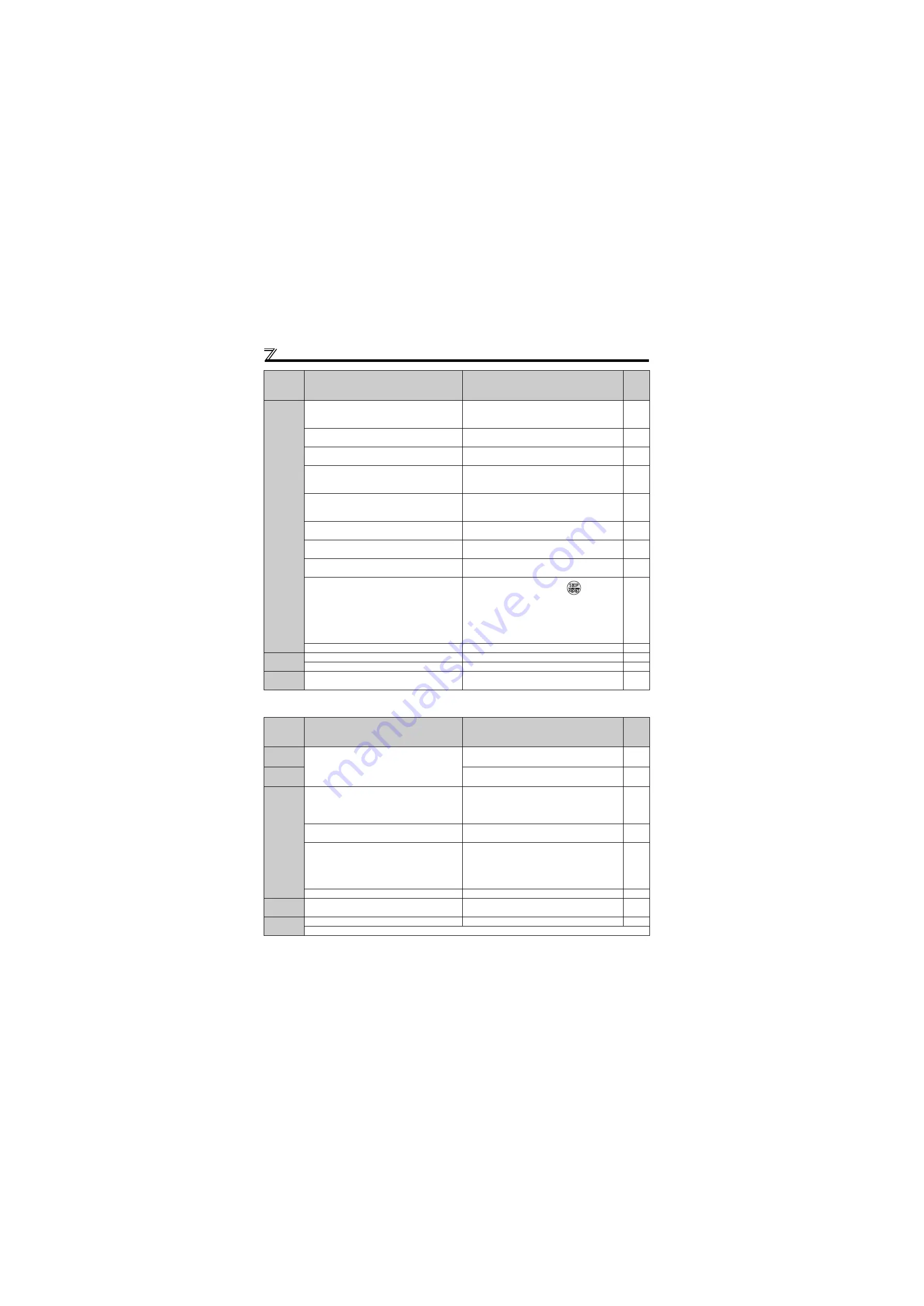
266
Check first when you have a trouble
5.5.2
Motor or machine is making abnormal acoustic noise
Parameter
Setting
Pr. 78 Reverse rotation prevention selection
is set.
Check the
Pr. 78
setting.
Set
Pr. 78
when you want to limit the motor rotation to
only one direction.
Pr. 79 Operation mode selection
setting is wrong.
Select the operation mode which corresponds with input
methods of start command and speed command.
Bias and gain
(calibration parameter C2 to C7)
settings
are improper.
Check the bias and gain
(calibration parameter C2 to C7)
settings.
Pr. 13 Starting speed
setting is greater than the running
speed.
Set running speed higher than
Pr. 13
.
The drive unit does not start if the speed setting signal is
less than the value set in
Pr. 13
.
Speed settings of various running speed (such as multi-
speed operation) are zero.
Especially,
Pr. 1 Maximum setting
is zero.
Set the speed command according to the application.
Set
Pr. 1
higher than the actual speed used.
Pr. 15 Jog speed setting
setting is lower than
Pr. 13 Starting
speed
.
Set
Pr. 15 Jog speed setting
higher than
Pr. 13 Starting
speed
Operation mode and a writing device do not match.
Check
Pr. 79, Pr. 338, Pr. 339, Pr. 551,
and select an
operation mode suitable for the purpose.
Start signal operation selection is set by the
Pr. 250 Stop
selection
Check
Pr. 250
setting and connection of STF and STR
signals.
Performing offline auto tuning.
When offline auto tuning ends, press
of the
operation panel for the PU operation. For the External
operation, turn OFF the start signal (STF or STR).
This operation resets the offline auto tuning, and the PU's
monitor display returns to the normal indication.
(Without this operation, next operation cannot be started.)
PM motor test operation is selected.
Set "30" in
Pr. 800 Regenerative function selection
.
Load
Load is too heavy.
Reduce the load.
—
Shaft is locked.
Inspect the machine (motor).
—
Others
Operation panel display shows an error (e.g. E.OC1).
When any fault occurs, take an appropriate corrective
action, then reset the drive unit, and resume the operation.
Check
Points
Possible Cause
Countermeasures
Refer
to
Page
Input
Signal
Disturbance due to EMI when speed command is given
from analog input (terminal 2, 4).
Take countermeasures against EMI.
Parameter
Setting
Increase the
Pr. 74 Input filter time constant
if steady
operation cannot be performed due to EMI.
Parameter
Setting
Resonance occurs. (Rotation speed)
Set
Pr. 31 to Pr. 36 (speed jump)
.
When it is desired to avoid resonance attributable to the
natural speed of a mechanical system, these
parameters allow resonant speeds to be jumped.
Offline auto tuning is not performed when driving a
motor other than S-PM geared motor.
Perform offline auto tuning.
Gain adjustment during PID control is insufficient.
To stabilize the measured value, change the proportional
band (
Pr. 129
) to a larger value, the integral time (
Pr. 130
)
to a slightly longer time, and the differential time (
Pr. 134
)
to a slightly shorter time.
Check the calibration of set point and measured value.
Speed control gain is too high.
Check
Pr. 820 Speed control P gain
setting.
Others
Mechanical looseness
Adjust machine/equipment so that there is no
mechanical looseness.
—
Motor
Operating with output phase loss
Check the motor wiring.
—
Please contact your sales representative.
Check
Points
Possible Cause
Countermeasures
Refer
to
Page
Summary of Contents for FR-D720-0.2K-G
Page 45: ...34 MEMO ...
Page 293: ...290 MEMO ...