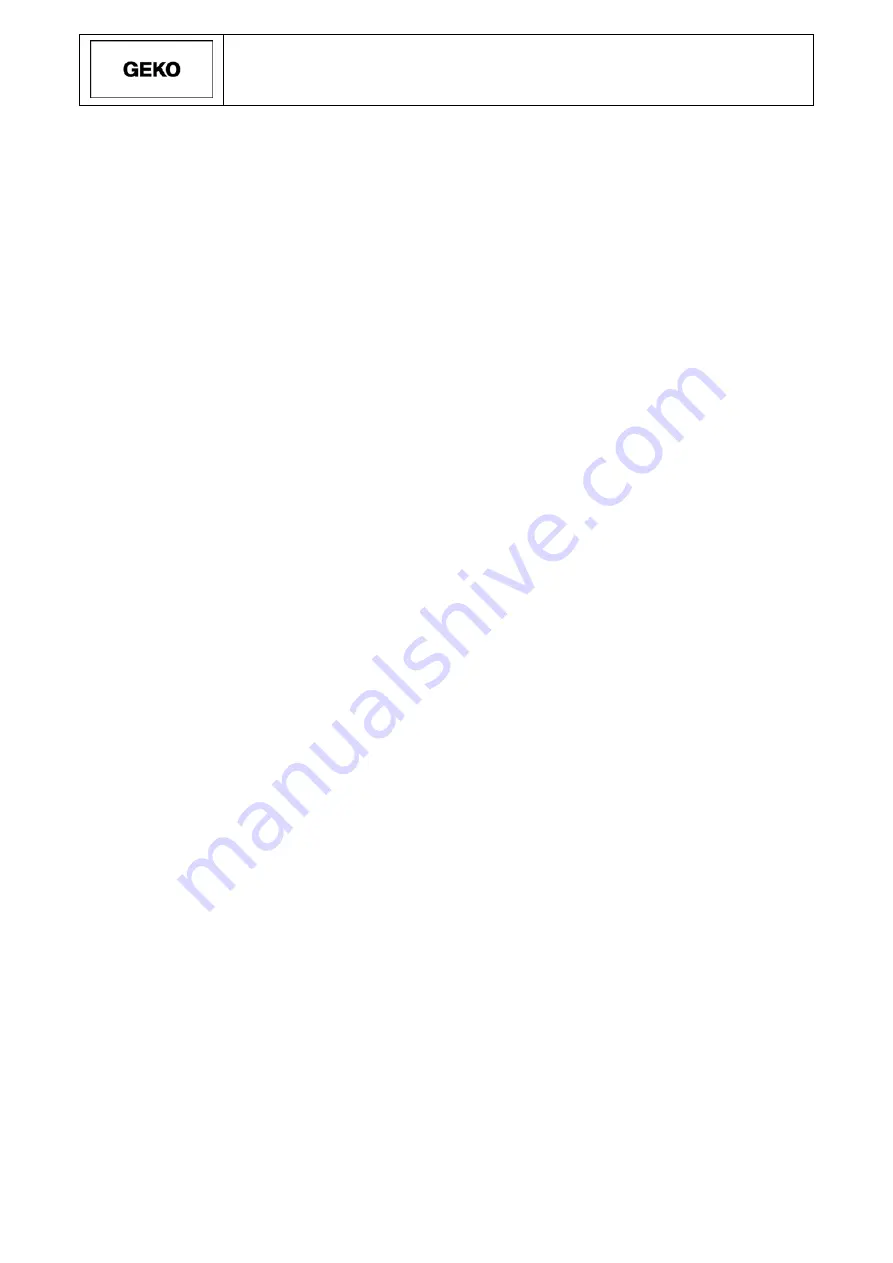
Depiction
22
1.13.3
Continuity / Resistance test
The generator has four components which can be checked using an ohm meter:
exciter stator, exciter rotor, main stator and main rotor. Each of these components
are comprised of various windings which form a complete electrical path of relatively
low resistance. Using an ohm meter measure the loop resistance of each component.
Compare these measured values with the values listed in the specification
section of this manual. Note that very small resistance values require precision
equipment to make accurate measurements; however, a standard ohm meter will
provide a good indication of winding continuity.
1.13.4
Insulation test
Insulation resistance is a measure of the integrity of the insulating materials that
separate the electrical windings from the generator’s steel core. This resistance can
degrade overtime or be degraded by contaminants: dust, dirt, oil, grease, and
especially moisture. Most winding failures are due to a breakdown in the insulation
system. In many cases, low insulation resistance is caused by moisture collected when
the generator is shutdown. Insulation resistance is measured with a megger
(mega-ohmmeter). A megger measures insulation resistance by placing 500 volts
between the winding and the frame of the generator. Caution must be taken to
remove all electronic devices (regulators, diodes, surge protectors, capacitors,
protective relays, etc.) from the winding circuit before checking the insulation.
Winding insulation can be checked on the main stator, main rotor, exciter stator,
and exciter rotor. Minimum resistance is 2 mega-ohms. If the winding resistance
is low it must be dried or repaired.
1.13.5
Diode testing
If the generator is close coupled to an engine, it may be necessary to "bar over" the
engine in order to gain access to a given area of the rectifier assembly. NEVER use the
generator's fan as a fulcrum to accomplish this. Use the engine manufacturer's rec-
ommended practice to manually turn over the engine. To prevent possible injury to
personnel, and damage to the equipment, ensure that the engine cannot start during
this procedure. Remove the two main rotor leads and the three exciter rotor leads
from the rectifier assembly (Figure 5). The rectifier assembly is now electrically iso-
lated from the generator. The diodes remain mounted and the diode leads remain
connected to the terminal posts. Using an ohmmeter or a battery light continuity
tester, place one test probe on the diode lead terminal post. In succession, touch the
other test probe to the lead screw hole in each heat sink. Reverse the probes and re-
peat the procedure. You have now tested the three diodes connected to this terminal
post in both the forward and reverse direction. Repeat the procedure using the other
diode terminal post.
When the positive test probe is connected to the diode's anode and the negative test
probe is connected to the diode's cathode (forward biased), the diode will switch on
and conduct electricity. This is observed by a low resistance reading when using an
ohm meter or the lighting of the bulb when using a battery light continuity tester. Re-
versing the test leads (reverse biased) will result in the diode switching off and no
electricity will be conducted. The results of these tests should indicate one of three
conditions:
Summary of Contents for Eisemann T 18000 E
Page 2: ......
Page 4: ...2...
Page 16: ...Beschreibung 14 1 BESCHREIBUNG 1 1 Abmessungen...
Page 46: ...2...
Page 58: ...Depiction 14 1 DEPICTION 1 1 Dimensions...
Page 88: ...2...
Page 89: ...3...
Page 90: ...4 GEKO EISEMANN...
Page 91: ...GEKO E EISEMAN 5 NN...
Page 94: ...8 0 0 1 0 2...
Page 95: ...9...
Page 96: ...10 0 3 0 4 OFF...
Page 97: ...11 0 5...
Page 98: ...12 0 6 0 6 1...
Page 99: ...13 0 6 2 0 6 3...
Page 100: ...14 0 6 4 0 6 5 0 6 6...
Page 101: ...15 1 1 1 18000 ED S SEBA SS...
Page 104: ...1 5 1 6 400 230 1 7 1 50 Hz 8000 18 18 8 k 2 2...
Page 108: ...1 13 1 13 1 1 13 2 1 2 12 3 1 13 3 1 13 4 2 F F F1 F F 22 12 2 50 00 12...
Page 109: ...1 13 5 1 2 6 30 10 23 3 3 3...
Page 110: ...2 2 1 2 1 1 2 1 2 16 3 24 1 1 8...
Page 111: ...2 2 B A C 25 1 0 1 0 1 0...
Page 112: ...2 3 10 5 1 3 26 5 1 3 200 3 1 2 4 2 3 6...
Page 113: ...2 4 2 4 1 2 4 2 27 5 16 6 16 9 MIN MIN MAX...
Page 115: ...29 2 4 6 DIN VDE 0100 551 DIN VDE 0100 410 17 4 BGV A3 TN C S...
Page 117: ...3 5 3 6 1 7 31 3 3 3...
Page 118: ...2 4 32 1 7 2 7...
Page 119: ...33 4 500...
Page 120: ...34 5 400 250 100 5 5 1 8 2 4 100 5 3 5 1 5 1 2 5 5 250 400 5 3 5 2 2 5 4 5 2...
Page 121: ...5 1 5 1 1 35 16 6 B A 2 80 0 C B...
Page 122: ...5 1 2 5 1 3 16 1 116 11 M 1 2 3 2 4 MAX MIN 36 1 2 3 4 N 1 16 9 1 8 16 9 5...
Page 123: ...5 2 5 2 1 C 5 2 2 1 2 37 C A 16 4 B D...
Page 124: ...5 2 3 5 3 38 Briggs B H 30 s Stratto Briggs St F H 0 on tratton 2 G J K L...
Page 125: ...5 4 F E 39 B...
Page 126: ...40 5 5 A B 0 76 20...
Page 127: ...41 6 6 1 6 1 1 6 1 2 6 1 3 6 1 4...
Page 128: ...42 6 2...
Page 129: ...43 6 3 240 40 C...
Page 130: ......
Page 131: ......
Page 132: ......