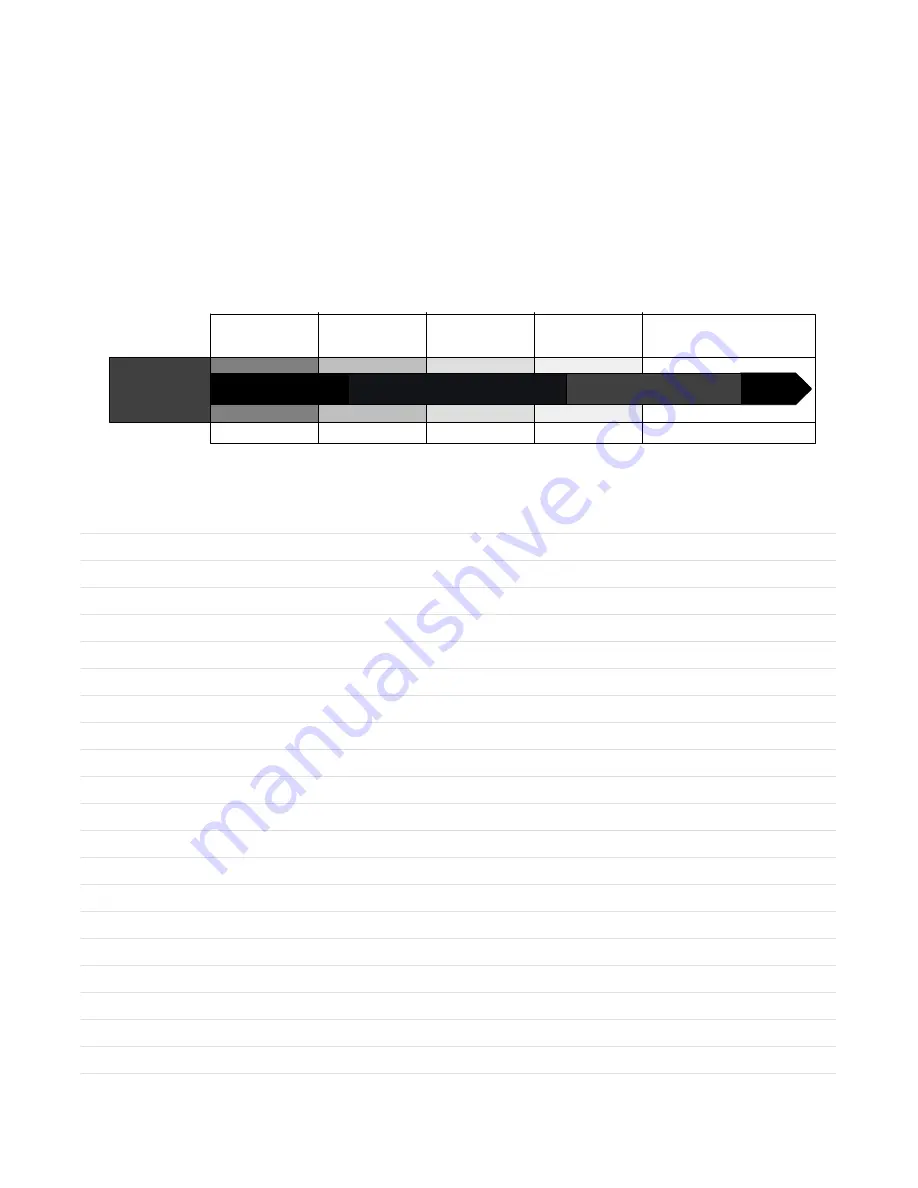
OM-257 675 Page 36
9-3. Automated Welding Equipment Recommendations
Planning proper layout and routing of welding cables and control cables should be considered when setting up automated equipment.
1.
Whenever possible all cables should be routed out of the path of moving equipment.
2.
Cable installation in a stationary position will decrease the likelihood of wires breaking down in the cable.
3.
Cables that are moving will breakdown over time. This time can be increased by making sure there are no stress points when installing cables,
and deciding how and where to tie cables down.
4.
If at all possible, do not route weld cables and control cables together. Leave as much space as reasonable between the weld cables and any
other control cables. Welding generates electrical noise which is present on the weld cables (see 9-9 for grounding information).
9-4. Process Considerations
To obtain the most performance from the welding equipment, it is important to use the right transfer mode for the application. There are no hard and fast
rules, but there are general guidelines to follow when making a selection. The transfer modes available depend on the power source being used. The
possible transfer modes are as follows: Short Arc, Spray, Pulsed Spray, Accu-pulse, and RMD (Regulated Metal Deposition).
Weld Puddle
Control
Process
Standard
Spray
Pulsed
Spray
Accu-pulse
t
Standard
Short Circuit
RMD
t
Regulate Metal
Deposition
Flat/Horizontal
All Position Performance
Thin Material/Gap Filling
Note: To achieve optimum performance, 4/0 welding secondary cable is recommended and the supplied work sense lead must be
connected as close to the arc as possible.
Notes
Summary of Contents for Auto-Axcess E Digital
Page 6: ......
Page 16: ...OM 257 675 Page 10...
Page 18: ...OM 257 675 Page 12 Notes...
Page 22: ...OM 257 675 Page 16 Notes...
Page 26: ...OM 257 675 Page 20 Notes...
Page 30: ...OM 257 675 Page 24 Notes...
Page 37: ...General OM 257 675 Page 31 Notes...
Page 98: ...Safety OM 257 675 Page 92 Notes...
Page 115: ...Trouble OM 257 675 Page 109 Notes...
Page 121: ...Circuits OM 257 675 Page 115 257 679 A Part 2 Of 2...
Page 123: ...Circuits OM 257 675 Page 117 257 678 A Part 1 Of 2...
Page 125: ...Circuits OM 257 675 Page 119 257 678 A Part 2 Of 2...
Page 127: ...Circuits OM 257 675 Page 121 257 676 A Part 1 Of 2...
Page 129: ...Circuits OM 257 675 Page 123 257 676 A Part 2 Of 2...
Page 130: ...OM 257 675 Page 124 Figure 15 7 Circuit Diagram For Axcess E Digital Module...
Page 131: ...Circuits OM 257 675 Page 125 257 680 A...
Page 132: ...OM 257 675 Page 126 Figure 15 8 Circuit Diagram For Motor And Digital I O Interface...
Page 133: ...Circuits OM 257 675 Page 127 258 246 A...
Page 143: ...E450 Parts OM 257 675 Page 137 Notes...