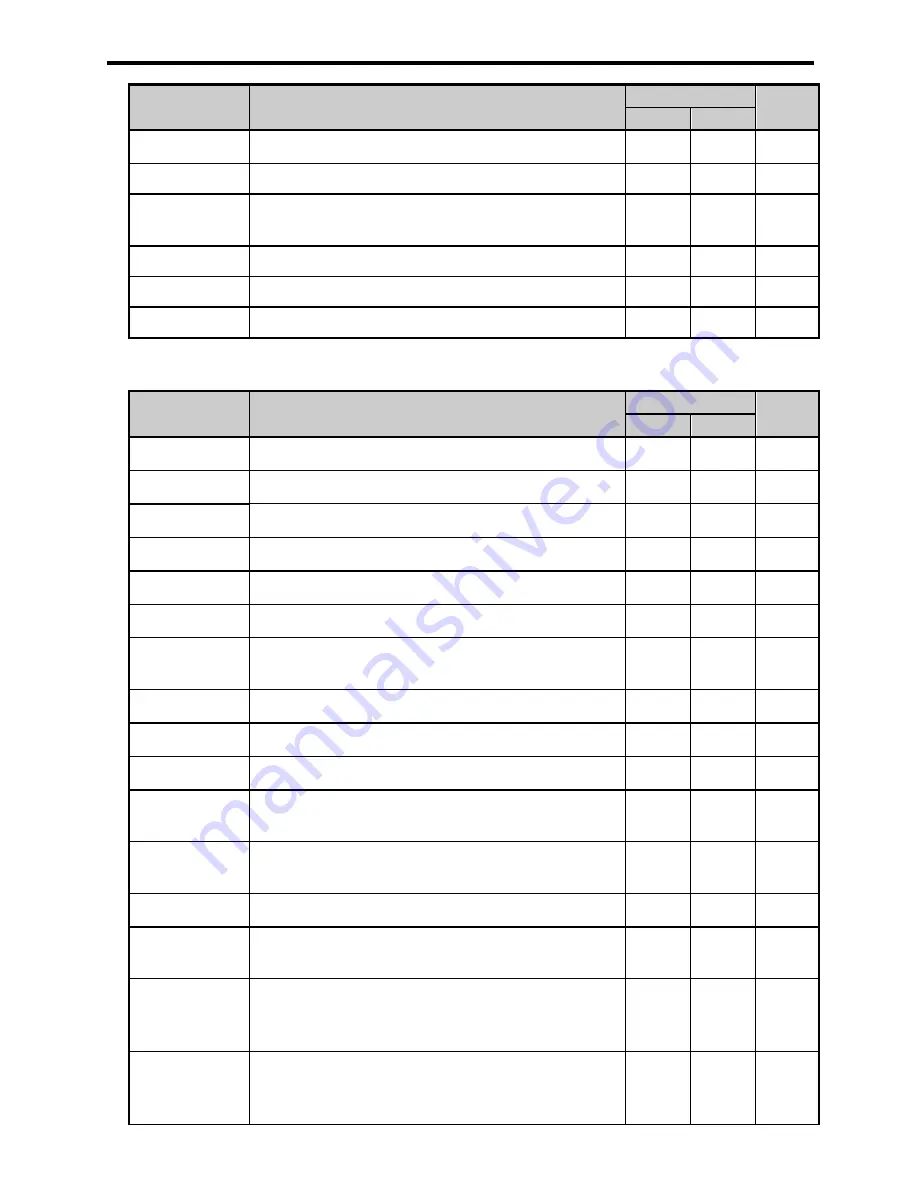
Chapter 6 Positioning Monitoring Package
6-6
Item
Displays
Related flag
Remark
Axis X
Axis Y
Home return
Whether home return is being conducted
K4215
K4315
BIT
Position Sync
Whether position synchronization is being conducted
K4216
K4316
BIT
Speed
Sync Whether position synchronous operation is being
conducted
K4217 K4317
BIT
Jog high speed Whether jog high speed operation is being conducted
K4219
K4319
BIT
Jog low speed
Whether jog low speed operation is being conducted
K4218
K4318
BIT
Inching
Whether inching operation is being conducted
K421A
K431A
BIT
(b) In case of XEC
Item
Displays
Related flag
Remark
Axis X
Axis Y
Current position Current position of each axis
%KD211 %KD216
DINT
Current speed
Current speed of each axis
%KD212 %KD217
DINT
Step No.
Currently operating step of each axis
%KW426 %KW436
WORD
Error code
Error code in case of an error of the axis
%KW427 %KW437
WORD
M code
M code of the currently operating step
%KW428 %KW438
WORD
Busy
Whether the axis is operating
%KX6720 %KX6880
BIT
Positioning
complete
Whether the positioning has been completed for the axis
%KX6722 %KX6882
BIT
M code On
M code On/Off of the currently operating step
%KX6723 %KX6883
BIT
Origin fix
Whether the origin has been fixed
%KX6724 %KX6884
BIT
Output inhibit
Whether output is inhibited
%KX6725 %KX6885
BIT
Upper limit
detection
Whether the upper limit is detected
%KX6728 %KX6888
BIT
Lower limit
detection
Whether the lower limit is detected
%KX6729 %KX6889
BIT
EMG stop
Emergency stop
%KX6730 %KX6890
BIT
Normal/reverse
rotation
Normal and reverse rotation
%KX6731 %KX6891
BIT
Operation status
The operation status of each axis (acc., dec., constant
speed, and dwell)
%KX6732
~
%KX6735
%KX6892
~
%KX6895
BIT
Control pattern
Operation control pattern of each axis (position, speed,
interpolation)
%KX6736
~
%KX6738
%KX6896
~
%KX6898
BIT
Summary of Contents for XBC-DN20S
Page 210: ...Chapter 7 Program Examples of Positioning 7 6 2 XEC ...
Page 215: ...Chapter 7 Program Examples of Positioning 7 11 2 XEC ...
Page 220: ...Chapter 7 Program Examples of Positioning 7 16 2 XEC ...
Page 225: ...Chapter 7 Program Examples of Positioning 7 21 2 XEC ...
Page 232: ...Chapter 7 Program Examples of Positioning 7 28 2 XEC ...
Page 237: ...Chapter 7 Program Examples of Positioning 7 33 2 XEC ...
Page 240: ...Chapter 7 Program Examples of Positioning 7 36 ...
Page 309: ...Appendix 4 Dimension App 4 4 XBC DN64H XEC DN64H XEC DP64H XBC DR64H XEC DR64H ...
Page 311: ...Appendix 4 Dimension App 4 6 XBE DC08A XBE DC16A XBE TN08A XBE TN16A XBE DR16A XBE RY08A ...
Page 312: ...Appendix 4 Dimension App 4 7 5 Communication module XBL C41 21A XBL EMTA ...
Page 313: ...Appendix 4 Dimension App 4 8 5 Special module XBF AD04A XBF DV04A ...