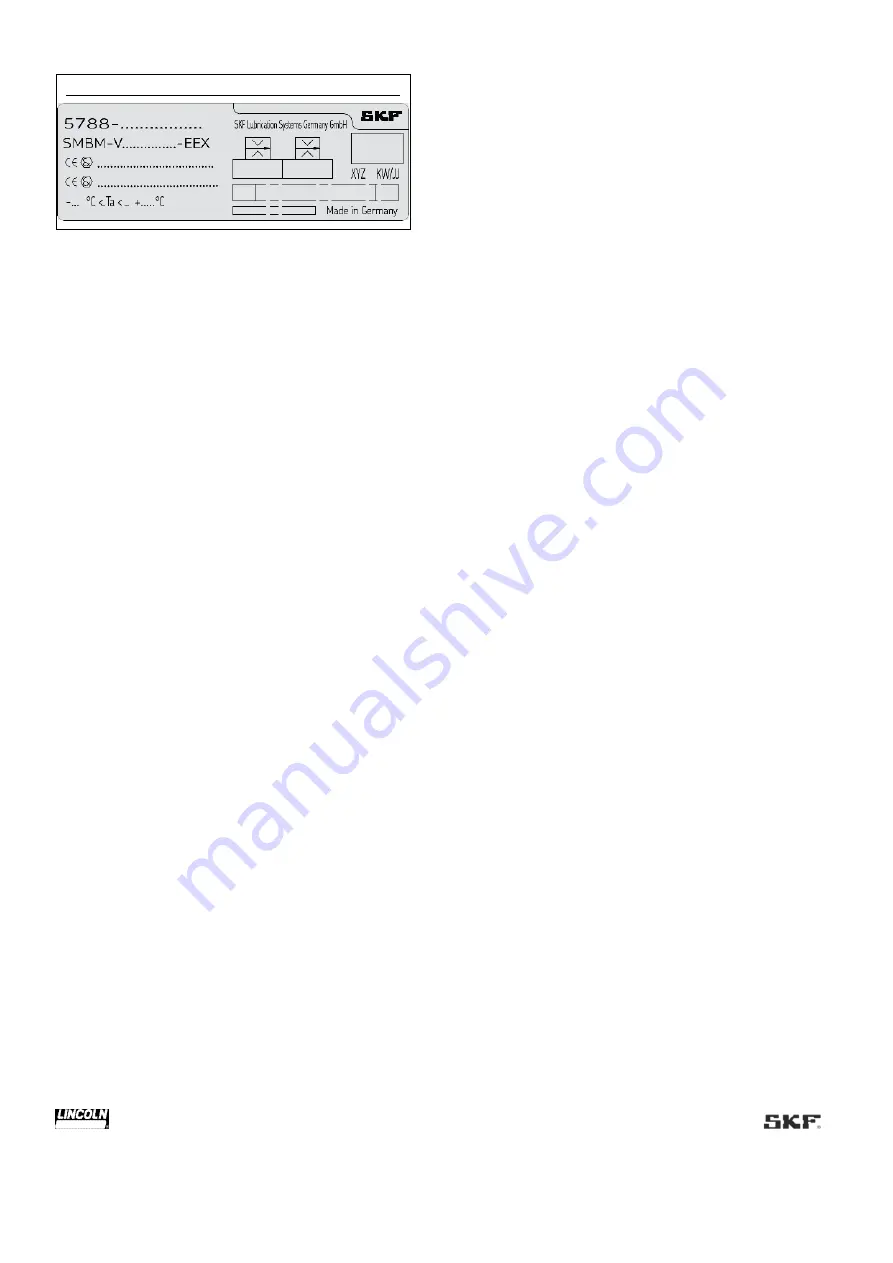
10
Fig. 2
Type plate of the SMBM-V
1.11 Notes on CE marking
CE marking is carried out in accordance with the requirements
of the applied Directives requiring CE marking:
•
2014/30/EC Electromagnetic Compatibility
•
2011/65/EU Directive on the restriction of the use of certain
hazardous substances in electrical and electronic equipment
(RoHS II)
•
2014/34/EU Directive for equipment and protective systems
intended for use in potentially explosive atmospheres (ATEX)
1.12 Note on Low Voltage Directive
The protection objectives of the Low Voltage Directive
2014/35/EU are met in accordance with Annex II, No. 1.2.7 of
the ATEX Directive 2014/34/EU.
1.13 Note on Pressure Equipment
Directive
Due to its performance characteristics, the product does not
reach the limit values defined in Article 4, Paragraph 1,
Subparagraph (a) (ii) and is excluded from the scope of Pressure
Equipment Directive 2014/68/EU in accordance with Article 1,
Paragraph 2 Subparagraph (f).
1.14 Emergency shutdown
This is done by a course of action to be defined by the operator.
1.15 Assembly, maintenance, fault,
repair
Prior to the start of this work, all relevant persons must be
notified of it. At a minimum, the following safety measures must
be taken before any work is done:
•
Unauthorized persons must be kept away
•
Mark and secure the work area
•
Cover adjacent live parts
•
Dry any wet, slippery surfaces or cover them appropriately
•
Cover hot or cold surfaces appropriately
Where applicable:
•
Depressurize
•
Isolate, lock and tag out
•
Check to ensure live voltage is no longer present
•
Ground and short-circuit
The product should be protected as much as possible from
humidity, dust, and vibration, and should be installed so that it
is easily accessible. Ensure an adequate distance from sources
of heat or cold. Any visual monitoring devices present, such as
pressure gauges, min./max. markings, or oil level gauges must
be clearly visible. Observe the mounting position requirements.
Drill required holes only on non-critical, non-load-bearing
parts of the operator's infrastructure. Use existing holes where
possible. Avoid chafe points. Immobilize any moving or detached
parts during the work. Adhere to the specified torques.
If guards or safety devices need to be removed, they must be
reinstalled immediately following conclusion of work and then
checked for proper function.
Check new parts for compliance with the intended use before
using them.
Avoid mixing up or incorrectly assembling disassembled parts.
Label parts. Clean any dirty parts.
1.16 First start-up, daily start-up
Ensure that:
•
All safety devices are fully present and functional
•
All connections are properly connected
•
All parts are correctly installed
•
All warning labels on the product are fully present, visible, and
undamaged
•
Illegible or missing warning labels are immediately replaced
1.17 Special safety instructions regarding
explosion protection
•
Always behave so that explosion hazards are avoided.
•
A written work approval from the operator is required prior to
working in potentially explosive areas. Keep unauthorized
persons away.
•
There must be no indications that parts of the explosion
protection are missing or are not working. Should such
indications become apparent, switch off the machine and
inform a superior without delay.
•
Measures for explosion protection must never be deactivated,
modified or bypassed.
•
It is forbidden to bring in ignition sources such as sparks,
open flames and hot surfaces in potentially explosive areas.
•
Check the machine at regular intervals for damage which may
represent an ignition risk.
•
The ignition temperature of the lubricant must lie at least
50 K over the maximum admissible surface temperature of
the components.
•
Only use tools and clothing which are permitted for use in
potentially explosive areas (ESD).
•
Transport, installation, repairs and work on electrical
components may only be carried out, if it has been ensured
that the atmosphere is not potentially explosive.
•
Repairs or modifications to machines which are protected
against explosions may be carried out only by the
manufacturer or by a workshop recognized by a named
institution and confirmed in writing. If the work is not carried
out by the manufacturer, the repairs must be approved by a