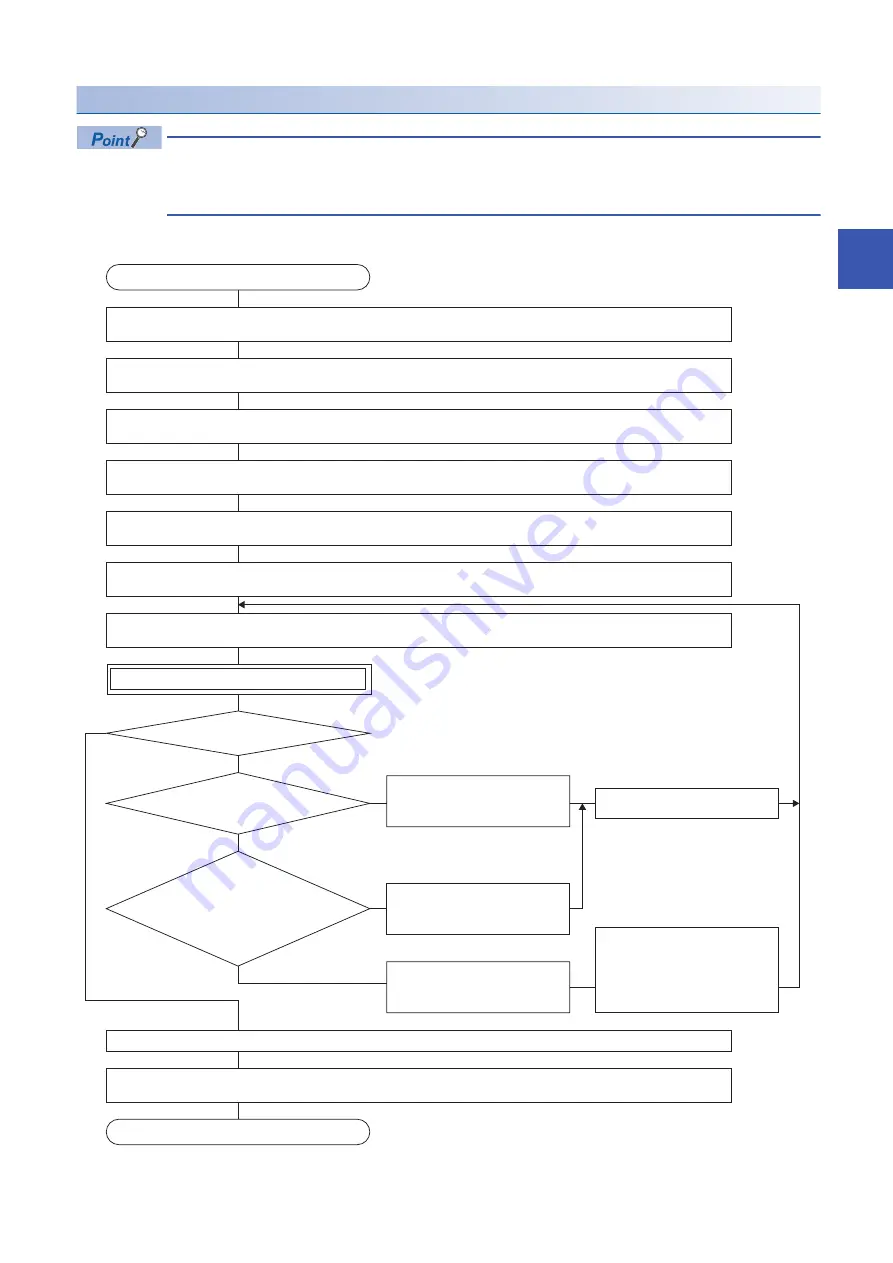
11 USING A DIRECT DRIVE MOTOR
11.2 Startup [G] [WG]
367
11
Magnetic pole detection procedure
When using a controller manufactured by Mitsubishi Electric, the servo parameter setting values are
overwritten from the controller. Once magnetic pole detection is complete, note down the changed servo
parameter setting values, and set the same values in the controller.
■
Magnetic pole detection by position detection method
*1 For the incremental system, the setting of [Pr. PL01] is not required.
NO
YES
YES
NO
YES
NO
Magnetic pole detection
Set [Pr. PL08.0 Magnetic pole detection method selection] to "0" (position detection method).
Set [Pr. PL01.0 Servo motor magnetic pole detection selection] to "1" (Magnetic pole detection at initial servo-on after cycling the
power).
*1
Set [Pr. PL09 Magnetic pole detection - Voltage level] to "10" as a guide value.
Execute "Forward rotation CCW" or "Reverse rotation CW" with "Positioning operation" in the test operation mode on MR
Configurator2. Set the travel distance to "0" at this time.
The magnetic pole detection is performed.
Is [Pr. PL09] the final value?
Perform one of the following operations:
alarm reset, servo amplifier power cycling,
or software reset.
Has [AL. 027 Initial magnetic pole
detection error] occurred?
Increase the value of [Pr. PL09] by five.
Have [AL. 032 Overcurrent],
[AL. 050 Overload 1],
[AL. 051 Overload 2],
and [AL. 0E1 Overload warning 1]
occurred?
Cycle the power of the servo amplifier
or reset the software.
Set approximately 70 % of the value set for
[Pr. PL09] as the final setting value. If [AL.
027] occurs with this value, specify a value
intermediate between the value set at [AL.
0E1] and the value set at [AL. 027] as the
final setting value.
Perform one of the following operations:
alarm reset, servo amplifier power cycling,
or software reset.
Set [Pr. PL01.0] to "0" (Magnetic pole detection disabled).
*1
End
Check if LSP (Forward rotation stroke end), LSN (Reverse rotation stroke end), and EM2 (Forced stop 2) have been turned on.
Then, cycle the power of the servo amplifier or reset software.
Turn "ON (up)" the DIP switch (SW3-1).
Then, cycle the power of the servo amplifier or reset software.
Cycle the power of the servo amplifier or reset software.
Turn "OFF (down)" the DIP switch (SW3-1).
Then, cycle the power of the servo amplifier or reset software.
Summary of Contents for Melservo-J5 MR-J5 Series
Page 2: ......
Page 441: ...12 USING A FULLY CLOSED LOOP SYSTEM 12 7 Absolute position detection system 439 12 MEMO ...
Page 445: ......