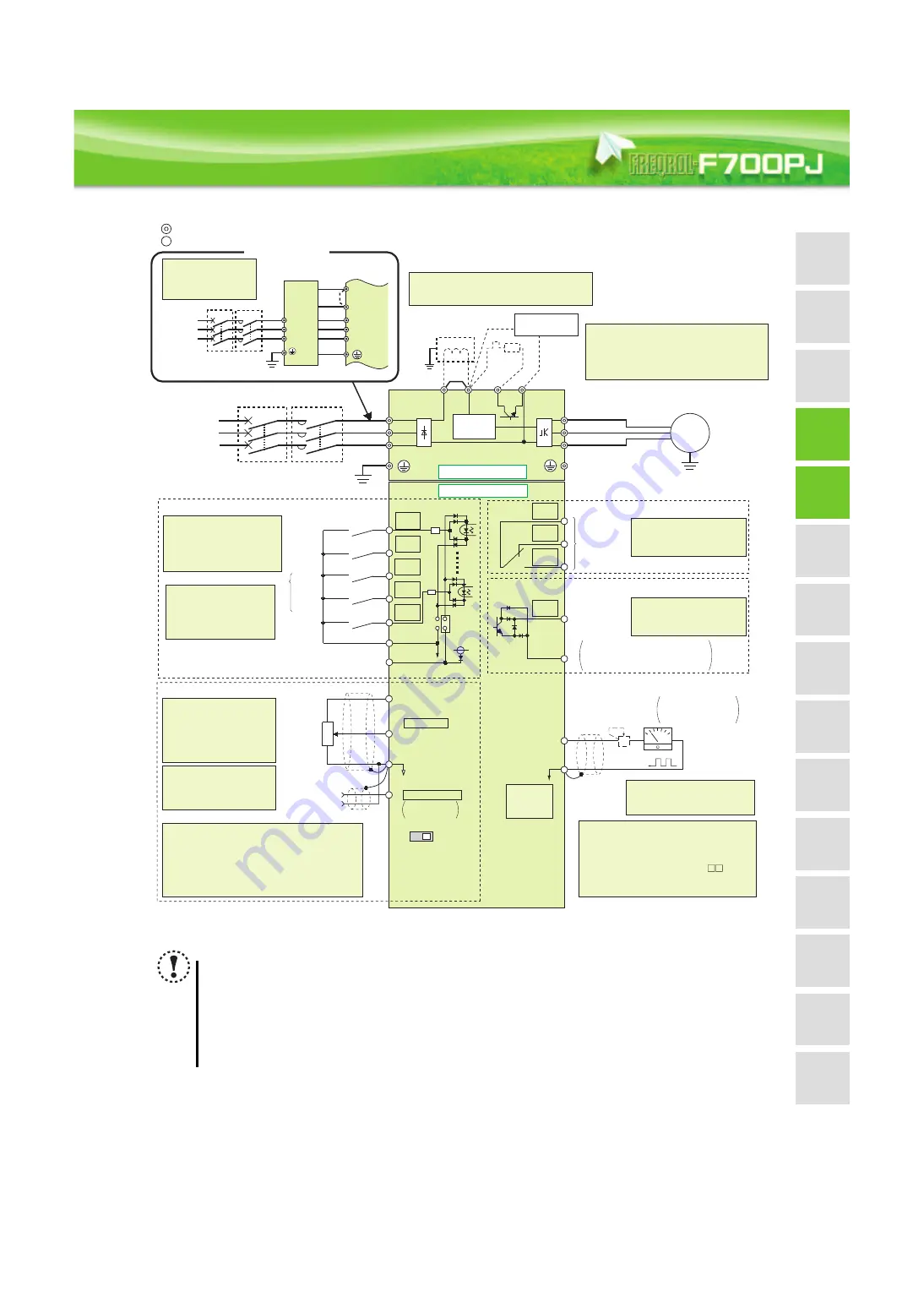
Features
Options
Precautions
Motor
Connection
example
Standard
specs.
Outline
dimensions
Parameter
list
Parameter
descriptions
Protective
functions
IPM motor
control
Compatibility
W
a
rranty
Te
rminal connection
diagrams
T
e
rminal specs.
Operation panel
Parameter unit
FR Configurator
17
Terminal Connection Diagram
NOTE
To prevent a malfunction caused by noise, separate the signal cables more than 10cm from the power cables. Also
separate the main circuit wire of the input side and the output side.
After wiring, wire offcuts must not be left in the inverter.
Wire offcuts can cause an alarm, failure or malfunction. Always keep the inverter clean. When drilling mounting holes
in an enclosure etc., take care not to allow chips and other foreign matter to enter the inverter.
The terminals S1, S2, SC, and SO are for manufacturer setting. Do not remove the shortening wires across the
terminals S1 and SC and the terminals S2 and SC.
Earth
(Ground)
Motor
M
Earth (Ground)
Three-phase
AC power
supply
MCCB
MC
R/L1
P1
P/+
PR N/-
S/L2
T/L3
U
V
W
Earth
(Ground)
Forward
rotation
start
Reverse
rotation
start
Middle
speed
High
speed
Terminal 4
input
selection
Control input signals (No voltage input allowed)
24VDC power supply
(Common for external power supply transistor)
STR
STF
RH
RM
AU
SD
PC
Relay output
Relay output
(Fault output)
Running
Open collector output
Open collector output common
Sink/source common
RUN
SE
A
B
C
FM
SD
Indicator
(Frequency meter, etc.)
-
Moving-coil type
1mA full-scale
Calibration resistor
Frequency setting signals (Analog)
2 0 to 5VDC
10(+5V)
2
3
1
4 4 to 20mADC
Frequency
setting
potentiometer
1/2W1k
Ω
Terminal 4
input
(Current input)
(+)
(-)
5(Analog common)
∗5
It is recommended to use
2W1k
Ω
when the
frequency setting signal
is changed frequently.
∗5
∗4
Terminal input specifications
can be changed by analog
input specifications
switchover
(Pr. 73)
.
Terminal 10 and terminal 2
are used as PTC input
terminal
(Pr. 561)
.
∗3
When using terminals
PC-SD as a 24VDC
power supply, take care
not to short across
terminals PC and SD.
PU
connector
∗8
It is not necessary when
calibrating the indicator from
the operation panel.
∗2
DC reactor (FR-HEL)
When connecting a DC reactor, remove the
jumper across P1 and P/+.
Control circuit terminal
Main circuit terminal
Sink logic
Jumper
∗2
∗7
∗3
∗4
∗6
∗8
The function of these
terminals can be changed to
the reset signal, etc. with the
input terminal assignment
(Pr. 178 to Pr. 182)
.
Multi-speed
Terminal functions vary by
Pr. 190 RUN terminal
function selection
Terminal functions vary by
Pr. 192 A,B,C terminal
function selection
SINK
SOURCE
V
I
∗6
0 to 5VDC
(0 to 10VDC)
0 to 10VDC
∗6
Terminal input specifications can be changed by analog
input specifications switchover
(Pr. 267)
. Set the
voltage/current input switch in the "
V
" position to select
voltage input (0 to 5V/0 to10V) and "
I
" (initial value) to
select current input (4 to 20mA).
To use terminal 4 (initial setting is current input), set "4"
in any of
Pr.178 to Pr.182 (input terminal function selection)
to assign the function, and turn ON AU signal.
Brake unit
(Option)
Voltage/current
input switch
Main circuit
Control circuit
R
Contact input common
With Filterpack
Three-phase
AC power
supply
MCCB
MC
R/L1
P1
P/+
S/L2
T/L3
Earth (ground)
∗1
Remove the jumper
across the terminals
P1 and P/+ to install
Filterpack.
Jumper
∗1
R0
S0
T0
P1
P
Filterpack
FR-BFP2
Inverter
GND
R
S
T
∗9
∗9
Operation and parameter setting can be done
from the parameter unit (FR-PU07) and the
enclosure surface operation panel (FR-
PA07).
(Use the option cable (FR-CB2 ).)
RS-485 communication can be utilized from
a personal computer and other devices.
+
24V
Inrush current
limit circuit
∗7
Brake resistor (FR-ABR, MRS type, MYS type)
Install a thermal relay to prevent an overheat
and burnout of the brake resistor.
Always install a thermal relay when using a
brake resistor whose capacity is 11K or higher.
Summary of Contents for F720PJ-11KF
Page 88: ...88 MEMO ...