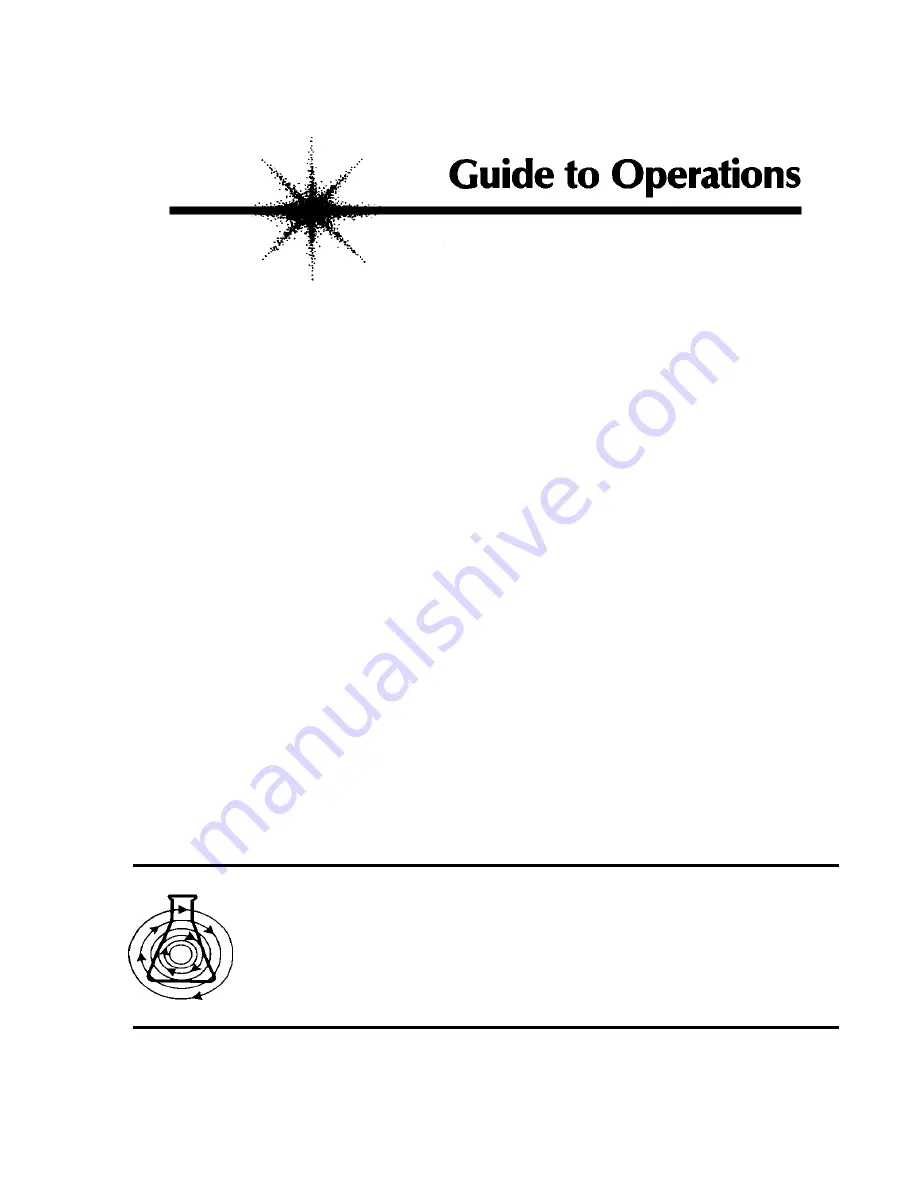
BioFlo 4500
Benchtop
Fermentor/Bioreactor
MANUAL
NO:
M1254-0050
Revision H
September 27, 2002
NEW BRUNSWICK SCIENTIFIC CO., INC.
BOX 4005
•
44 TALMADGE ROAD
•
EDISON, NJ 08818-4005
Telephone: 1-732-287-1200
•
1-800-631-5417
Fax: 732-287-4222
•
Telex: 4753012 NBSCO
Internet: http://www.nbsc.com
•
E-mail: [email protected]
Summary of Contents for BioFlo 4500
Page 2: ...BioFlo 4500 M1254 0050 User s Guide ii...
Page 4: ...BioFlo 4500 M1254 0050 User s Guide iv THIS PAGE INTENTIONALLY BLANK...
Page 6: ...BioFlo 4500 M1254 0050 User s Guide vi THIS PAGE INTENTIONALLY BLANK...
Page 8: ...BioFlo 4500 M1254 0050 User s Guide viii THIS PAGE INTENTIONALLY BLANK...
Page 10: ...BioFlo 4500 M1254 0050 User s Guide x THIS PAGE INTENTIONALLY BLANK...
Page 12: ...BioFlo 4500 M1254 0050 User s Guide xii THIS PAGE INTENTIONALLY BLANK...
Page 18: ...BioFlo 4500 M1254 0050 User s Guide xviii...
Page 34: ...BioFlo 4500 M1254 0050 User s Guide 34 THIS PAGE INTENTIONALLY BLANK...
Page 42: ...BioFlo 4500 M1254 0050 User s Guide 42 THIS PAGE INTENTIONALLY BLANK...
Page 60: ...BioFlo 4500 M1254 0050 User s Guide 60 THIS PAGE INTENTIONALLY BLANK...
Page 82: ...BioFlo 4500 M1254 0050 User s Guide 82 THIS PAGE INTENTIONALLY BLANK...
Page 88: ...BioFlo 4500 M1254 0050 User s Guide 88 THIS PAGE INTENTIONALLY BLANK...
Page 114: ...BioFlo 4500 M1254 0050 User s Guide 114 THIS PAGE INTENTIONALLY BLANK...
Page 138: ...BioFlo 4500 M1254 0050 User s Guide 138 THIS PAGE INTENTIONALLY BLANK...
Page 144: ...BioFlo 4500 M1254 0050 User s Guide 144 THIS PAGE INTENTIONALLY BLANK...
Page 152: ...BioFlo 4500 M1254 0050 User s Guide 152 THIS PAGE INTENTIONALLY BLANK...
Page 154: ...BioFlo 4500 M1254 0050 User s Guide 154...
Page 160: ...BioFlo 4500 M1254 0050 User s Guide 160 THIS PAGE INTENTIONALLY BLANK...
Page 162: ...BioFlo 4500 M1254 0050 User s Guide 162 THIS PAGE INTENTIONALLY BLANK...
Page 164: ...BioFlo 4500 M1254 0050 User s Guide 164 THIS PAGE INTENTIONALLY BLANK...
Page 168: ...BioFlo 4500 M1254 0050 User s Guide 168 THIS PAGE INTENTIONALLY BLANK...
Page 186: ...BioFlo 4500 M1254 0050 User s Guide 186 THIS PAGE INTENTIONALLY BLANK...
Page 194: ...BioFlo 4500 M1254 0050 User s Guide 194 THIS PAGE INTENTIONALLY BLANK...
Page 196: ...BioFlo 4500 M1254 0050 User s Guide 196 THIS PAGE INTENTIONALLY BLANK...
Page 208: ...BioFlo 4500 M1254 0050 User s Guide 208 THIS PAGE INTENTIONALLY BLANK...
Page 214: ...BioFlo 4500 M1254 0050 User s Guide 214 Figure 49 Power Schematics Detail A...