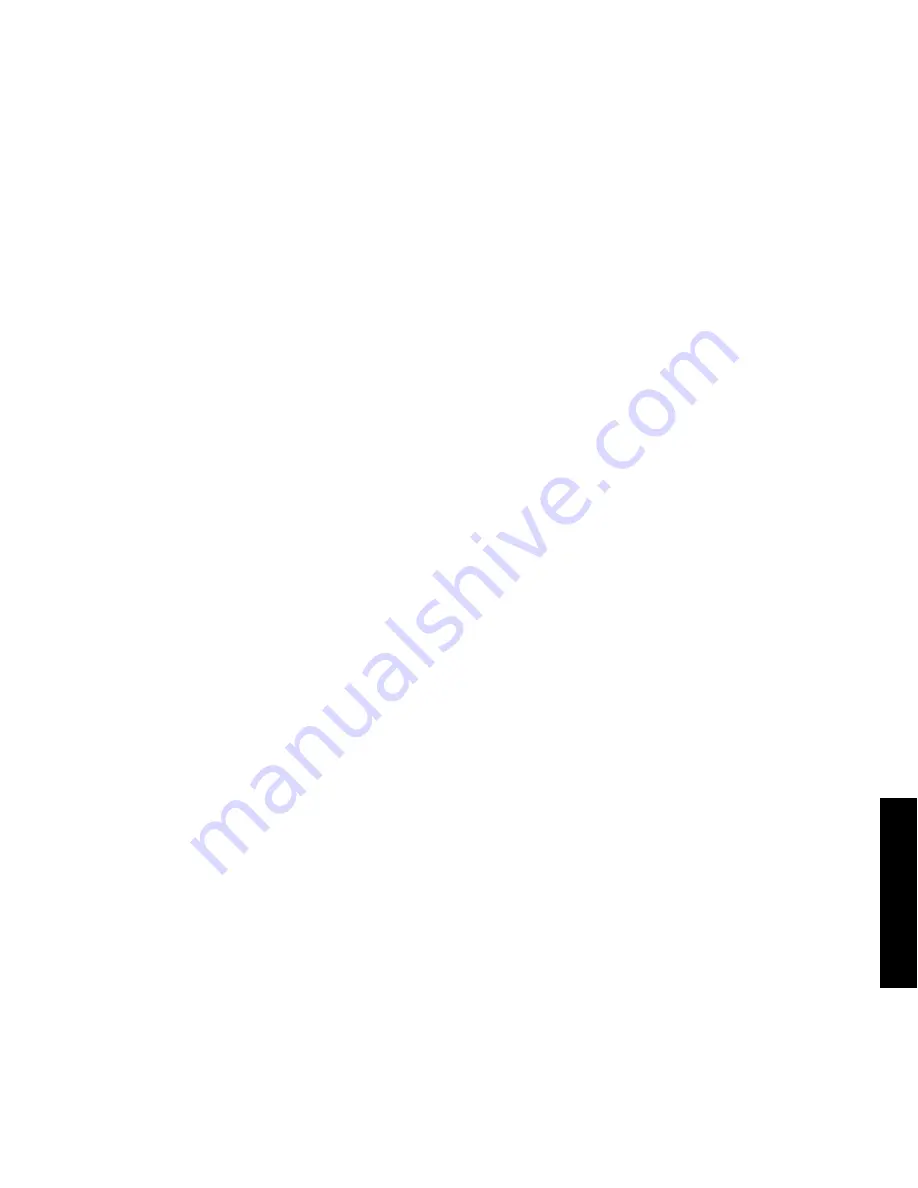
General
OM-257 675 Page 61
9-19. Electrical Functions Of Automated Welding Systems
Several important items to know about any automated welding system are as follows:
1.
To troubleshoot any system, determine the functions of the individual parts of the system.
2.
Determine what inputs and outputs are needed to control the timing, amount of weld output, and the movements of the part or welding gun.
3.
Determine where the previous mentioned signals come from e.g. PLC, robot, or from within an interface device.
4.
Determine which functions ar not occurring properly and troubleshoot the appropriate circuit or replace the faulty component in the system.
A. Function Of Power Sources
1.
Turns weld power on/off (commonly referred to as contactor).
2.
Controls weld output (voltage in CV mode and amperage in CC mode).
B. Function Of Fixed Automation Interface Using Digital Communications
1.
Signals the power source to turn on weld output.
2.
Energizes the gas solenoid.
3.
Energizes the wire drive motor.
4.
Controls the wire speed.
5.
Signals the power source as to how much output to deliver (voltage or amperage depending on weld process).
6.
Controls the timing of the a weld sequence that is dictated by the interface or some of the weld sequence that is dictated by the interface or
some external remote device such as a PLC.
7.
Typically sends an arc established signal through the use of a relay closure.
C. Function Of Programmable Logic Controller (PLC)
PLC sets weld and part number for arc data monitoring. This function requires the ADAM
−
6050 when using DeviceNet communications.
1.
Receives inputs from external devices such as the relay closure from an automation interface to determine arc initiation or arc error, or any
safety features that may prevent the start of a weld cycle or shut down the system to prevent injuries.
2.
Controls external devices with the use of electronic switches such as starting the motor that rotates the workpiece.
3.
Controls the timing of the weld cycle and movement of the workpiece or the welding gun through the programming of the PLC.
D. Function Of Limit Switches/Proximity Switches
1.
Limit switches are used to determine mechanical position of workpieces, positioners, guns, or for safety devices. These switches are either
open or closed.
E. Function Of Flexible Automation Interfaces Using Digital Communications
1.
Signals the power source to turn on weld output.
2.
Energizes the gas solenoid.
3.
Energizes the wire drive motor.
4.
Controls wire speed by using internal commands or analog commands from the robot controller.
5.
Signals the power source for amount of weld output to deliver (voltage or amperage depending on weld process) using internal commands or
analog commands from the robot controller.
6.
Accept or ignore wire speed and voltage analog signals from the robot controller.
7.
Control weld sequence timing as directed by the interface or robot controller.
8.
Send an arc established signal using a relay closure.
9.
Accept an arc on signal from the robot controller.
10.
Check current flow to determine if wire is stuck to the workpiece at the end of a weld.
11.
Provides a remote E-Stop.
12.
Accepts a remote purge signal.
13.
Accepts a remote jog signal for forward or reverse.
14.
Provides arc error output relays.
15.
Receives remote program select signals to allow program changes while welding or at the start of any weld.
16.
Sets weld and part number for arc data monitoring. This function requires the ADAM
−
6050 when using DeviceNet communications.
There are three modes of interface operations available depending on robot controller capabilities:
1.
Arc On, No Analog (power source) mode uses the robot controller to send a signal to start the welding process and the interface controls the
timing of the weld sequence (preflow, run-in, start time, weld, crater, and postflow).
2.
Arc On, Analog (shared control) mode uses the robot controller to send a signal to start the welding process and send analog commands to the
interface to control the amount of weld output and wire speed. The interface will still control preflow, run-in, start time, and postflow.
Summary of Contents for Auto-Axcess E Digital
Page 6: ......
Page 16: ...OM 257 675 Page 10...
Page 18: ...OM 257 675 Page 12 Notes...
Page 22: ...OM 257 675 Page 16 Notes...
Page 26: ...OM 257 675 Page 20 Notes...
Page 30: ...OM 257 675 Page 24 Notes...
Page 37: ...General OM 257 675 Page 31 Notes...
Page 98: ...Safety OM 257 675 Page 92 Notes...
Page 115: ...Trouble OM 257 675 Page 109 Notes...
Page 121: ...Circuits OM 257 675 Page 115 257 679 A Part 2 Of 2...
Page 123: ...Circuits OM 257 675 Page 117 257 678 A Part 1 Of 2...
Page 125: ...Circuits OM 257 675 Page 119 257 678 A Part 2 Of 2...
Page 127: ...Circuits OM 257 675 Page 121 257 676 A Part 1 Of 2...
Page 129: ...Circuits OM 257 675 Page 123 257 676 A Part 2 Of 2...
Page 130: ...OM 257 675 Page 124 Figure 15 7 Circuit Diagram For Axcess E Digital Module...
Page 131: ...Circuits OM 257 675 Page 125 257 680 A...
Page 132: ...OM 257 675 Page 126 Figure 15 8 Circuit Diagram For Motor And Digital I O Interface...
Page 133: ...Circuits OM 257 675 Page 127 258 246 A...
Page 143: ...E450 Parts OM 257 675 Page 137 Notes...