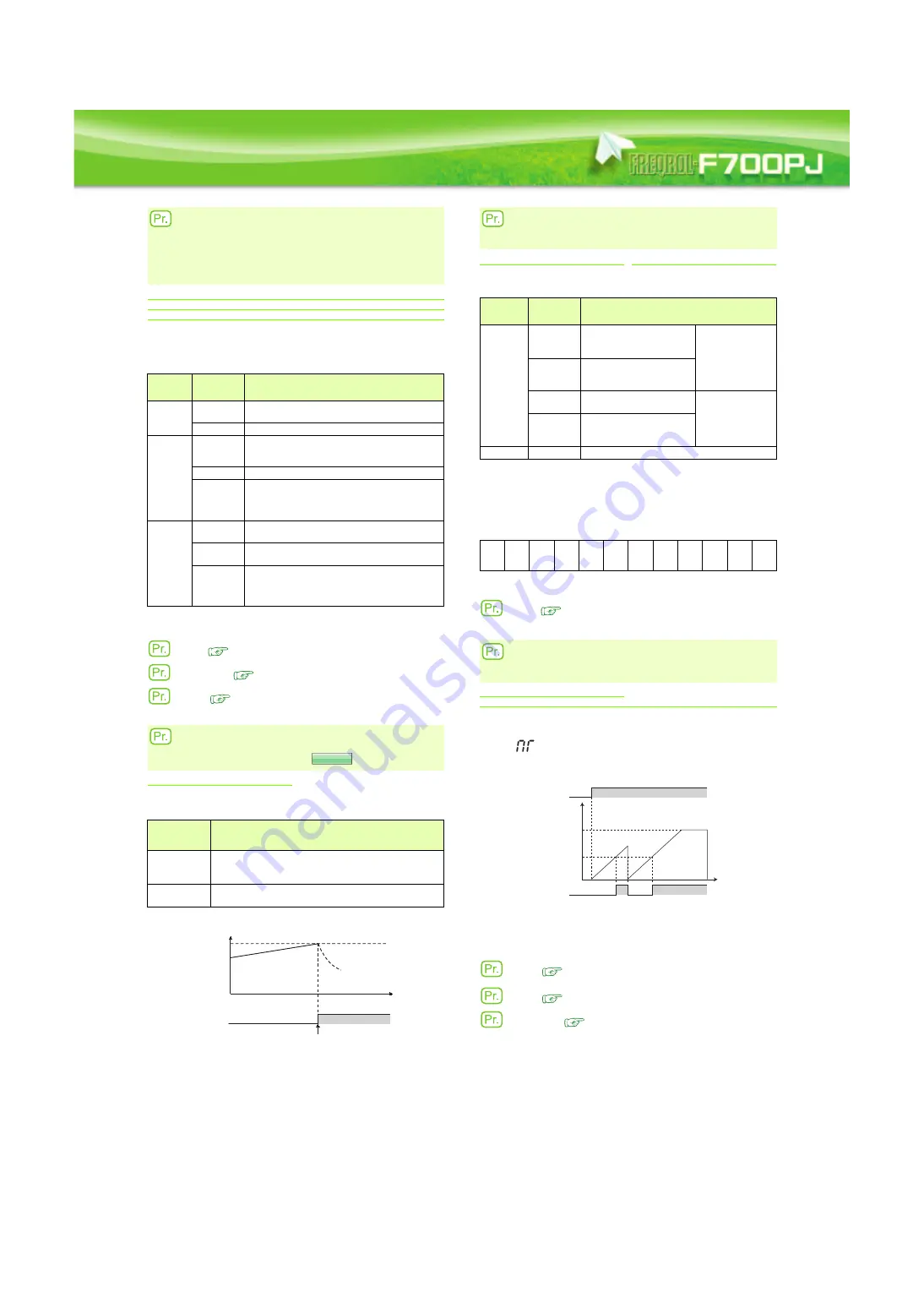
52
When setting parameters, refer to the instruction manual (applied) and understand instructions.
When the RS-485 communication with the PU connector is used,
the external start command and frequency command can be valid.
Command source in the PU operation mode can be selected.
Pr. 551
is always write-enabled.
Inverter outputs are stopped when the motor speed exceeds the
Pr.374 Overspeed detection level
under IPM motor control.
You can utilize the ON/OFF of the inverter's output signals instead
of the remote output terminal of the programmable controller.
This parameter allows its setting to be changed during operation in any
operation mode even if "0" (initial value) is set in
Pr. 77 Parameter write
selection
.
<Remote output data>
When the cumulative energization time of the inverter reaches the
parameter set time, the maintenance timer output signal (Y95) is
output.
(MT) is displayed on the operation panel.
This can be used as a guideline for the maintenance time of
peripheral devices.
The cumulative energization time of the inverter is stored into the
EEPROM every hour and indicated in
Pr. 503 Maintenance timer
in
100h increments.
Pr. 503
is clamped at 9998 (999800h)
.
338, 339, 551
Operation command source and speed
command source during
communication operation
Pr.338 Communication operation command source
Pr.339 Communication speed command source
Pr.551 PU mode operation command source selection
Pr.
Number
Setting
Range
Description
338
0 (initial
value)
Start command source communication
1
Start command source external
339
0
(initial
value)
Frequency command source communication
1
Frequency command source external
2
Frequency command source external (When
there is no external input, the frequency
command via communication is valid, and the
frequency command from terminal 2 is invalid.)
551
2
PU connector is the command source when PU
operation mode.
4
Operation panel is the command source when
PU operation mode.
9999
(initial
value)
Parameter unit automatic recognition
Normally, operation panel is the command
source. When the parameter unit is connected to
the PU connector, PU is the command source.
340
Refer to the section about
Pr.79
342, 343
Refer to the section about
Pr.117
450
Refer to the section about
Pr.71
374
Overspeed detection
Pr.374 Overspeed detection level
Pr.374
Setting
Description
0 to 400Hz
When the motor speed exceeds the speed set in
Pr.374
,
overspeed (E.OS) occurs, and the inverter outputs are
stopped.
9999
(initial value)
No function
IPM
IPM
IPM
ALM
Motor speed
Time
E.OS
Coast to stop
ON
Pr. 374
495, 496
Remote output function (REM signal)
Pr.495 Remote output selection
Pr.496 Remote output data 1
Pr.
Number
Setting
Range
Description
495
0
(initial
value)
Remote output data clear
at powering OFF
Remote output
data is cleared
during an inverter
reset
1
Remote output data
retention even at powering
OFF
10
Remote output data clear
at powering OFF
Remote output
data is retained
during an inverter
reset
11
Remote output data
retention even at powering
OFF
496
0 to 4095
Refer to the following diagram.
Pr.496
b11
b0
AB
C
RUN
As desired (Always "0" during reading)
502
Refer to the section about
Pr.117
503, 504
Part maintenance
Pr.503 Maintenance timer
Pr.504 Maintenance timer alarm output set time
549
Refer to the section about
Pr.117
551
Refer to the section about
Pr.338
553, 554
Refer to the section about
Pr.127
First power
Time
ON
Maintenance
timer
(
Pr. 503
)
Set "0" in
Pr. 503
Y95 signal
MT display
OFF
ON
ON
Pr. 504
9998
(999800h)
Summary of Contents for F720PJ-11KF
Page 88: ...88 MEMO ...