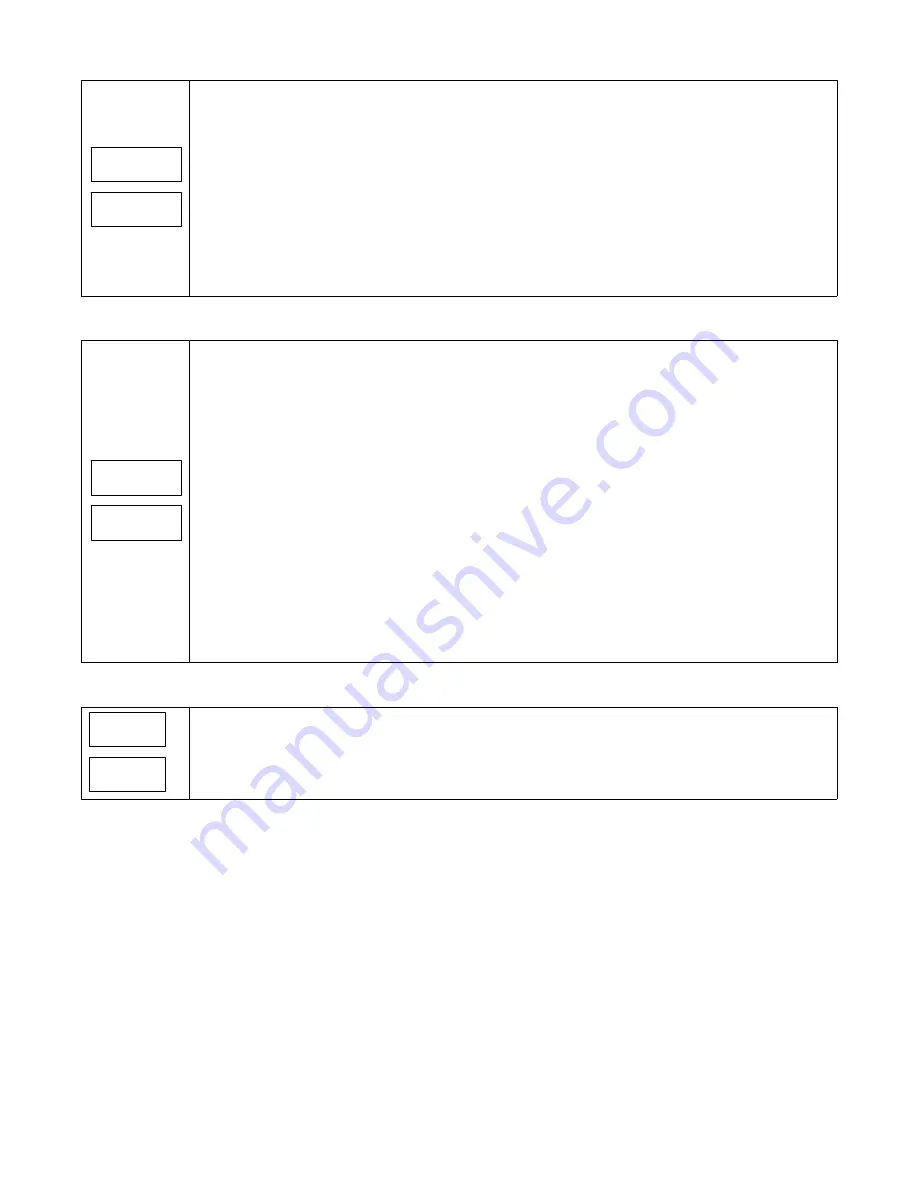
OM-257 675 Page 98
H. No Tach Error
ERR
TACH
Indicates loss of tachometer feedback. Determine cause of error as follows:
S
Press JOG button on the front panel.
S
Does the motor run wide open immediately?
S
YES
Replace Motor Board PC6.
S
Does the motor ramp up in speed?
S
YES
Bad motor tach. Contact nearest Factory Authorized Service Agent.
S
Does the motor respond at all?
S
YES
Contact nearest Factory Authorized Service Agent.
S
Check motor cable. Is it damaged?
S
YES
Replace motor cable.
S
NO
Contact factory service personnel.
I.
Thermal Over Temperature Error
ERR
TEMP
Indicates one or more of the inverter engines overheated. Sent from inverter engine module(s) (RC6, Pin 12, on inverter
control board PC1) to process control module PC4 (J2, Pin 7). Check fan on inverter engine(s) and weld currents.
This signal is the sum of two conditions: shutdown that comes from the temperature monitoring circuit on the inverter con-
trol board, and Pwr-Up-Cnt that generated by the boost section of the inverter control board. When either of these signals
is active, RC6-12 is pulled low (this is the not ready line out of the inverter control board).
Shutdown is active when there is an over-temperature condition on the primary or secondary heatsink or on the boost
inductor. To determine which of the two locations is at fault, check LED 1 and LED 2 on inverter control board PC1.
S
If LED 1 is lit, this indicates an over-temperature condition on the primary heat sink.
S
If LED 2 is lit, this indicates an over-temperature condition on the secondary heat sink or on the boost inductor.
Pwr-Up-Cnt (power up control) monitors primary voltage start-up conditions when the power source is first turned on. This
signal is opto-isolated from the boost section of the inverter control board. The following conditions must be met for the
power source to power up:
S
Auxiliary power board PC3 must be powered up and operating to supply prepower of +15 volts DC to the boost sec-
tion of inverter control board PC1.
S
The peak voltage of the input line power must be greater than 150 volts peak.
S
The DC bus voltage must be greater than 85% of the rectified line voltage. This bus voltage also turns on the
pre-charge relay.
S
The DC bus voltage must be boosted to greater than 858 volts DC.
If any of these conditions are not met, then receptacle RC6-12 is pulled low and weld output is locked out.
J. Unknown Error
ERR
UNKN
Indicates error bit from process control module PC4 is set, but error value sent does not match anything defined with the
UIM board PC7.
Summary of Contents for Auto-Axcess E Digital
Page 6: ......
Page 16: ...OM 257 675 Page 10...
Page 18: ...OM 257 675 Page 12 Notes...
Page 22: ...OM 257 675 Page 16 Notes...
Page 26: ...OM 257 675 Page 20 Notes...
Page 30: ...OM 257 675 Page 24 Notes...
Page 37: ...General OM 257 675 Page 31 Notes...
Page 98: ...Safety OM 257 675 Page 92 Notes...
Page 115: ...Trouble OM 257 675 Page 109 Notes...
Page 121: ...Circuits OM 257 675 Page 115 257 679 A Part 2 Of 2...
Page 123: ...Circuits OM 257 675 Page 117 257 678 A Part 1 Of 2...
Page 125: ...Circuits OM 257 675 Page 119 257 678 A Part 2 Of 2...
Page 127: ...Circuits OM 257 675 Page 121 257 676 A Part 1 Of 2...
Page 129: ...Circuits OM 257 675 Page 123 257 676 A Part 2 Of 2...
Page 130: ...OM 257 675 Page 124 Figure 15 7 Circuit Diagram For Axcess E Digital Module...
Page 131: ...Circuits OM 257 675 Page 125 257 680 A...
Page 132: ...OM 257 675 Page 126 Figure 15 8 Circuit Diagram For Motor And Digital I O Interface...
Page 133: ...Circuits OM 257 675 Page 127 258 246 A...
Page 143: ...E450 Parts OM 257 675 Page 137 Notes...