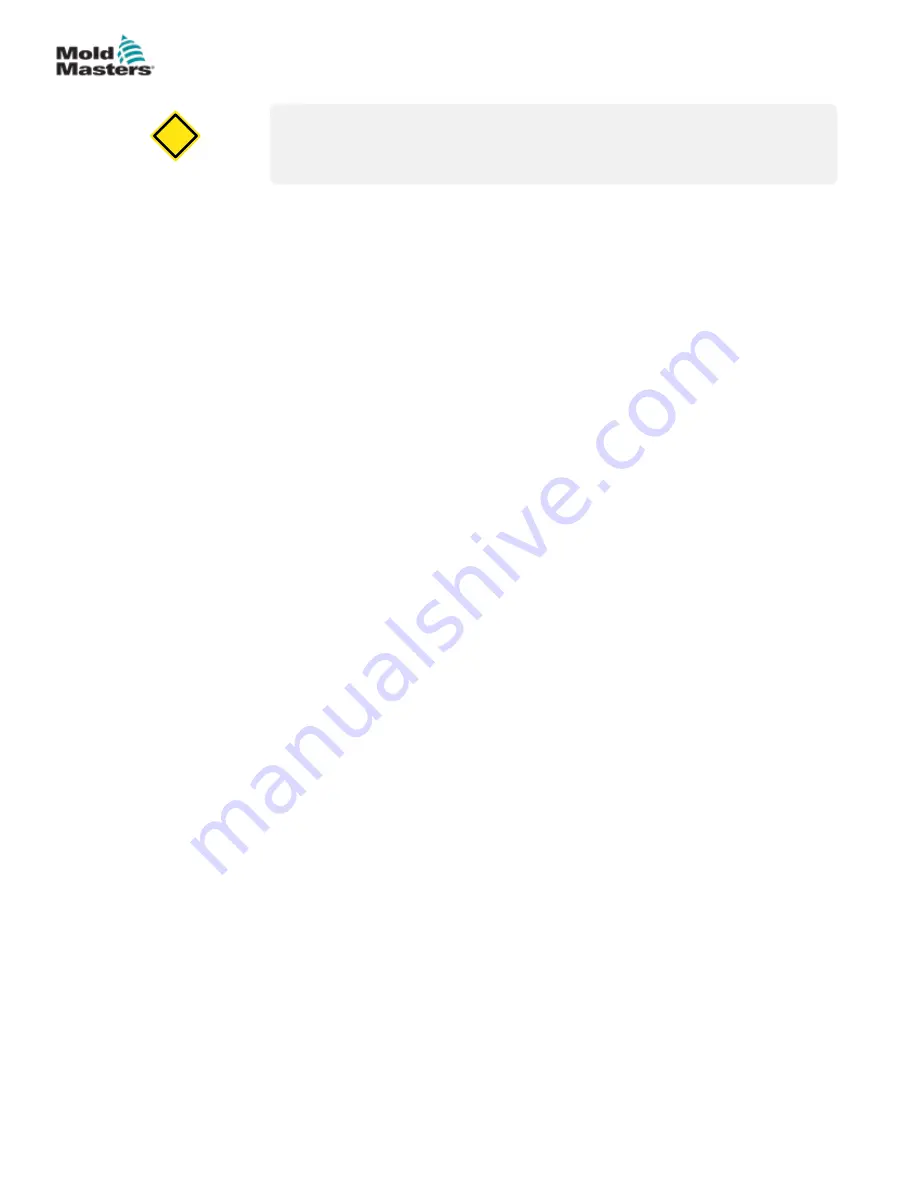
10.3 Color Change for a Valve Gate System
CAUTION
Do not activate the valve gate while purging or feeding the barrel, unless
the Hot Runner system has reached normal processing temperature.
CAUTION
1.
When the system is up and running with one color, back-off the injection
unit, purge and introduce the new color.
2. Start molding the new color until the majority of old color has been
removed from the Hot Runner system.
3.
Back-off the injection unit and switch off all heats on the Hot Runner
system.
4. Allow the Hot Runner system to cool down. Leave mold water cooling /
actuator cooling on. This pulls old material away from the runner walls
and allows new and old color to mix.
5. Heat up the system and start molding.
10.4 Locating a Source of Contamination
6. Purge the original color from the machine, following the instructions in:
• “10.2 Color Change for a Hot Tip / Sprue System” on page 10-1
• “10.3 Color Change for a Valve Gate System” on page 10-2
7.
Load the hopper with a second color (differe
nt from the intended color).
8.
Continue to purge until no trace of the first color appears.
9.
Shut off the hopper and continue to remove the second color, following
the instructions above.
10.
Load the hopper with the third, and final intended color.
11. Purge the third color through the injection unit to clean the injection unit of
the second color.
12.
Continue to purge until no trace of the first color appears.
13. If the second color appears in the molded product then the problem is in
the injection unit.
10-2
© 2020 Mold-Masters (2007) Limited. All Rights Reserved.
COLOR CHANGE
FSG2 User Manual
Summary of Contents for Fusion G2
Page 1: ...version 14 User Manual Original Instructions...
Page 2: ......
Page 10: ......
Page 64: ......
Page 151: ......