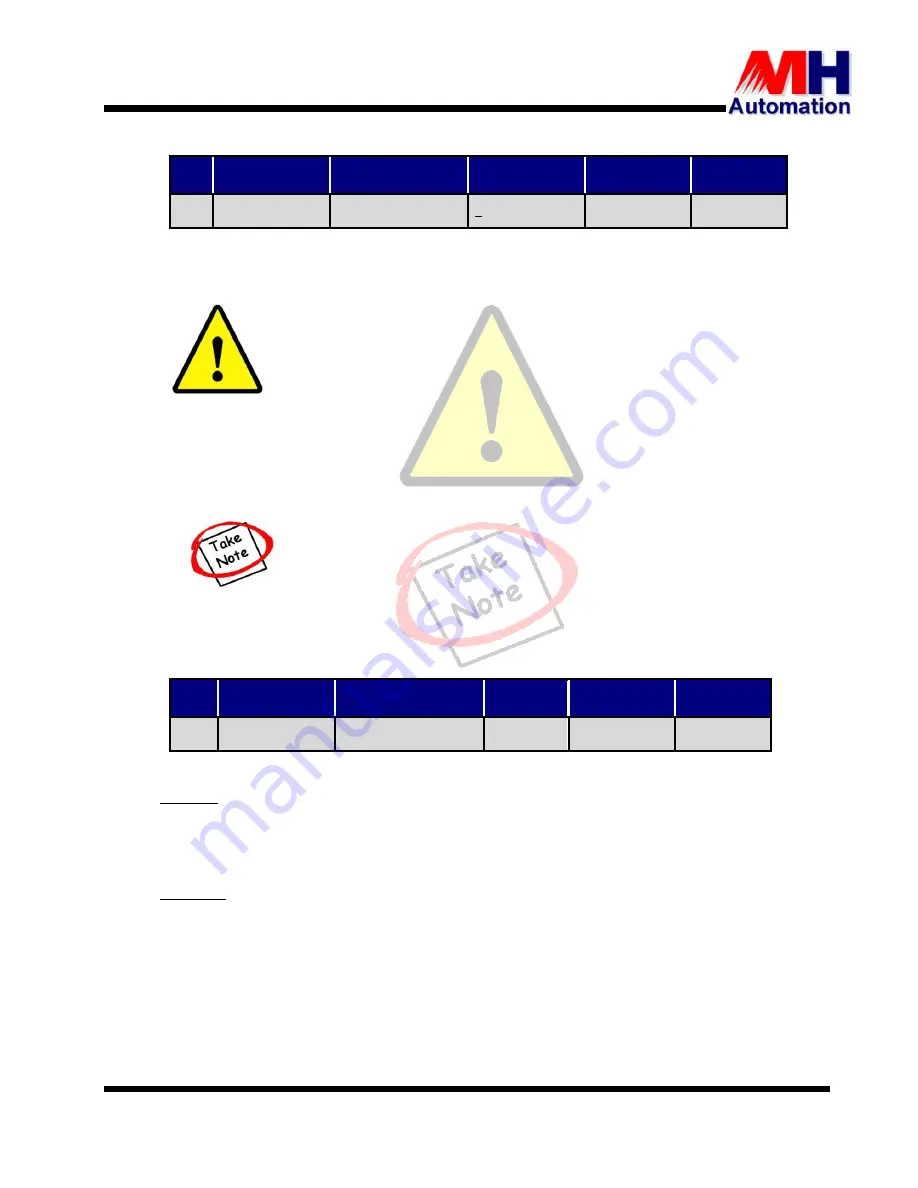
U
U
s
s
e
e
r
r
M
M
a
a
n
n
u
u
a
a
l
l
Revision 8.6
SECTION 3 : TRAVEL PARAMETERS
42
3.4.3.
Motor Current
NO
PARAMETER
DESCRIPTION
SCALE
INCREMENT
DEFAULT
3
Motor Current
Motor full load current
< 60% of CT ratio
-
10
This parameter sets the motor full load stator current (Motor flc).
The value to be used is the stator current related to the mechanical power for the specific duty.
CAUTION
DO NOT EXCEED THE MOTOR NAMEPLATE
VALUE FOR THE APPLICABLE DUTY.
Note
This value should be determined during the
design phase. This value is to be used by the
thermal model to calculate overload conditions
3.4.4.
Overload Class
NO
PARAMETER
DESCRIPTION
SCALE
INCREMENT
DEFAULT
4
Overload class
Overload class type
5 or 10
-
5
This parameter selects the Class of overload that the thermal model uses as a reference.
Class 5:
Example:
Trip if stator current exceeds three times motor full load current (Motor flc) for a period exceeding 17
sec.
Class 10:
Example:
Trip if stator current exceeds three times motor full load current (Motor flc) for a period exceeding 34
sec.