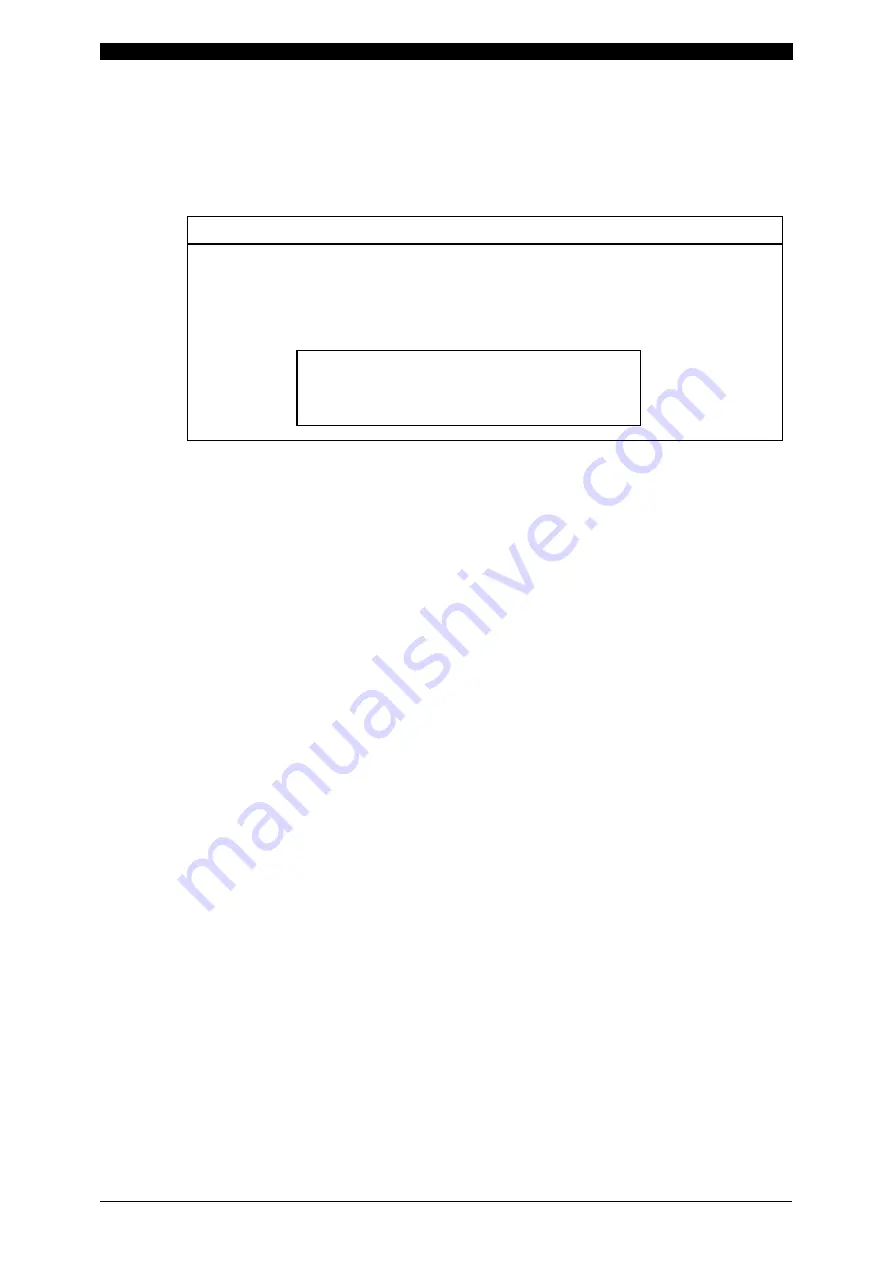
IS-120B
3. Name and Functions of Each Section
3-6
⑥
Connector
This connector is used to connect the circuit cable. Connect the other end of the
cable to the
[
PROGRAM UNIT
]
connector
of
IS-120B
.
CAUTION
Setting and change for each item cannot be done from the start signal
receiving to the weld sequence end.
If the setting is done during the weld sequence, the following screen appears.
Press
①
[TROUBLE RESET] key.
IS-120B IS BUSY OR NOT CONNECTED
Please RESET key in