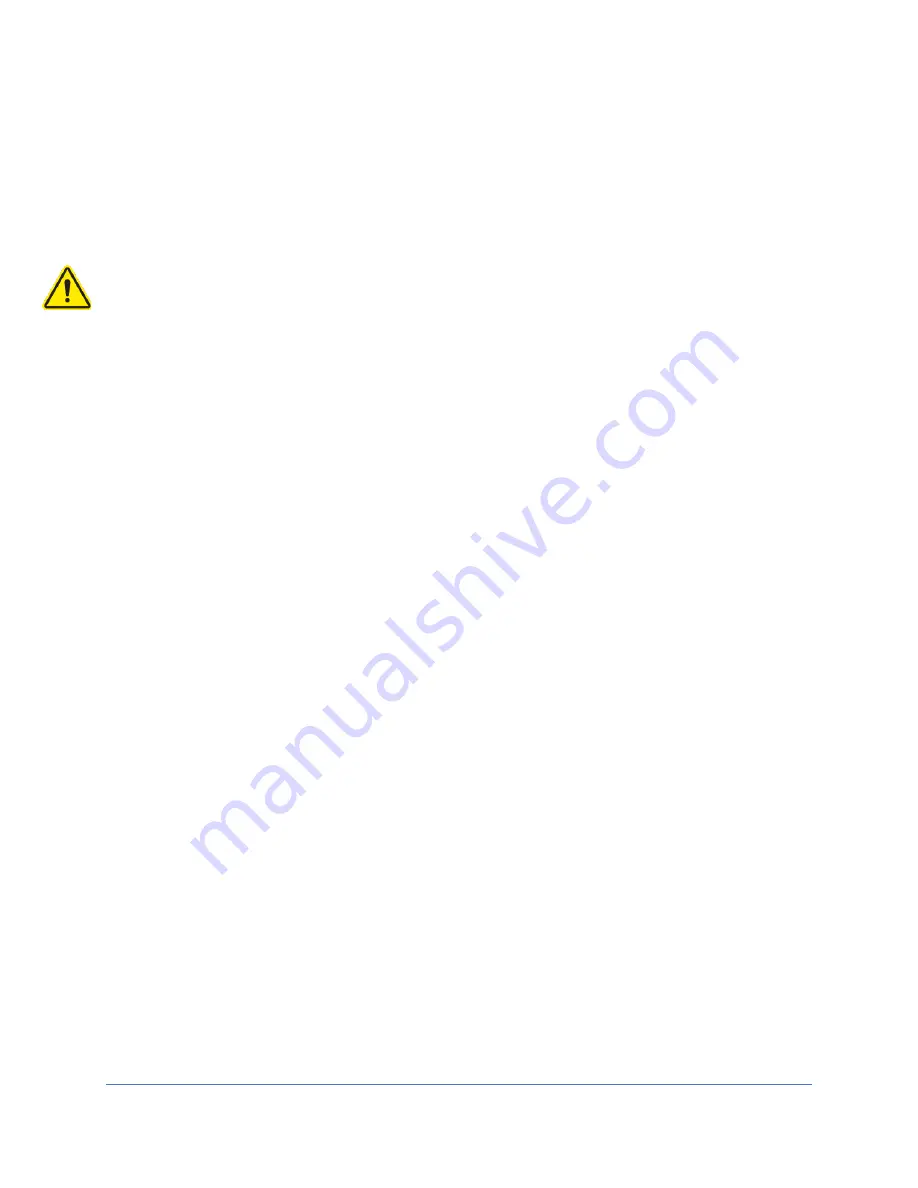
78
Humidify Valve
Humidifier Valve will open (moderate click sound upon actuation), and then close after
30 seconds.
Chamber Light
Chamber Light dims, and then returns to full brightness after 30 seconds.
Time On for each diagnostic test is with Main Door closed. To run each test indefinitely,
open the Main Door before starting the test. Take care not to leave the unit running any
diagnostic tests indefinitely, and do
NOT
run any diagnostic test longer than 30 minutes.
Summary of Contents for Capture BT 31700-00
Page 2: ...2 CAptureTM BT Fuming Chamber 2020 Present 3170000 3170001 3170002 3170003 3170004 3170005...
Page 55: ...55 Figure 7 6...
Page 81: ...81 Wiring Diagrams 100 120V...
Page 82: ...82 208 230V...
Page 87: ...87 Chamber will not achieve humidity...
Page 88: ...88 Chamber does not exhaust CA fumes...
Page 89: ...89 Door alarm active when door s closed...
Page 90: ...90 Hot Plate will not achieve temperature set point...
Page 91: ...91 White CA residue builds on inside of Chamber...