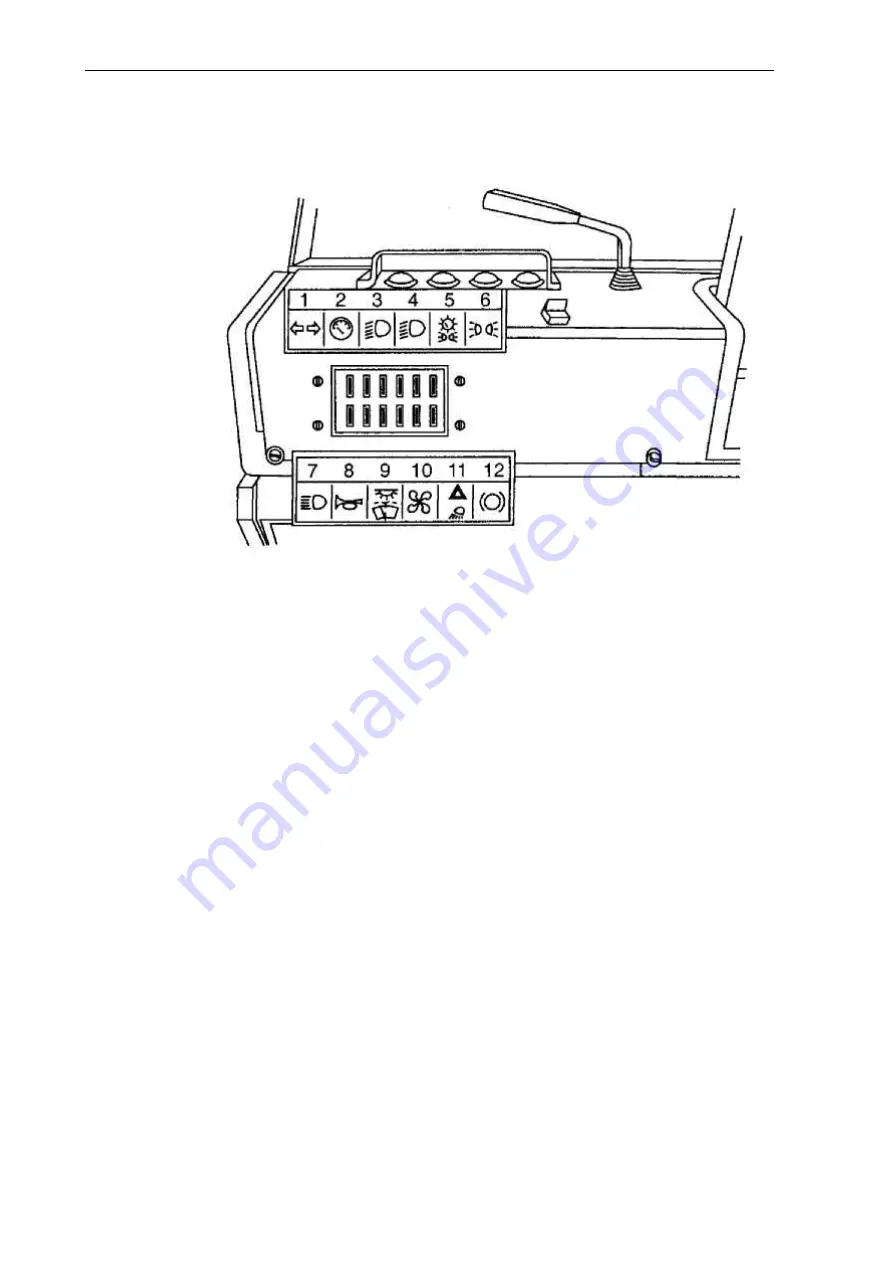
Section C. Controls and Instruments Belarus – 90/92 Operating manual
29
Fuses
Two blocks of fuses are installed in electric chains.
12 safety locks protect from overloads the following electric chains of tractor:
1 —indexes of turns, 15
А
;
2 — feed of control-measuring instruments, 7,5
А
;
3 — passing light of left road headlight 7,5
А
;
4 — passing light of right road headlight, 7,5
А
;
5 — dimensional fires of right board, illumination of plate, illumination of devices
, 15
А
;
6 — dimensional fires of left board, 7,5
А
;
7 — headlight of road headlights, 25
А
;
8 — horn, 15
А
;
9 — reserve, 25
А
;
10 — reserve, 15
А
;
11 — emergency light signal system, back working headlights, 15
А
;
12 — stop-alarm fires, feed of portable lamp, 15
А
.
Besides there is block with safety lock of 60 ampere on oil tank for protection of
chain of storage battery.
https://tractormanualz.com/