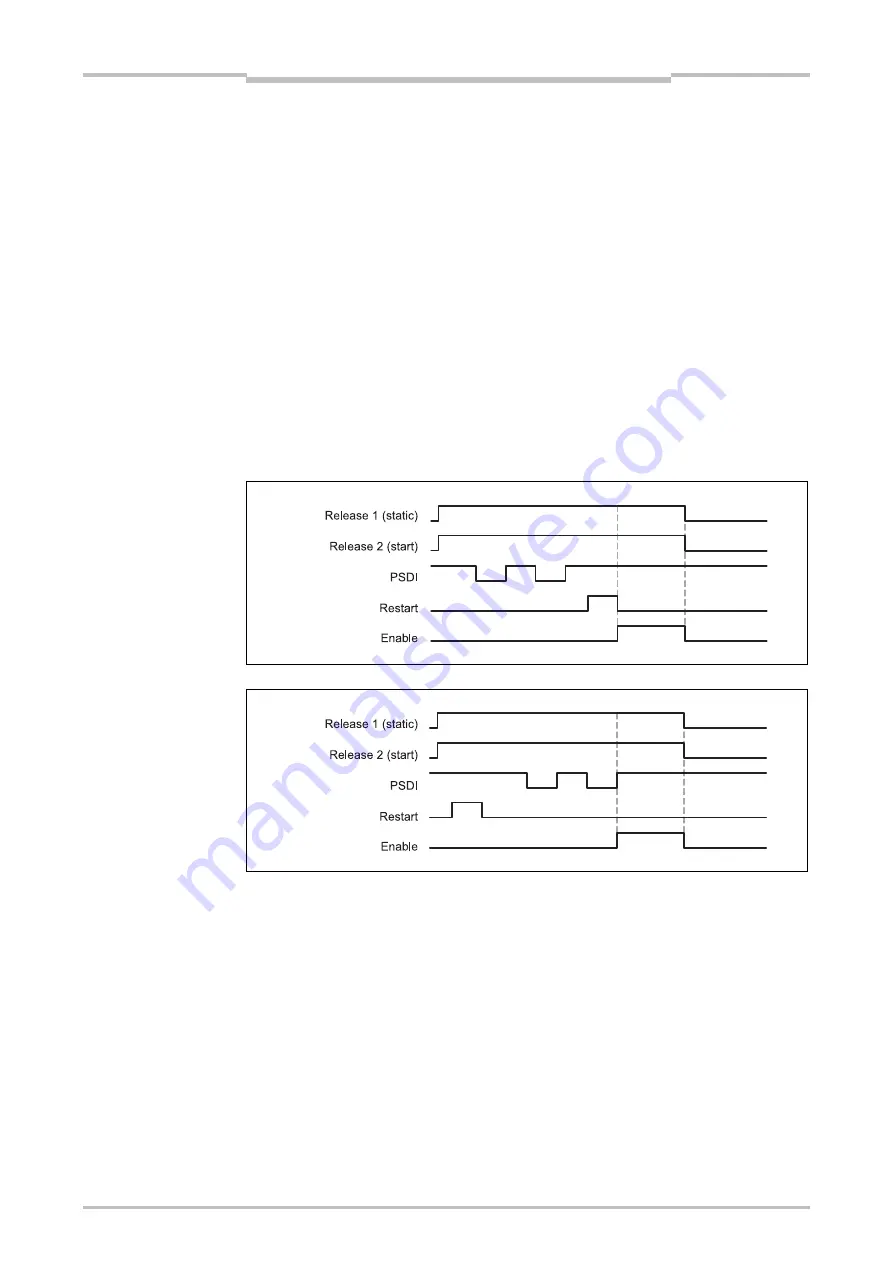
Chapter 9
252
Logic programming – Function blocks
Requirements for the start sequence
If the
Enable
output changes to Low because of one of the following conditions, a
complete start sequence can be necessary:
Release 1 (static)
is Low,
the
Unexpected PSDI
output is High, while Cycle = 0 and there is no active
upstroke muting and no stop at the top dead center,
in case of a PSDI timeout,
after the
Control of drive
has been switched on
If the
Unexpected PSDI
output is High and the
Enable
output is Low and the
PSDI
input is also Low and
Restart interlock
is set to
Without
, a restart is possible without
a complete restart sequence. This can also apply during the press upstroke if
Restart
interlock
is set to
Always
.
The minimum break time at the
PSDI
input is 100 ms or 350 ms. Shorter breaks are
not evaluated as valid, i.e. they are ignored. If the
Condition for Release 2 (start)
input
is configured as
Necessary for first start
or as
Necessary for every start
, the
Release 2 (start)
input also must be High if a complete start sequence is required.
After the initial complete start sequence has been executed and the press has
completed a press cycle, the
Top
input must indicate that the press has currently
reached the top dead center. This is indicated by a rising edge (Low to High) of the
Top
input. When this happens, the internal break counter is reset.
A cycle start sequence is required in order to trigger a subsequent cycle. In this case,
the
Enable
output is set to High when the configured number of breaks has occurred
and the remaining configured conditions have been fulfilled (e.g.,
Condition for
Release 2 (start) input
can be configured as
Necessary for every start
).
Figure 235:
Sequence/timing diagram
for a complete start
sequence in Standard mode
in two-cycle mode
Figure 236:
Sequence/timing diagram
for a complete start
sequence in Sweden mode
in two-cycle mode
Summary of Contents for SW1DNN-WS0ADR-B
Page 2: ......
Page 288: ...Chapter 15 285 Annex ...
Page 289: ...Chapter 15 286 Annex ...
Page 290: ...Chapter 15 287 Annex ...
Page 291: ...Chapter 15 288 Annex ...
Page 292: ...Chapter 15 289 Annex ...
Page 293: ...Chapter 15 290 Annex ...
Page 294: ...Chapter 15 291 Annex ...
Page 295: ...Chapter 15 292 Annex ...
Page 296: ...Chapter 15 293 Annex ...
Page 297: ...Chapter 15 294 Annex ...
Page 298: ...Chapter 15 295 Annex 15 1 2 Example application Wood scanner ...
Page 299: ...Chapter 15 296 Annex ...
Page 300: ...Chapter 15 297 Annex ...
Page 301: ...Chapter 15 298 Annex ...
Page 302: ...Chapter 15 299 Annex ...
Page 303: ...Chapter 15 300 Annex ...
Page 304: ...Chapter 15 301 Annex ...
Page 305: ...Chapter 15 302 Annex ...
Page 306: ...Chapter 15 303 Annex ...
Page 307: ...Chapter 15 304 Annex 15 1 3 Example application Ramp down detection ...
Page 308: ...Chapter 15 305 Annex ...
Page 309: ...Chapter 15 306 Annex ...
Page 310: ...Chapter 15 307 Annex ...
Page 311: ...Chapter 15 308 Annex ...
Page 312: ...Chapter 15 309 Annex ...
Page 313: ...Chapter 15 310 Annex ...
Page 314: ...Chapter 15 311 Annex ...
Page 321: ......