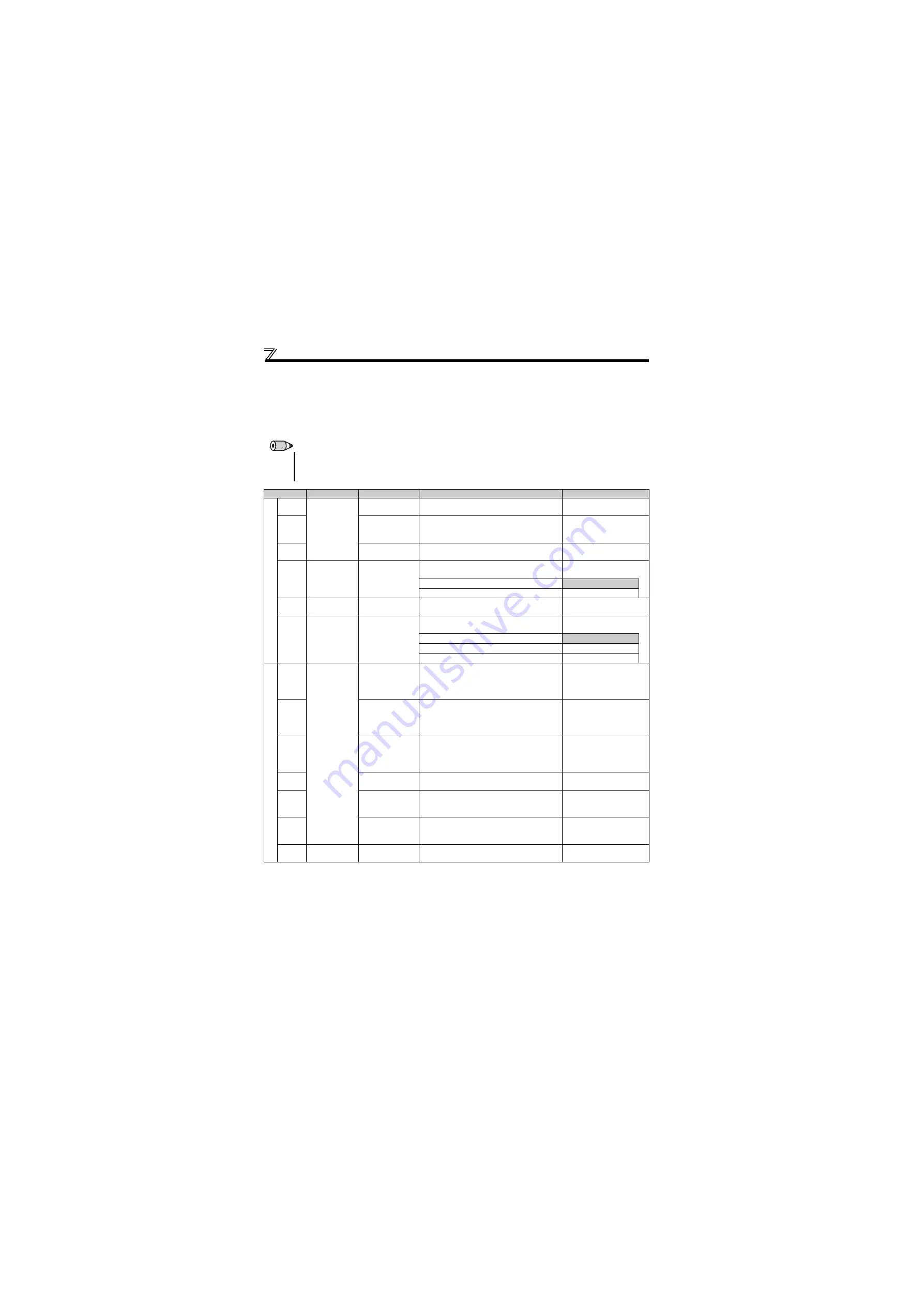
220
Special operation and speed control
(4) I/O signals and parameter setting
Set "20, 21" in
Pr. 128
to perform PID operation.
Set "14" in any of
Pr. 178 to Pr. 182 (input terminal function selection)
to assign PID control selection (X14) signal to turn the
X14 signal ON.
When the X14 signal is not assigned, only the
Pr. 128
setting makes PID control valid.
Enter the set point using the drive unit terminal 2 or
Pr. 133
and enter the measured value to terminal 4.
REMARKS
When
Pr. 128
= "0" or X14 signal is OFF, normal drive unit operation is performed without PID action.
Turning ON/OFF of bit of the terminal, to which X14 signal is assigned through network as RS-485 communication, enables
PID control.
Signal
Terminal Used
Function
Description
Parameter Setting
Input
X14
Depending on
Pr. 178 to Pr. 182
PID control
selection
Turn ON X14 signal to perform PID control.
Set 14 in any of
Pr. 178
to
Pr.
182
.
X64
PID forward/
reverse action
switchover
By turning ON X64, forward action can be
selected for PID reverse action (
Pr. 128
= 20), and
reverse action for forward action (
Pr. 128
= 21).
Set 64 in any of
Pr. 178 to Pr.
182
.
X72
PID integral value
reset
ON: Integral and differential values are reset
OFF: Normal processing
Set 72 in any of
Pr. 178 to Pr.
182
.
2
2
Set point input
You can input the set point for PID control.
Pr. 128
= 20, 21,
Pr. 133
= 9999
0 to 5V ..............0 to 100%
Pr. 73
= 1
, 11
0 to 10V ............0 to 100%
Pr. 73
= 0, 10
PU
—
Set point input
Set the set point
(Pr. 133)
from the operation
panel.
Pr. 128
= 20, 21
Pr. 133
= 0 to 100%
4
4
Measured value
input
Input the signal from the detector (measured
value signal).
Pr. 128
= 20, 21
4 to 20mA .........0 to 100%
Pr. 267
= 0
1 to 5V ..............0 to 100%
Pr. 267
= 1
2 to 10V ............0 to 100%
Pr. 267
= 2
Outpu
t
FUP
Depending on
Pr. 190
or
Pr. 192
Upper limit output
Output to indicate that the measured value signal
exceeded the maximum value
(Pr. 131)
.
Pr. 128
= 20, 21
Pr. 131
9999
Set 15 or 115 in
Pr. 190
or
Pr. 192
.
FDN
Lower limit output
Output when the measured value signal falls
below the minimum value
(Pr. 132)
.
Pr. 128
= 20, 21
Pr. 132
9999
Set 14 or 114 in
Pr. 190
or
Pr. 192
.
RL
Forward (reverse)
rotation direction
output
"Hi" is output to indicate that the output indication
of the parameter unit is forward rotation (FWD) or
"Low" to indicate that it is reverse rotation (REV)
or stop (STOP).
Set 16 or 116 in
Pr. 190
or
Pr. 192
.
PID
During PID control
activated
Turns ON during PID control.
Set 47 or 147 in
Pr. 190
or
Pr. 192
.
SLEEP
PID output
interruption
Turns ON when the PID output
interruption function is performed.
Pr. 575
9999
Set 70 or 170 in
Pr. 190
or
Pr. 192
.
Y48
PID deviation limit
Output when the absolute value of deviation
exceeds the limit value.
Pr. 553
9999
Set 48 or 148 in any of
Pr. 190
or
Pr. 192
.
SE
SE
Output terminal
common
Common terminal for open collector output
terminal.
When the X14 signal is not assigned, only the
Pr. 128
setting makes PID control valid.
The shaded area indicates the parameter initial value.
When 100 or larger value is set in any of
Pr. 190
and
Pr. 192 (output terminal function selection)
, the terminal output has negative logic.
details.)
When
Pr. 561 PTC thermistor protection level
"9999", terminal 2 is not available for set point input.
Use
Pr. 133
for set point input.
When the voltage/current input specifications were changed using
Pr. 73
and
Pr. 267
, be sure to make calibration.
(Refer to page 224 for calibration examples
for PID control.)
Summary of Contents for FR-D720-0.2K-G
Page 45: ...34 MEMO ...
Page 293: ...290 MEMO ...