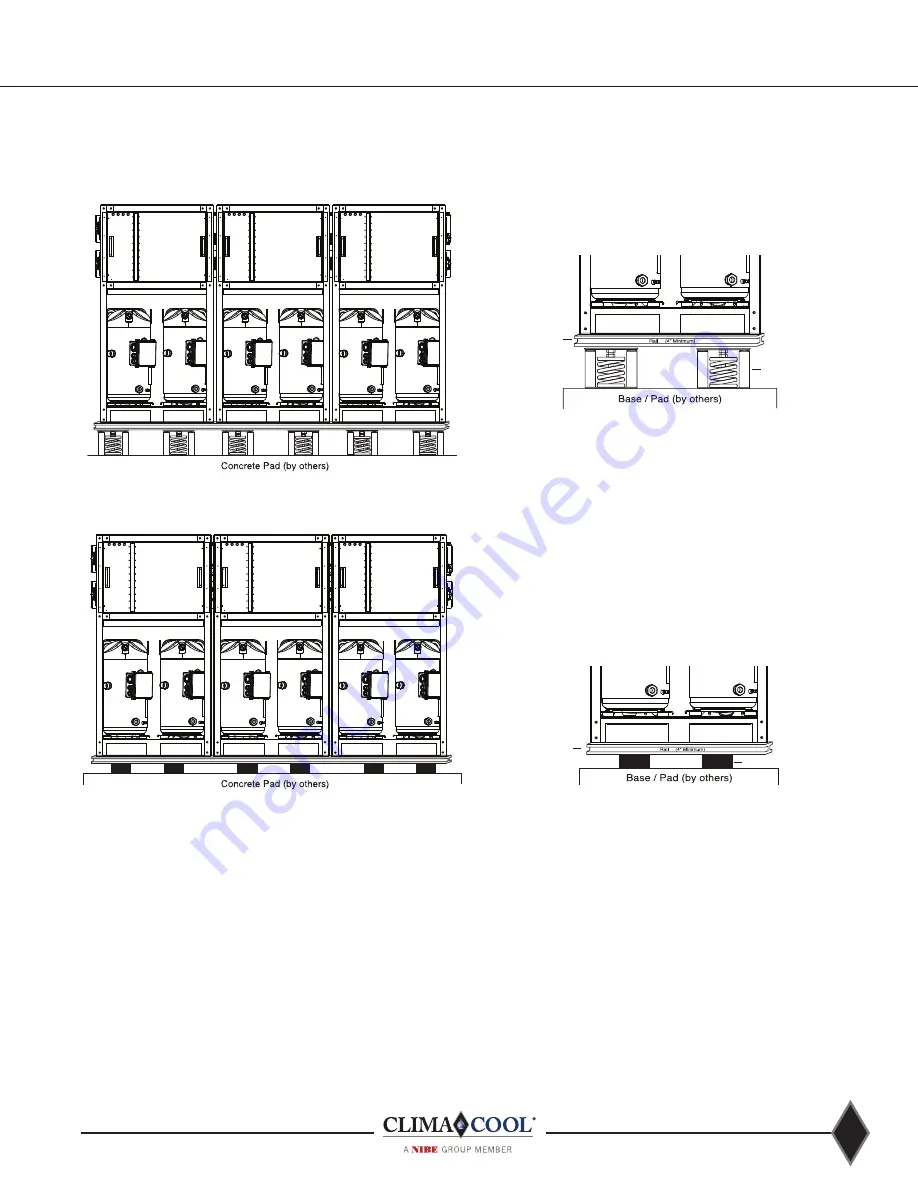
11
www.climacoolcorp.com
Spring Vibration
Isolators (by others)
4” Rail Minimum
Recommended
(by others)
Spring Vibration
Isolators (by others)
4” Rail Minimum
Recommended
(by others)
Mounting Rail and Vibration Isolation
Figure 6 - Spring Vibration Isolators Option
Figure 7 – Vibration Isolation Pads Option
Note:
Size and weight distribution is to be determined by a qualified structural engineer per individual job requirements.
ClimaCool recommends locking down the chiller to a concrete base or to three (3) 4” base mounting rails using the six (6)
bolt holes provided in each base pan . Due to the low vibration of the modules, the application of spring isolators or pads is
not required . Should isolators or pads be desired, install in accordance with Figures 6 and 7 .
4” Rail Minimum
Recommended
(by others)
Vibration Pads (by others)
4” Rail Minimum
Recommended
(by others)
Vibration Pads (by others)
Summary of Contents for CLIMACOOL UCR 30
Page 19: ...17 www climacoolcorp com Voltage Phase Monitor Wiring Diagram...
Page 29: ...27 www climacoolcorp com Evaporator Water Pressure Drop Charts...
Page 30: ...28 www climacoolcorp com Glycol Performance Adjustments Factor Charts...
Page 78: ...76 www climacoolcorp com Wiring Diagram...
Page 79: ...77 www climacoolcorp com Wiring Diagram...
Page 80: ...78 www climacoolcorp com Wiring Diagram CoolLogic Control Panel...
Page 81: ...79 www climacoolcorp com Wiring Diagram CoolLogic Control Panel...