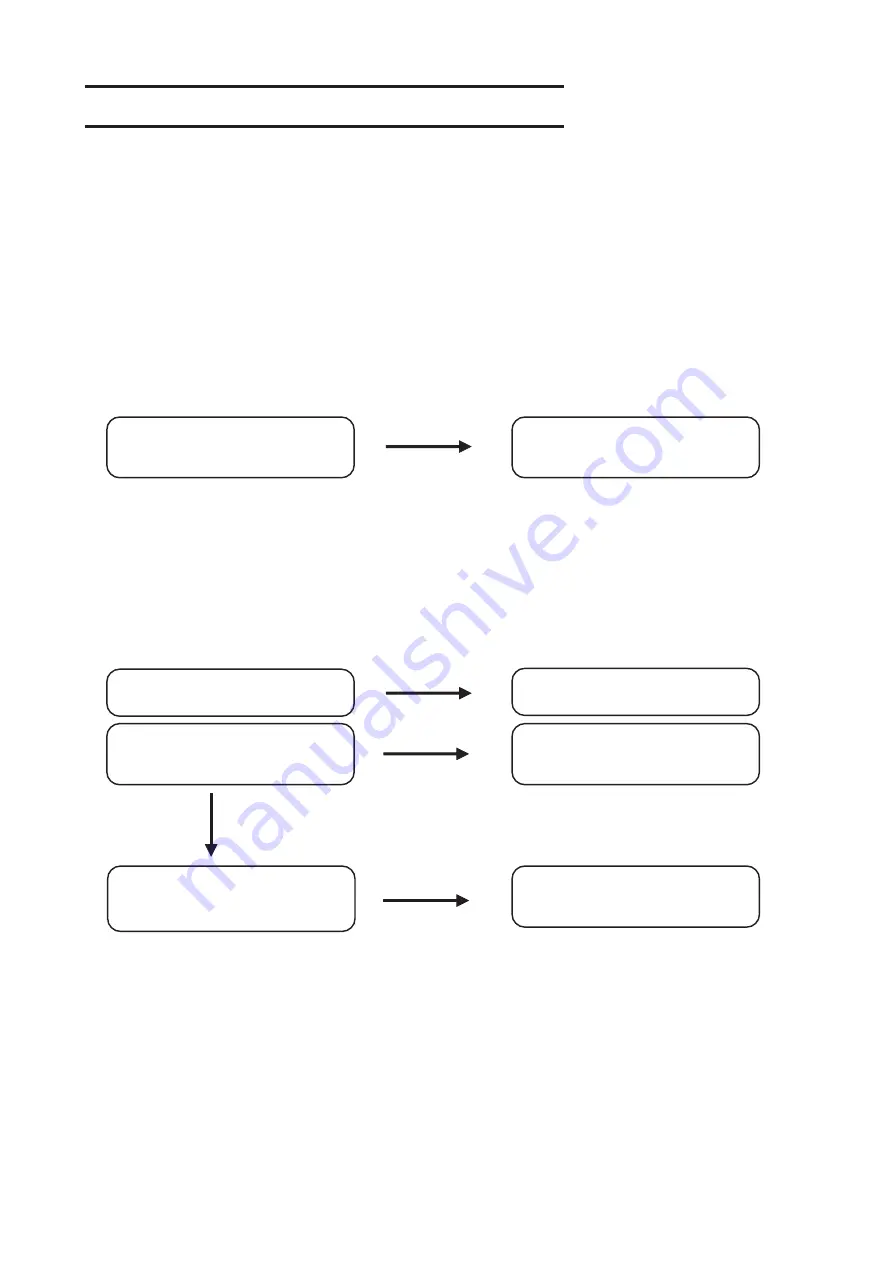
- 5.2 -
Before taking a phenomenon as a sign of failure
Corrective measures against troubles in the case where no error message is given on the
LCD are described in this section. Be sure to take the following measures before taking the
trouble as a sign of failure. If the measures fail restore the plotter to the normal state, contact
your local MIMAKI distributor or MIMAKI office to call for service.
The plotter cannot be energized
More often than not, this is due to improper connection of the power cable. Check that the
power cable has been properly connected to the power outlet and the computer.
The plotter cannot perform printing
This occurs when the data is not being transmitted to the plotter properly. It can also occur
when any of the plotter functions fails or the fabric has been set improperly.
Has the power cable been
connected to the plotter and
the receptacle?
Securely connect the power
cable to them. See page 1.20.
Is the correct interface cable
used?
Has the interface cable been
securely connected in position?
Is the message telling that ink
has run out shown on the
display?
Use the cable exclusive for the
plotter. See page 1.19.
Securely connect the interface
cable in position. See page 1.18.
Replace the ink cartridge with a
new one. See page 2.15.
No
Yes
No
No
No
Summary of Contents for DS-1600
Page 2: ......
Page 110: ......
Page 146: ...4 36...
Page 171: ......
Page 172: ...Printed in Japan D201421 MIMAKI ENGINEERING CO LTD 2006 NH...