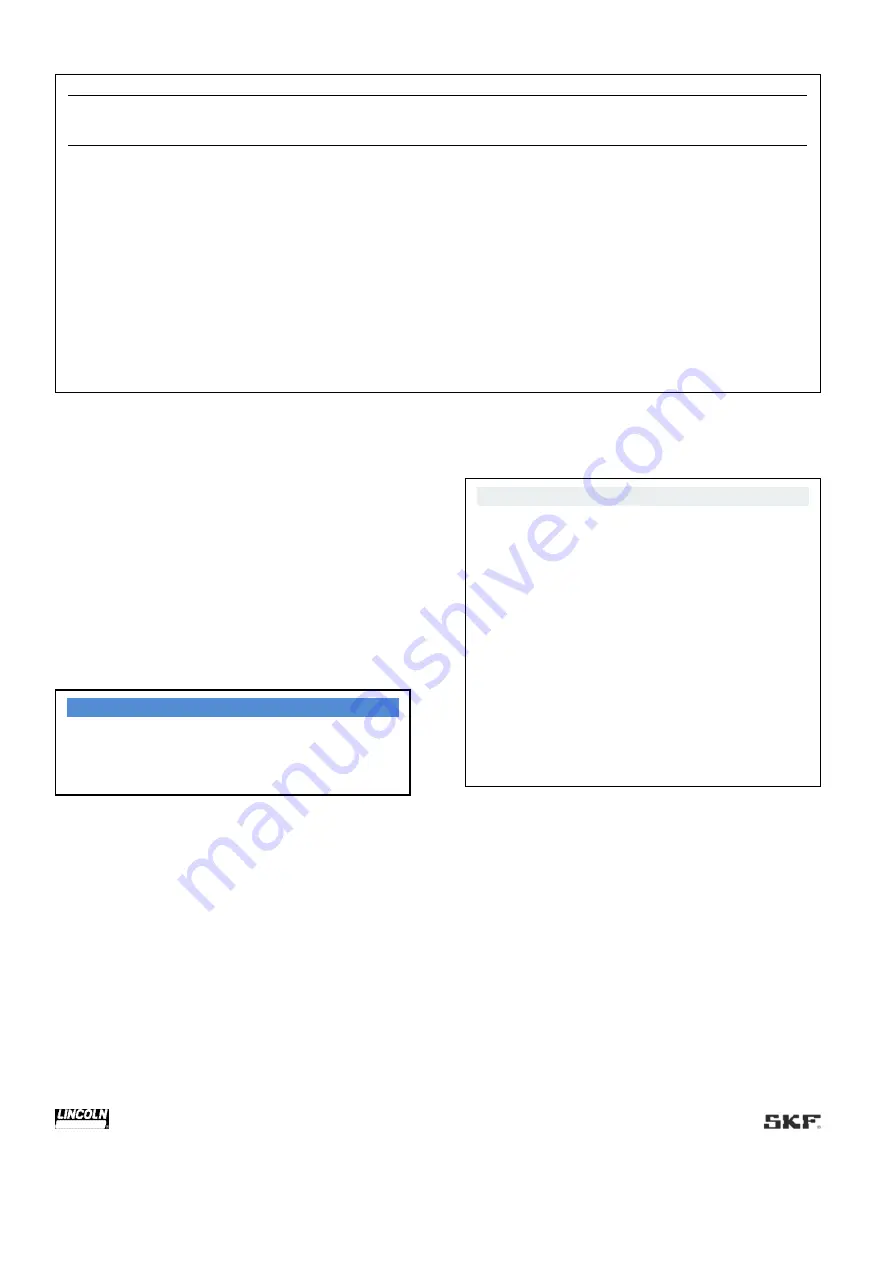
14
Table 2
Residual hazards when operating in a potentially
explosive atmosphere
Avoidance / Remedy
Generation of electrostatic charges, sparks by dropping of
parts
•
Secure parts against falling
•
If necessary, cover parts to avoid sparking
Introduction of catalytic, unstable, or pyrophoric
substances into the potentially explosive atmosphere
•
Ensure that none of these substances enters the potentially explosive
atmosphere
•
Have all substances approved by the operator in advance
Use of isolating amplifiers, for example to operate a
capacity sensor in the potentially explosive atmosphere
•
Install isolating amplifiers only outside of the potentially explosive
atmosphere
Incorrect mounting position. Loss of proper fill level
reporting function
•
Follow the prescribed mounting position (tolerance range ± 5°) / correct
the mounting position as necessary
Use of an unsuitable lubricant at low temperatures. At low
temperatures, excessive lubricant viscosity can cause loss
of flow limiter function
•
Use only lubricants suitable for the specific operating temperature in
each case
2. Lubricants
2.1 General information
Lubricants are used specially for specific applications. To fulfill
the task, lubricants must meet various requirements to varying
degrees. The most important requirements for lubricants are:
•
Reduction in friction and wear
•
Corrosion protection
•
Noise reduction
•
Protection against contamination / ingress of foreign matter
•
Cooling (primarily for oils)
•
Durability (physical/chemical stability)
•
Compatibility with as many materials as possible
•
Economic and environmental aspects
<
IMPORTANT NOTE
Safe operation of the flow limiters is ensured only
when clean lubricating oil is being supplied. The
lubricating oil must be free of air inclusions during
its conveyance.
2.2 Selection of lubricants
SKF Lubrication Systems considers lubricants to be an element
of system design. The selection of a suitable lubricant should
reasonably be made during the design of the machine and
forms the basis for planning the centralized lubrication system.
The manufacturer/operator of the machine should preferably
make the selection with the supplier of the lubricant on the
basis of the requirements profile of the specific task.
If you have no or little experience selecting lubricants for
centralized lubrication systems, please contact SKF.
We gladly assist our customers in the selection of suitable
components for supplying the selected lubricant and in the
planning and design of a centralized lubrication system.
This will spare you potentially costly downtime due to damage
to the machine/system and/or damage to the centralized
lubrication system.
NOTE
•
Only lubricants specified for the product may be used (see
"Technical data" chapter). Unsuitable lubricants may lead
to failure of the product.
•
Do not mix lubricants. This can have unpredictable effects
on the usability and thus on the functioning of the
centralized lubrication system.
•
Due to the large number of possible additives, individual
lubricants that meet the required specifications according
to the manufacturer’s data sheet are under some
circumstances not suitable for use in centralized
lubrication systems (e.g., incompatibility between
synthetic lubricants and materials). To avoid this, always
use lubricants that have been tested by SKF.
•
Observe the relevant safety data sheets and any
instructions regarding hazards marked on the packaging
when handling lubricants.
2.3 Material compatibility
The lubricants must generally be compatible with the following
materials:
•
Steel, gray cast iron, brass, copper, aluminum
•
NBR, FPM, ABS, PA, PU
2.4 Temperature properties
The lubricant used must be suitable for the specific operating
temperature of the product.
The viscosity required for proper functioning of the product
must be maintained and must not be exceeded at low
temperatures or fall too low at low temperatures. See the
"Technical data" chapter for the required viscosities.