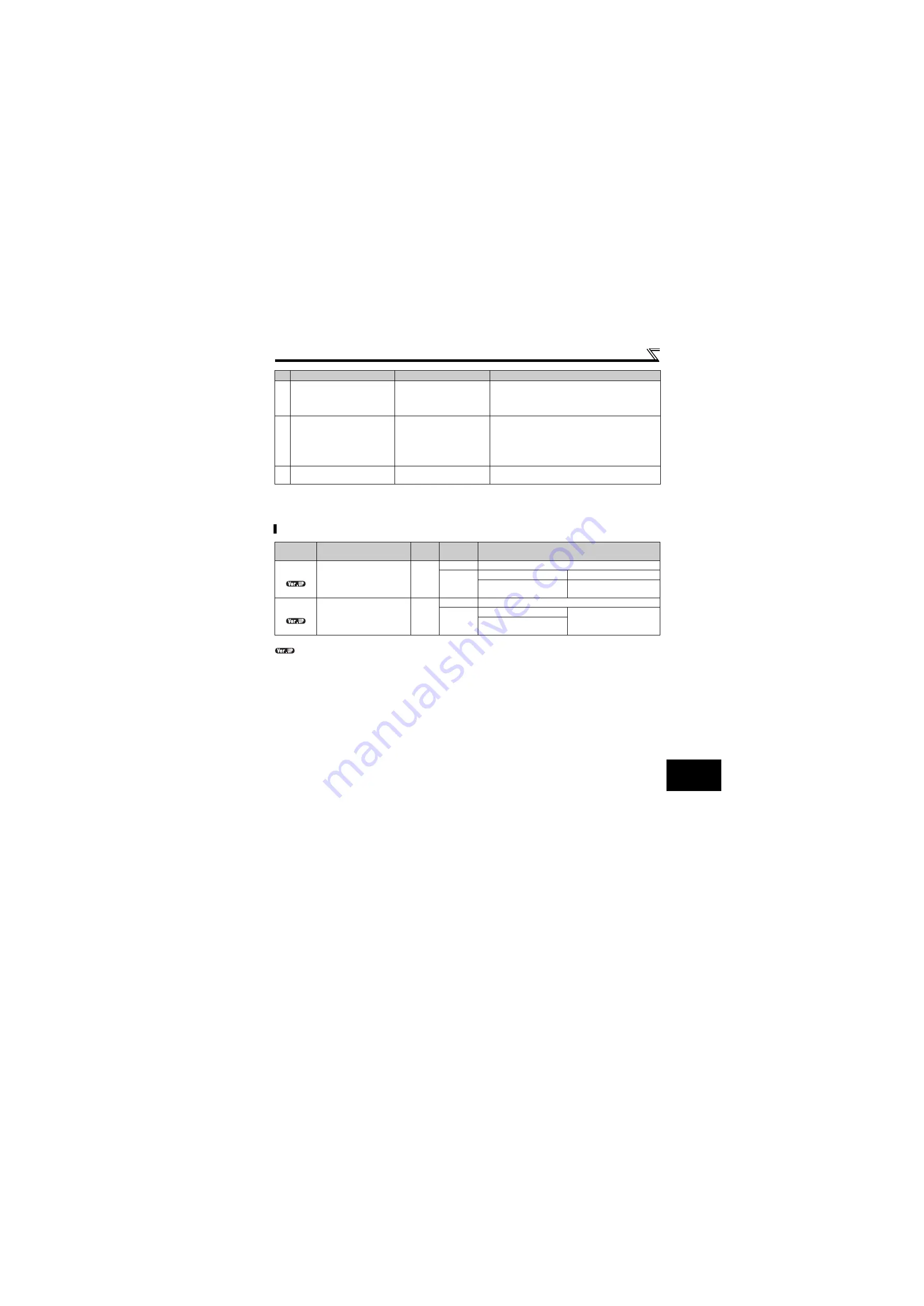
81
Test operation and gain adjustment of the PM sensorless vector control
4.3.6
Gain adjustment of current controllers for the d axis and the q axis (Pr.824, Pr.825)
The above parameters can be set when
Pr.160 Extended function display selection
= "0". (
........Specifications differ according to the date assembled.
to check the SERIAL number.
(1) Current loop proportional (P) gain adjustment
(Pr. 824)
Use
Pr.824 Torque control P gain (current loop proportional gain)
to adjust the proportional gain of current controllers for the d axis
and the q axis. The 100% gain is equivalent to 1000 rad/s. Setting this parameter higher improves the trackability for current
command changes. It also reduces the current fluctuation caused by external disturbances.
(2) Current control integral time adjustment
(Pr. 825)
Use
Pr.825 Torque control integral time (current loop integral time)
to set the integral time of current controllers for the d axis and
the q axis. If the setting value is small, it produces current fluctuation against external disturbances, decreasing time until it
returns to original current value.
5
Acceleration/deceleration time is
different from the setting.
(1) Torque shortage
(2) Load inertia is too high.
(1) Raise the stall prevention operation level.
(
.)
(2) Set acceleration/deceleration time suitable for the
load.
6
Machine movement is unstable.
(1) Speed control gain is not
suitable for the machine.
(2) Response is slow because
of the drive unit's
acceleration/deceleration
time setting.
(1) Adjust
Pr. 820
and
Pr. 821
(2) Set the optimum acceleration/deceleration time.
7
Rotation ripple occurs during the
low-speed operation.
Speed control gain is too low.
Raise
Pr. 820
.
The gain of the current controller can be adjusted.
Parameter
Number
Name
Initial
Value
Setting
Range
Operation
824
Torque control P gain
(current loop
proportional gain)
9999
0 to 200%
Set the current loop proportional gain.
9999
S-PM geared motor
50% is set.
IPM motor (after tuning)
SPM motor (after tuning)
100% is set.
825
Torque control integral
time (current loop
integral time)
9999
0 to 500ms Set current loop integral compensation time.
9999
S-PM geared motor
20.0ms is set.
IPM motor (after tuning)
SPM motor (after tuning)
Condition
Possible Cause
Countermeasure
Summary of Contents for FR-D720-0.2K-G
Page 45: ...34 MEMO ...
Page 293: ...290 MEMO ...