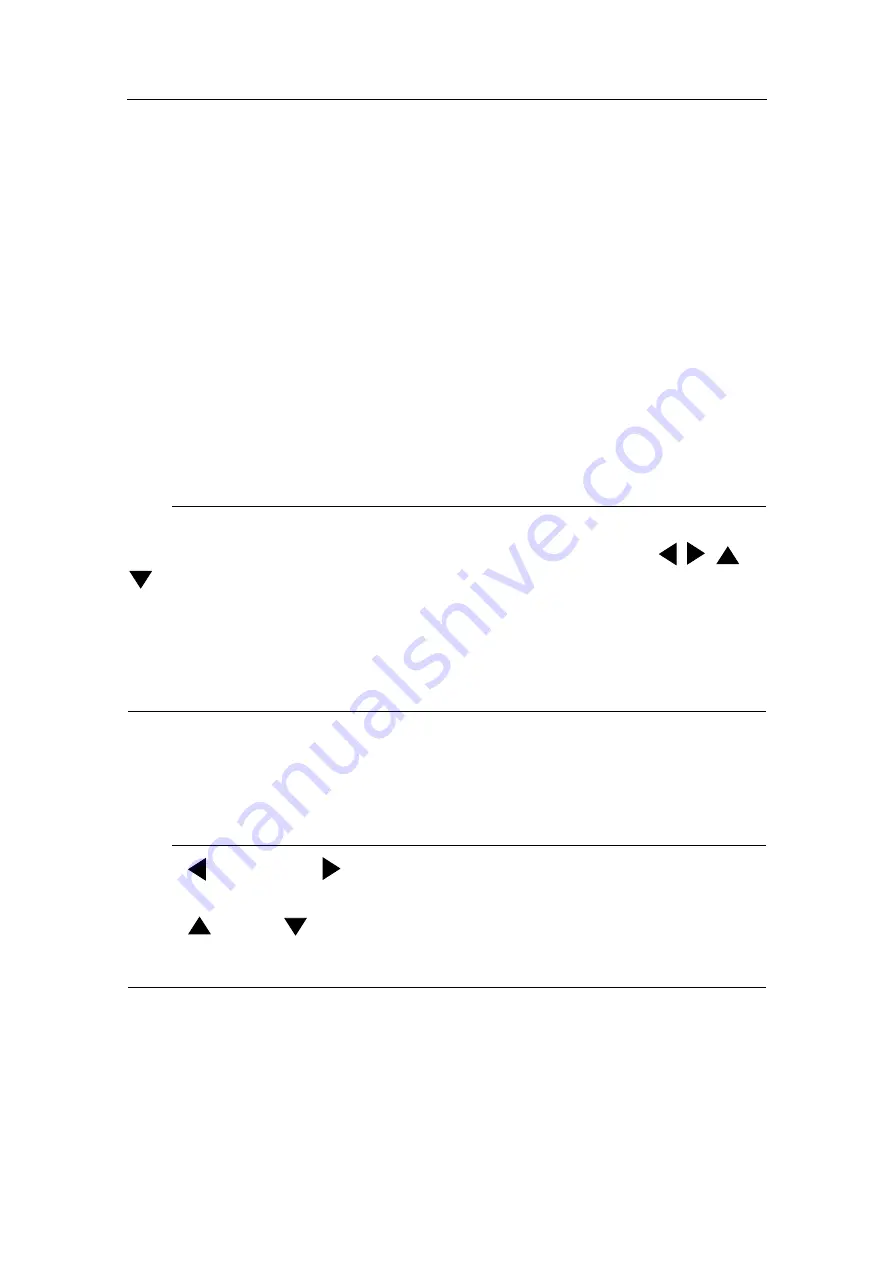
Kongsberg cJoy OT
4
To terminate the panel test, press the
Test
button.
• The panel test function is terminated.
• The
operation
indicator changes to steadily lit green.
Panel dimming
The operator terminal stores two palettes for the display, one for day operation and the
other for night operation. Both of these palettes contain parameters which adjust the
brightness of the display, the brightness of the button status indicators and the intensity
of the button background lighting.
The parameter values for these palettes are changed by means of the Panel dimming
function.
Note
System operation is blocked when the panel dimming function is enabled. If a button not
used by the panel dimming function is pressed (i.e. all buttons except for
,
,
,
and
Enter
) when the function is enabled, the function is automatically terminated.
The panel dimming is also automatically terminated if no buttons are pressed within
a preset time limit.
Toggling between day and night settings is performed by means of the
Day/night
button
(see Day and night palettes on page 77).
When an operator terminal is restarted, the settings for night operation are automatically
selected.
To perform panel dimming for the currently selected (day or night) palette, proceed as
follows:
Note
Use the
(decrease) and
(increase) buttons to adjust level values. Any adjustments
made with these two buttons takes effect immediately.
Use the
(up) and
(down) buttons to navigate from one setting to another.
Use the
Enter
button to navigate down to the next setting.
1
Press the
Dim
button.
• The panel dimming function is enabled.
• The
operation
indicator starts flashing green/red.
• The Dim Settings input dialog, with the
Display Brightness
bargraph selected
(green level indicator), is shown in the View area of the display.
74
385585/C
Summary of Contents for cJoy OT
Page 207: ...Message explanations A 86 385585 C...
Page 208: ...2015 Kongsberg Maritime...