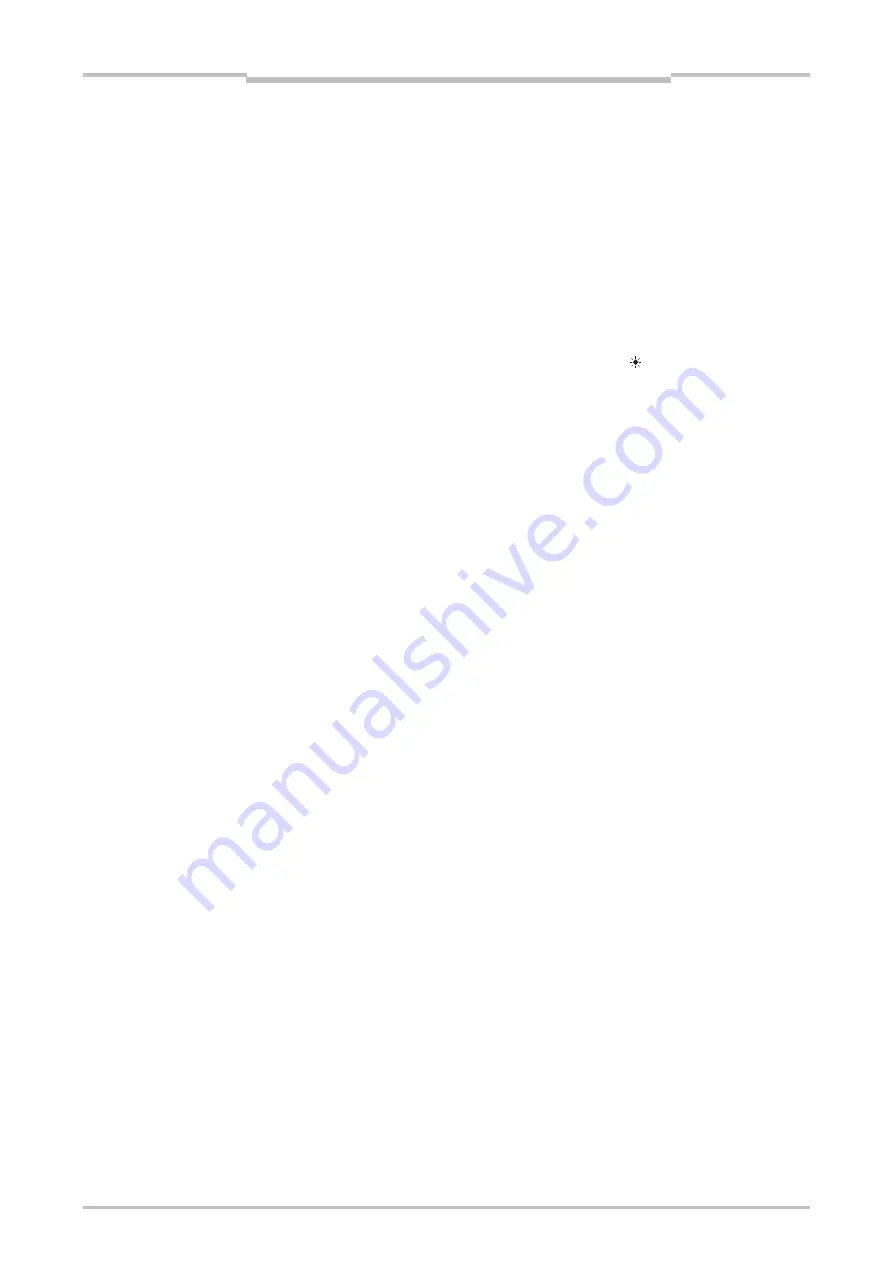
Chapter 7
106
Flexi Link
7.5 Flexi
Link
troubleshooting
This section deals with some common causes for malfunctions of the Flexi Link
network and how to diagnose and correct them.
For an overview of the LED error displays please refer to the Safety Controller User’s
Manual.
7.5.1
Flexi Link ID mismatch
Error description
If no process image transfer is possible between the stations in your system and all
CPU modules show a recoverable error (MS LED flashing
Red at 1 Hz and EFI1
and EFI2 LEDs light up Red), this could be due to a Flexi Link ID mismatch. This
means that at least one of the stations in the system has one or two Flexi Link IDs that
differ from the other stations’ Flexi Link IDs.
Diagnostics
Switch to the Flexi Link
System overview
.
If the Setting and Monitoring Tool is not connected to the system, connect to all
stations.
Check the status messages of the stations for indication of a Flexi Link ID mismatch.
Correction of the error
If different Flexi Link IDs exist in the system, the current configuration must be
transferred to all stations again.
Check whether the configuration in the Setting and Monitoring Tool is correct.
Connect to all stations.
Transfer the configuration to all stations.
Switch to the view for each station and verify the configuration if necessary.
Summary of Contents for SW1DNN-WS0ADR-B
Page 2: ......
Page 288: ...Chapter 15 285 Annex ...
Page 289: ...Chapter 15 286 Annex ...
Page 290: ...Chapter 15 287 Annex ...
Page 291: ...Chapter 15 288 Annex ...
Page 292: ...Chapter 15 289 Annex ...
Page 293: ...Chapter 15 290 Annex ...
Page 294: ...Chapter 15 291 Annex ...
Page 295: ...Chapter 15 292 Annex ...
Page 296: ...Chapter 15 293 Annex ...
Page 297: ...Chapter 15 294 Annex ...
Page 298: ...Chapter 15 295 Annex 15 1 2 Example application Wood scanner ...
Page 299: ...Chapter 15 296 Annex ...
Page 300: ...Chapter 15 297 Annex ...
Page 301: ...Chapter 15 298 Annex ...
Page 302: ...Chapter 15 299 Annex ...
Page 303: ...Chapter 15 300 Annex ...
Page 304: ...Chapter 15 301 Annex ...
Page 305: ...Chapter 15 302 Annex ...
Page 306: ...Chapter 15 303 Annex ...
Page 307: ...Chapter 15 304 Annex 15 1 3 Example application Ramp down detection ...
Page 308: ...Chapter 15 305 Annex ...
Page 309: ...Chapter 15 306 Annex ...
Page 310: ...Chapter 15 307 Annex ...
Page 311: ...Chapter 15 308 Annex ...
Page 312: ...Chapter 15 309 Annex ...
Page 313: ...Chapter 15 310 Annex ...
Page 314: ...Chapter 15 311 Annex ...
Page 321: ......