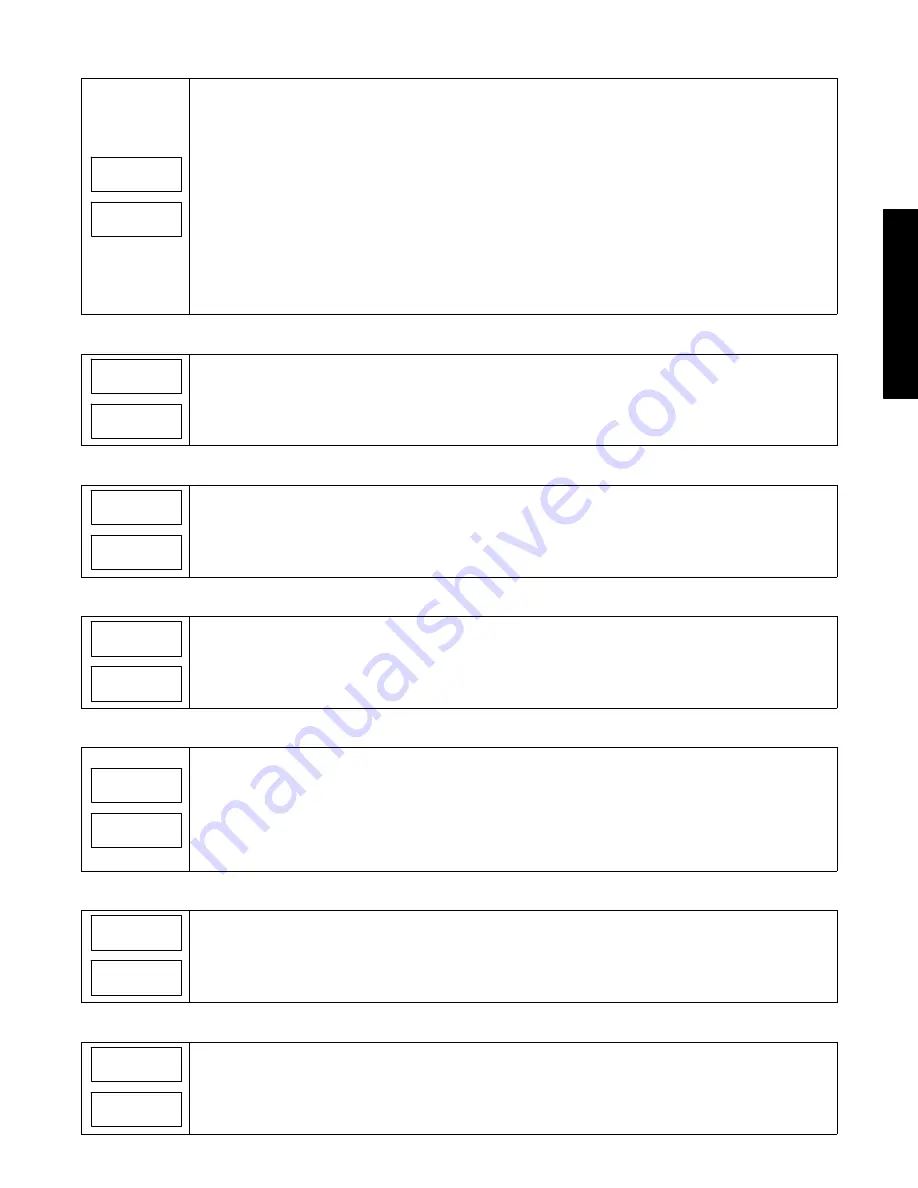
Trouble
OM-257 675 Page 97
A. Emergency Stop Error
E
STOP
Indicates an emergency stop error.
Receptacle RC5-1 connects to receptacle RC1-4 and receptacle RC5-2 connects to receptacle RC4-2 on E-Stop board
PC12. A closure between RC4-1 and RC4-2 24 volts DC to be supplied to the four relays on E-Stop board PC12.
In an E-Stop situation (relays open), all four relays on the E-Stop board de-energize and cut power to the control boards.
When relay CR1 on E-Stop board PC12 is de-energized, it drops out the 18 volts AC from transformer T1 that powers the
inverter control board(s).
When relay CR2 on E-Stop board PC12 is de-energized, it breaks the contactor signal being sent to the inverter engine
board(s) from the process control module PC4 (J2-9 to RC2-3) and causes a loss of signal to the AIM board (RC2-1 and
RC2-2) and to micro input (RC5-3 and RC5-4), signaling an E-Stop is active.
When relay CR3 on E-Stop board PC12 is de-energized, it breaks the secondary side output of the motor board before it
goes to the filter board.
Relay CR4 on E-Stop board PC12 is a soft start relay in parallel with the contacts of relay CR1.
B. Arc Error
ERR
ARC
Indicates voltage has exceeded the programmable limit of a valid arc for the programmed amount of time (default time is
500 ms). Check contact tip, weld conditions, and shielding gas.
Arc error can be enabled or disabled using an optional PDA with File Management/WaveWriter software.
C. No Coolant Flow Error
ERR
COOL
Indicates no coolant flow in water flow switch option. The error may be reset by reestablishing coolant flow to the gun, and
then pressing the Jog/Purge button.
D. Ground Current Detect Error
ERR
GND
Indicates that weld current is flowing through the primary ground. This is a latching error and welding power source power
must be cycled off and back on again.
E. Line Error
ERR
LINE
Indicates that primary power has dropped below the operating point of the welding power source. Signal is sent from in-
verter engine module(s) (RC6, Pin 9 on inverter control board PC1) to process control module PC4 (J2, Pin 1). Check for a
brown-out condition. The primary boost capacitors have dropped below an acceptable minimum voltage threshold.
This circuit monitors the 940 volts primary DC bus voltage across the electrolytic capacitors C1 and C2. Low line is dis-
played when this voltage drops below 858 volts DC. This could happen when attempting to draw near rated output power
with an input voltage below 190 volts AC, three phase. This causes the boost section to go into current limit trying to sup-
ply the output power. Once current limit is reached, the boost section can no longer hold the bus capacitors at 940 volts
DC. The inverter control will also go into an output current limit mode in an attempt to supply output power.
F. Motor Over Current Error
ERR
MOTR
Indicates that the motor has been drawing too much current for too long a time period. To remedy this fault, reduce the wire
feed speed or the wire feeder torque load/duty cycle. Press Jog/Purge button to clear error.
G. Arc Start Error
STRT
ERR
Indicates the contactor either is or was active, but the system failed to start an arc. Conditions for a valid arc start are at
least 50% of arc start current, voltage less than 60 volts, and voltage greater than min. valid arc voltage (default is 22.5
volts). This situation is usually attributed to a contact tip or feeder issue. The arc start error parameter can be disabled
using an optional PDA with File Management/Wave Writer software.
Summary of Contents for Auto-Axcess E Digital
Page 6: ......
Page 16: ...OM 257 675 Page 10...
Page 18: ...OM 257 675 Page 12 Notes...
Page 22: ...OM 257 675 Page 16 Notes...
Page 26: ...OM 257 675 Page 20 Notes...
Page 30: ...OM 257 675 Page 24 Notes...
Page 37: ...General OM 257 675 Page 31 Notes...
Page 98: ...Safety OM 257 675 Page 92 Notes...
Page 115: ...Trouble OM 257 675 Page 109 Notes...
Page 121: ...Circuits OM 257 675 Page 115 257 679 A Part 2 Of 2...
Page 123: ...Circuits OM 257 675 Page 117 257 678 A Part 1 Of 2...
Page 125: ...Circuits OM 257 675 Page 119 257 678 A Part 2 Of 2...
Page 127: ...Circuits OM 257 675 Page 121 257 676 A Part 1 Of 2...
Page 129: ...Circuits OM 257 675 Page 123 257 676 A Part 2 Of 2...
Page 130: ...OM 257 675 Page 124 Figure 15 7 Circuit Diagram For Axcess E Digital Module...
Page 131: ...Circuits OM 257 675 Page 125 257 680 A...
Page 132: ...OM 257 675 Page 126 Figure 15 8 Circuit Diagram For Motor And Digital I O Interface...
Page 133: ...Circuits OM 257 675 Page 127 258 246 A...
Page 143: ...E450 Parts OM 257 675 Page 137 Notes...