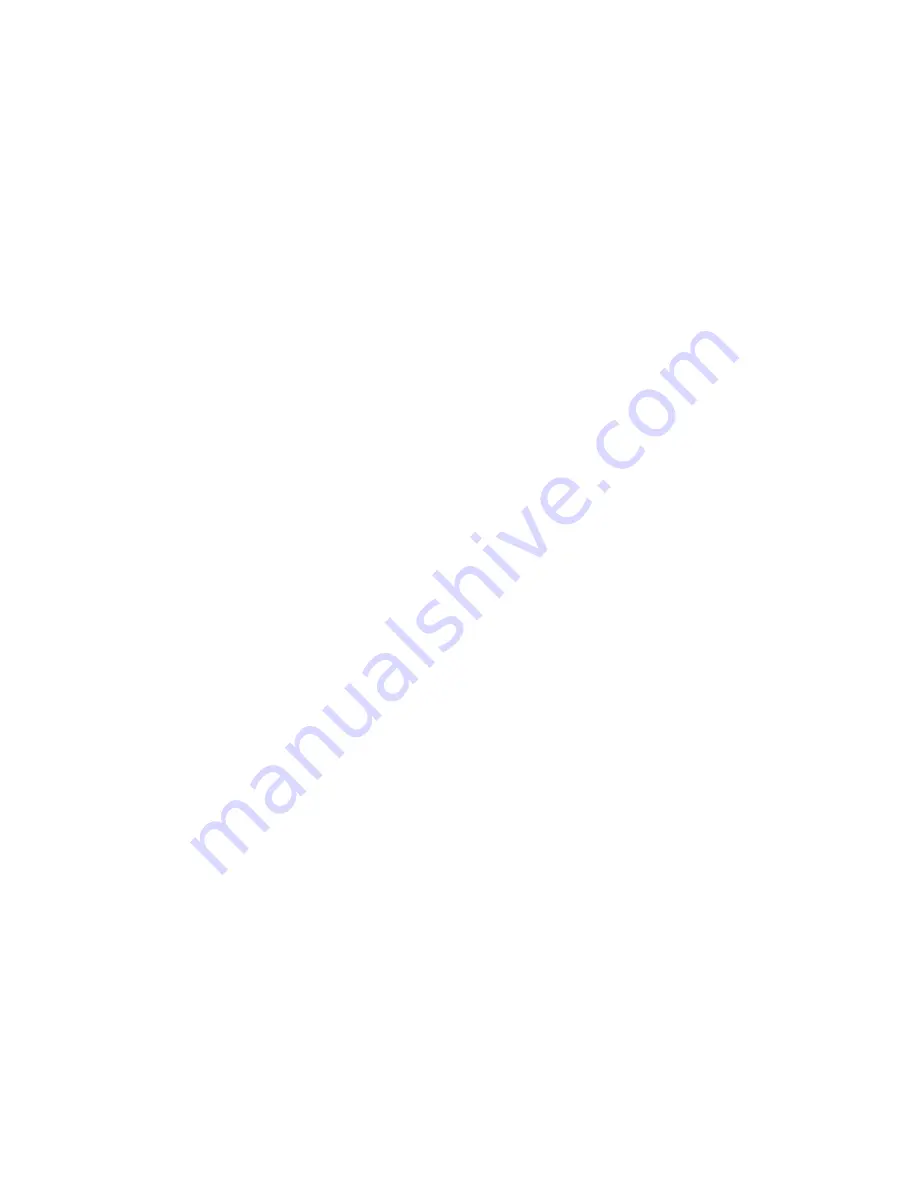
OM-257 675 Page 62
3.
PS, Wire, Gas, & Analog (robot control) mode use the robot controller to send a signal to start gas flow, a signal to start the wire feed motor, and
a signal to energize the power source. The robot controller also sends analog commands to the interface to control the amount of weld output
and wire speed.
.
One of the three modes is selected to match the capabilities and intended use of the robot controller. The Arc On, No Analog mode is a good
selection for testing the interface and power source functions in a system.
The requirements for making a MIG weld are as follows:
1.
The gas solenoid must be energized.
2.
The power source must be energized.
3.
The wire drive motor must be turned on.
4.
A wire speed command must be present at the main control board in the power source.
5.
A weld output command must be present at the main control board in the power source.
F. Function Of Gas Flow
The gas solenoid can be energized for a weld in one of two ways, either by a remote start signal from an external device or by a gas on signal from an
external device. The signal type will depend on system setup and is important to know when troubleshooting a shielding gas problem in the welding
operation. Severe porosity will occur if there is no signal to energize the gas solenoid or if the gas solenoid fails to energize. Even when the solenoid
energizes, proper gas flow and gas mixture are necessary to obtain a good quality weld.
G. Function Of Power Source Open Circuit Voltage
The power source requires two signals to start and control weld output. First, a start signal to energize the power source in an automated system is
provided by an input signal from an external device (normally referred to as arc on, start, or contactor). The actual turning on of the power source may
also be dependent on the sequencing information programmed into the interface or robot controller. The power source should energize at the same time
the drive motor turns on which will occur after preflow given there is preflow time programmed into the weld sequence. If there is no output start signal
from an external device or the power source fails to energize, there will not be any welding. Second, control of weld output is accomplished by an analog
signal (command signal) supplied to the main control board in the power source. This command signal is provided by an interface to the power source.
Control of the signal is established by settings in the interface or by analog signals from a robot controller. If the command signal is not present, the result
will be either an arc initiation error or noodle welding at the workpiece.
H. Function Of Drive Motor
The drive motor requires two signals to start wire feeding. First, a motor start signal is needed and this is supplied either internally after the remote start
signal is present and preflow times out if applicable, or a remote jog forward signal is supplied from a robot controller. Second, an analog wire speed
command signal is supplied through settings on the interface or an analog input from a robot controller. A quality weld is made when wire speed is
matched properly to the weld parameters. If either of the two previously described signals is missing, the result will be an arc initiation error or wire will
burn back to the contact tip depending on the proximity of the gun to the workpiece. These symptoms can also occur if the wire cannot be fed smoothly
from the source to the contact tip. Liners, contact tips, and unspooling devices should all be examined when there is inconsistent or erratic welding.
To achieve a good quality weld, the output must be set properly according to material size and type, joint configuration, gas mix, travel direction, speed,
design consideration, and desired weld appearance.
Summary of Contents for Auto-Axcess E Digital
Page 6: ......
Page 16: ...OM 257 675 Page 10...
Page 18: ...OM 257 675 Page 12 Notes...
Page 22: ...OM 257 675 Page 16 Notes...
Page 26: ...OM 257 675 Page 20 Notes...
Page 30: ...OM 257 675 Page 24 Notes...
Page 37: ...General OM 257 675 Page 31 Notes...
Page 98: ...Safety OM 257 675 Page 92 Notes...
Page 115: ...Trouble OM 257 675 Page 109 Notes...
Page 121: ...Circuits OM 257 675 Page 115 257 679 A Part 2 Of 2...
Page 123: ...Circuits OM 257 675 Page 117 257 678 A Part 1 Of 2...
Page 125: ...Circuits OM 257 675 Page 119 257 678 A Part 2 Of 2...
Page 127: ...Circuits OM 257 675 Page 121 257 676 A Part 1 Of 2...
Page 129: ...Circuits OM 257 675 Page 123 257 676 A Part 2 Of 2...
Page 130: ...OM 257 675 Page 124 Figure 15 7 Circuit Diagram For Axcess E Digital Module...
Page 131: ...Circuits OM 257 675 Page 125 257 680 A...
Page 132: ...OM 257 675 Page 126 Figure 15 8 Circuit Diagram For Motor And Digital I O Interface...
Page 133: ...Circuits OM 257 675 Page 127 258 246 A...
Page 143: ...E450 Parts OM 257 675 Page 137 Notes...