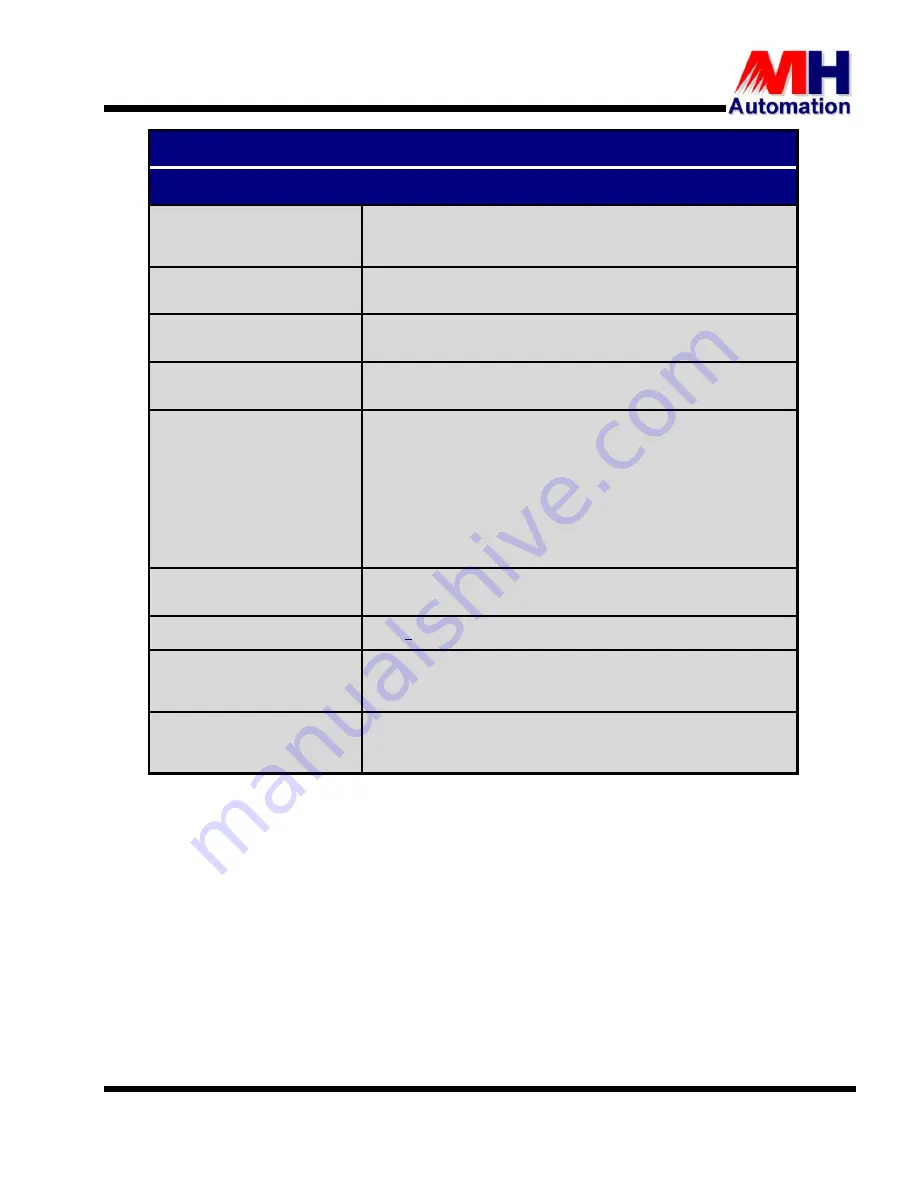
U
U
s
s
e
e
r
r
M
M
a
a
n
n
u
u
a
a
l
l
Revision 8.6
SECTION 2 : SYSTEM DESIGN
18
TECHNICAL DATA
CONTROLLER DATA
Altitude
Max. 1500 m at continuous rated current
Over 1500 m reduce rating by 1% for each 100 m,
absolute maximum altitude 3000 m
Vibration
IEC 721 - 3 - 3
Operating:
Max displacement amplitude 3 mm at 2 - 9 Hz
Max. acceleration amplitude 0,5 G at 9
–200 Hz
Shock
IEC 68 - 2 - 27
Operation: max 8G, 11 ms
Storage and shipping: max 15 G, 11 ms inside the manufacturers package
Enclosure
Control box: IP51
Power stack frames M100 to M2000: IP00
Protective functions
Over current protection: set at 4 x unit rating for a period longer than 2,5
seconds
Input phases rotation
Input phases under voltage: < 0,7 Un
Input phases single phasing
Output phases unbalanced: > 50% unbalance
Unit temperature: stack temperature > 95°C
Motor overload protection: This feature is not yet implemented
Loss of rotor frequency feedback
Loss of torque detection
Control method
Phase angle control; 3 phase, 6 thyristors connected in line with motor stator
in anti-parallel configuration
Operating frequency
50 Hz + 1%
Braking torque
Varies with rotor resistors values used, standard max. 2.5 x Tn.
Units may be designed for greater ratings. Consult MH Automation for further
details
Unit power dissipation
Control box: max. 40 W
Thyristor stack: Approximately 3,8 W/A of motor actual running current at
60% C.D.F
2.7. THYROMAT - BD DIGITAL CRANE CONTROLLER ENCLOSURES
The details listed in this paragraph are based on a complete THYROMAT installation. This includes items
such as the drive, contactors, relays, motor protection unit and other auxiliary components/equipment.
The listed enclosure sizes suggest the minimum requirement and should be used as a guideline only.
The environmental conditions used as a model for the enclosure sizes are based on the following
assumptions:
Ambient temperature
- 40°C
Maximum internal temperature of enclosure
- 60°C
Type of plant
- Ladle handling crane
Location
- Indoors
Degree of protection
- IP54