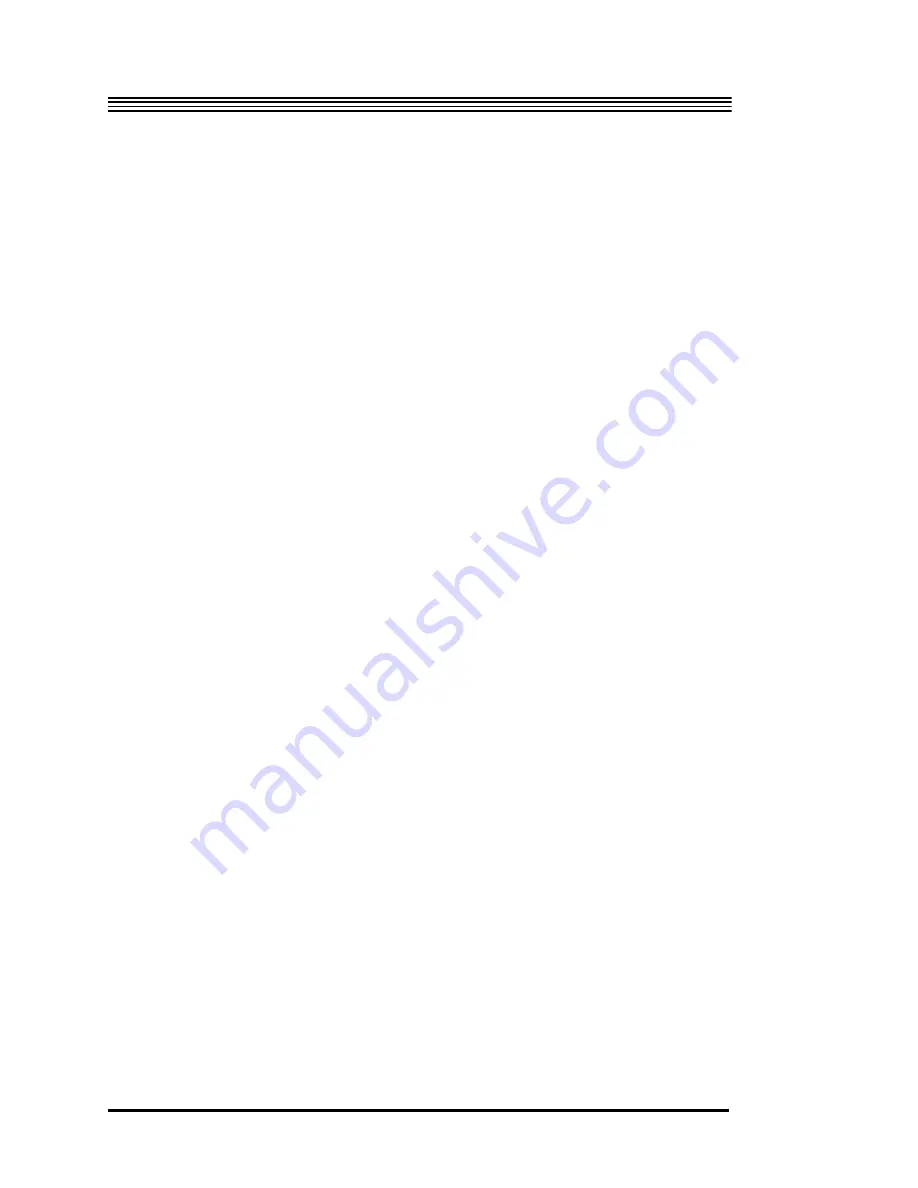
Design: Components and Function
2
motor and the coil and magnet system, while the aneroid wafer assembly
responds automatically to temperature changes.
A sphere detector system similar to the one used in the Dropping Chamber
provides information on the position of the reference mass relative to the
mainspring support system. An infrared LED and a photo detector are
mounted opposite each other inside the mainspring support housing. A
sphere attached to the bottom of the mass focuses the light from the LED onto
the detector, which transmits the resulting signal to a sphere signal
preamplifier.
The zero-position of the sphere on the test mass can be adjusted by moving
the top of the main spring with a small DC motor with a very large gear ratio
for fine control.
The main servo electronics control, the coil-magnet forcer, moves the main
spring support in such a way to keep the main spring length constant. This
active servo acts to effectively weaken the main spring synthesizing a long
period isolation device. The active period of the Superspring is nominally
about 60 seconds.
2.5.4.LASER CONTROLLER
The laser controller supplies power and enables operator control for the WEO
Model 100 Iodine stabilized laser or the Micro-g Solutions Model AL-1
frequency/intensity stabilized laser. See Chapter 3 for setup and operation.
2.5.5.POWER SUPPLIES
The electronics case contains all the power supplies which are required to
operate the FG5. They consist of two primary units:
The Micro-g Solutions Model 125 Portable Ion Pump Power Supply is located
in the front of the electronics case. It supplies power to the ion pump for both
AC and DC operation. See the Model 125 manual for operating instructions.
2-20
Summary of Contents for FG5
Page 22: ...Design Components and Function 2 Figure 2 10 The Superspring 2 14 ...
Page 31: ...Design Components and Function 2 Figure 2 13 Rotation Monitor 2 23 ...
Page 32: ......
Page 42: ...How to Set Up and Run the FG5 3 3 10 ...
Page 44: ...How to Set Up and Run the FG5 3 Figure 3 2 V Post 3 12 ...
Page 53: ...How to Set Up and Run the FG5 3 1 Backup the data 2 Shut off computer power 3 21 ...
Page 87: ...Adjustment and Maintenance 4 4 29 ...
Page 91: ...Adjustment and Maintenance 4 4 33 ...
Page 104: ...Troubleshooting 5 5 2 ...
Page 117: ...Troubleshooting 5 5 15 ...
Page 131: ...Checklists and Logs Appendix D 9 3 ...
Page 140: ...Checklists and Logs Appendix D Table 9 6 Replacing Drive Belt 9 12 ...
Page 145: ...Checklists and Logs Appendix D Table 9 10 Replace Linear Bearings 9 17 ...
Page 149: ...Checklists and Logs Appendix D Table 9 13 Replace Shaft Encoder 9 21 ...