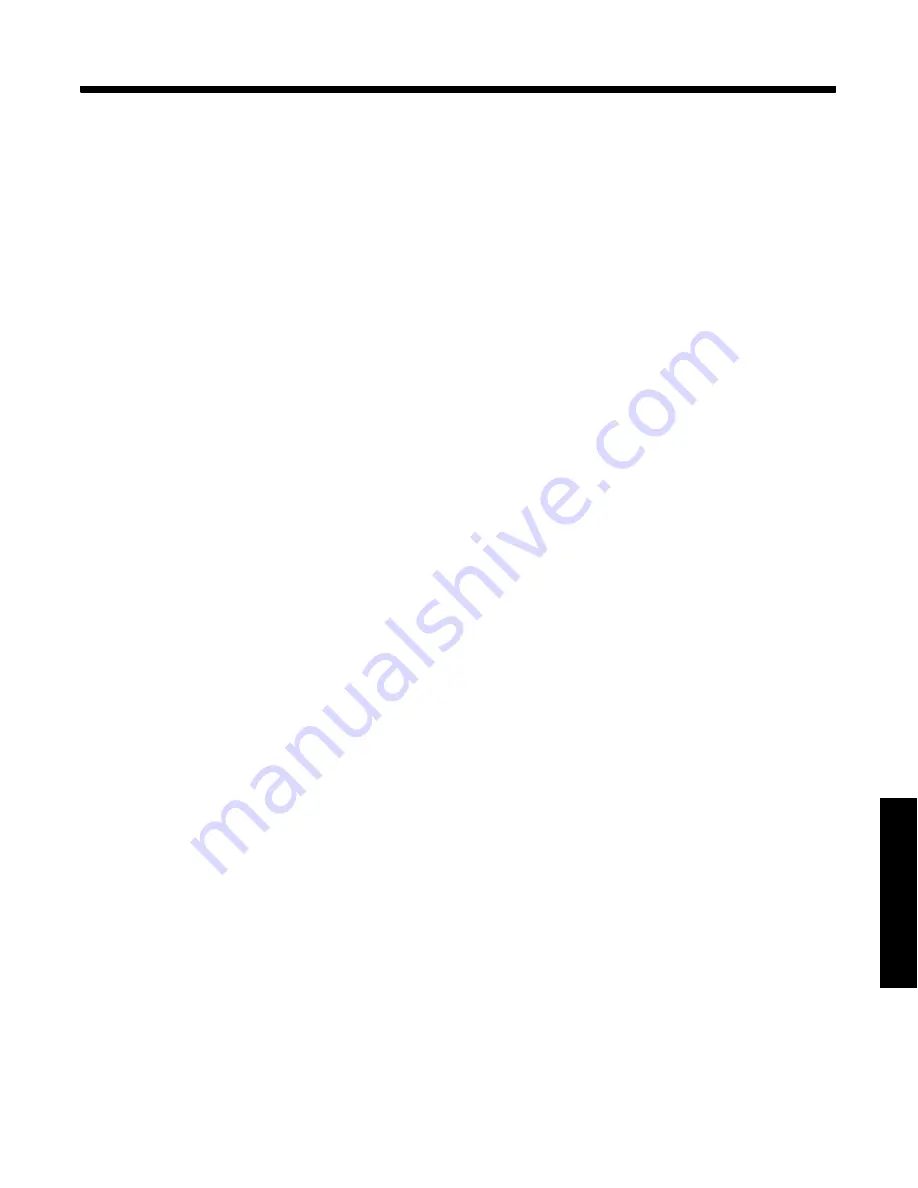
General
OM-257 675 Page 63
SECTION 10
−
OPERATION
10-1. Operational Terms
The following is a list of terms and their definitions as they apply to this interface unit:
General Terms:
Arc Adjust
Term used to represent arc length adjustments in pulse programs. Increasing Arc Adjust increases
the actual arc length. Likewise, decreasing arc adjust shortens arc length. Arc Adjust is replaced by
volts in MIG programs.
AccuCurve
CV Pulse process using a pulse waveform with modified curves at particular locations within the
waveform. Has a distinguished change in arc characteristics. Front panel display is ACCU
−
CURV.
Accu-pulse
Pulse process utilizing constant current ramps with constant voltage control of peaks and
backgrounds. Adaptive response is controlled by peak, background, and minimum current levels.
Benefits are shorter arc lengths, better puddle control, more tolerant of tip-to-work variation, less
audible noise, no arc wandering, allows weld to fill in at toes increasing travel speed and deposition,
and more tolerant to poor fit up and gaps.
Adjust
Control knob used to change or set parameters and functions.
Amps
Indicates average amperage while welding and 3 seconds hold value at end of weld.
Arc Control
Allows setting of inductance and slope in MIG mode. In pulse and Accu-pulse mode, this adjustment
changes the arc characteristics by adjusting the preprogrammed factory pulse data.
Arc Length
Distance from end of wire electrode to weld pool.
Auto Thread
Method of jogging wire without holding jog or trigger switch. By rocking the switch from purge to jog
within 0.5 seconds will automatically feed wire for a factory default setting of 192 in (4877 mm) of wire
before stopping. Default setting is 192 at a feed rate of 700 ipm (these values can be changed using
the HTML pages). Pressing jog, purge, or trigger switch will terminate the auto-threading feature.
Crater
Allows setting of voltage/arc adjust, wire feed rate, and time value for arc ends.
DeviceNet
This is a network system used in the automation industry to interconnect control devices for data
exchange. It uses Controller Area Network as the backbone technology and defines an application
layer to cover a range of device profiles. Typical applications include information exchange, safety
devices, and large I/O control networks.
Ethernet
This is a family of computer networking technologies for local area networks (LANS). Ethernet was
commercially introduced in 1980 and standardized in 1985 as IEEE 802.3. Ethernet hs largely re-
placed competing wired LAN technologies.
Ethernet/IP
(Ethernet Industrial Protocol) is a communications protocol, managed by the Open DeviceNet
Vendors Association (ODVA) and designed for use in process control and other industrial automation
applications.
Feeder Set Up
Allow selection of Sequence and trigger functions.
Gas Type
Selection of shielding gas being used in application.
IGNR (Ignore)
Allows the use of a dual schedule switch between ignore welds and count welds when using Insight
Centerpoint.
Inductance
In short circuit GMAW welding, an increase in inductance will decrease the number of short circuit
transfers per second (provided no other changes are made) and increase the arc-on time. The
increased arc-on time makes the welding puddle more fluid.
MIG
CV weld process with individual settings of voltage and wire speed.
MWCI
Manual Weld Control Interface. A separate remote user interface dedicated to providing arc data
monitoring near the operator’s location. This interface provides the operator with the ability to start a
new part, join welds, or ignore welds. The MWCI has a display for error read-outs and status LEDs.
Preflow
Setting a time value for gas flow prior to arc start.
Postflow
Setting a time value for gas flow after arc end.
Process
A selection made for MIG, Pulse, and Accu-pulse.
Process Set Up
Selection procedure for entering program.
Program
Eight active slots for selection of various processes, wire type, and parameters.
Program Load
Enters selected program information into program slot.
Pulse
Conventional pulse program using peak, background, pulse width, frequency, and peak voltage as
factory taught data. Adaptive method is controlled by frequency adjustment.
Remote Program Select
When Remote Program Select is On, it allows a robot or PLC to select the welding process and para-
meters.programs. When Off, program selection must be done from the welding power source front
panel.
.
Remote Program Select is factory set to “On”. Use the web pages to turn this function “Off”.
When Remote Program Select is “On”, program selection will be determined by remote input once a
weld is initiated. Prior to welding, program selection can be done in a normal manner from the welding
power source front control panel.
Summary of Contents for Auto-Axcess E Digital
Page 6: ......
Page 16: ...OM 257 675 Page 10...
Page 18: ...OM 257 675 Page 12 Notes...
Page 22: ...OM 257 675 Page 16 Notes...
Page 26: ...OM 257 675 Page 20 Notes...
Page 30: ...OM 257 675 Page 24 Notes...
Page 37: ...General OM 257 675 Page 31 Notes...
Page 98: ...Safety OM 257 675 Page 92 Notes...
Page 115: ...Trouble OM 257 675 Page 109 Notes...
Page 121: ...Circuits OM 257 675 Page 115 257 679 A Part 2 Of 2...
Page 123: ...Circuits OM 257 675 Page 117 257 678 A Part 1 Of 2...
Page 125: ...Circuits OM 257 675 Page 119 257 678 A Part 2 Of 2...
Page 127: ...Circuits OM 257 675 Page 121 257 676 A Part 1 Of 2...
Page 129: ...Circuits OM 257 675 Page 123 257 676 A Part 2 Of 2...
Page 130: ...OM 257 675 Page 124 Figure 15 7 Circuit Diagram For Axcess E Digital Module...
Page 131: ...Circuits OM 257 675 Page 125 257 680 A...
Page 132: ...OM 257 675 Page 126 Figure 15 8 Circuit Diagram For Motor And Digital I O Interface...
Page 133: ...Circuits OM 257 675 Page 127 258 246 A...
Page 143: ...E450 Parts OM 257 675 Page 137 Notes...