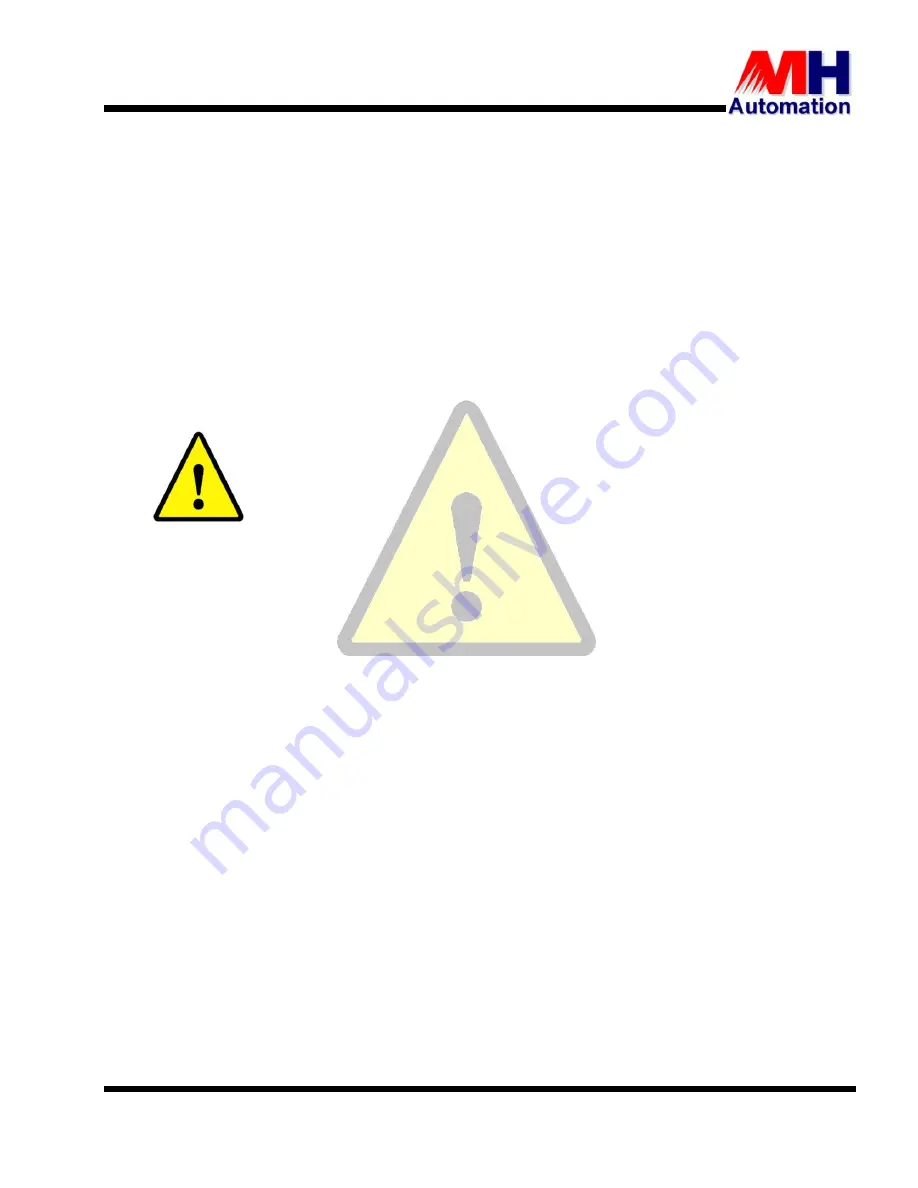
U
U
s
s
e
e
r
r
M
M
a
a
n
n
u
u
a
a
l
l
Revision 8.6
SECTION 2 : SYSTEM DESIGN
15
Before operation can commence, safety circuits monitor the motor for incorrect phase rotation, severe
phase differences or unbalance and low three-phase voltage supply and will only allow operation in the
event that all the conditions are correct. Electrical interlocking is provided to make sure that the master
controller is returned to the zero position after a power or phase loss after which the system will have to
be restarted before operation can commence.
Mechanical stresses to the motor and gearbox are minimised by ramping all the supplied voltages this,
in turn, provides constant acceleration and deceleration.
There are three independent slow speeds in both directions. Selection of full speed causes the motor to
ramp up (accelerate) to full speed. The two acceleration contactors are activated at 50% speed (25 Hz)
and 75% speed (12.5 Hz) respectively and the result is a smooth acceleration up to full speed. The
peak switching current during the acceleration cycle is limited to approximately twice that of the full load
current.
2.5.1.
Control Box
CAUTIONS
1. CARE MUST BE TAKEN WHEN INSERTING
CARDS INTO THE MOTHERBOARD NOT TO
BEND THE CONNECTING PINS
2. DO NOT TOUCH ANY OF THE COMPONENTS
ON THE CIRCUIT BOARDS, THEY ARE
VOLTAGE
SENSITIVE
AND
MAY
BE
DAMAGED / DESTROYED.
The control box contains the control cards necessary for the control of the motion and thyristor firing
circuitry. There are four individual cards that are common to the complete range. The cards are
contained in a box that has an IP51 rating. This keeps out the harmful dust ever present in steelworks
environments. The Control panel secures the cards in their sockets and minimises the effects of
vibration.
Each electronic card is covered with a conformal protective coating. This coating has the following
benefits:
Increased isolation between points at different potentials
Improved mechanical strength of components further resisting vibration
Further protection to card from metallic dust and humidity.
2.5.2.
Control Card
The control card consists of a microprocessor that interfaces with the process input and outputs. The
microprocessor integrates on-chip program memory, data memory (RAM) and serial communication.
Also on the card is the serial EEPROM, keypad and display driver communication interface.
The rotor frequency is evaluated on this card using digital signal processing. This gives the motors
actual speed. Inputs are optically isolated achieving high integrity of the control system.