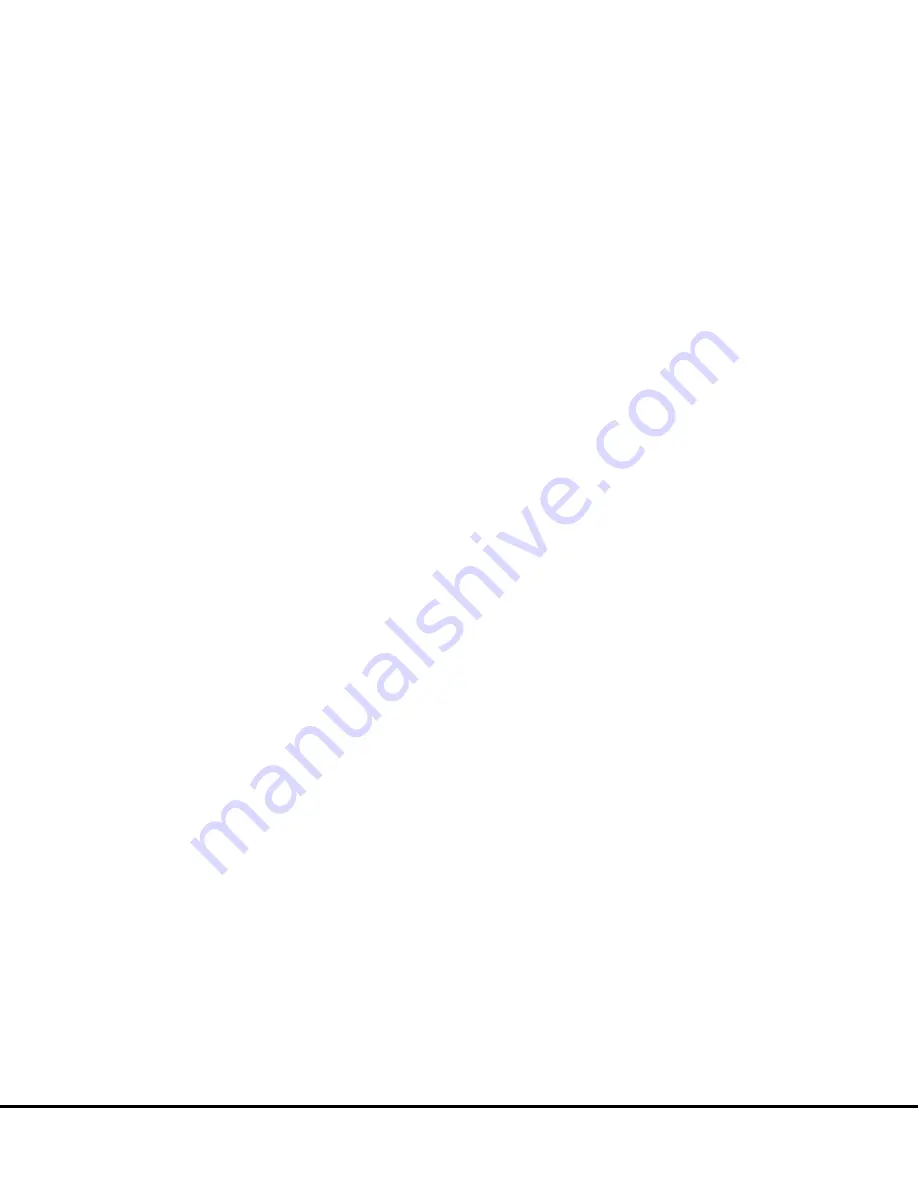
Periodic Inspections
It is important that periodic inspections (every three
months) of stored equipment be performed to insure
the continued serviceability of all protective measures
initially taken when the storage period began. Items
which should be checked at each inspection interval
are listed as follows:
1. Remove the weatherproof tape from the compart-
ment doors and preform a Megger test as de-
scribed in the Vehicle Test Instructions. Record
the test results and compare them with the re-
corded Megger readings taken when storage first
began, and those taken throughout the storage
period. Remove all test equipment and close up
the compartment. Reseal the compartment doors
with new weatherproof tape. If Megger readings
indicate a deterioration of insulation quality, to
below 2.0 megohms then consideration should be
given to providing more protection.
2. Check all other weatherproofing tape. Replace any
that has become loose or is missing completely.
3. Check all heat sources. Replace or repair any units
which have become inoperative.
4. Check all machine surfaces which were coated
with flushing compound when storage began. If
compound appears to be deteriorating, it must be
cleaned off and renewed.
Placing Equipment Into Service After
Storage
When taking equipment out of storage, perform the
following procedures:
When A Truck Is Operational
If a truck has been operated weekly throughout the
storage period, perform a complete visual inspection
of the Motorized Wheels, blowers, alternator and con-
trol compartments. Repair any defects found, then
place the truck directly into service.
When A Truck Is Not Operational
If the truck was not operated weekly throughout the
storage period, perform the following procedures:
1. Remove all weatherproofing tape from control
compartment doors and ductworks.
2. Remove all screening material from ductwork.
3. Remove all heat sources from Motorized Wheels,
control compartments and the alternator.
4. Fill with recommended oil. Refer to the Motorized
Wheel Service Manual for the type and amount oil
to be used. This oil should be drained and new oil
should be added after 500 hours of operation.
5. Clean all Motorized Wheel grease fittings in the
axle box. Insure that all grease lines are com-
pletely full of grease. Then add the recommended
amount of grease to all fittings.
6. Install brushes in the Motorized Wheels, blowers
and the alternator. Make sure that brushes move
freely in their carbonways and that they have
enough length to serve until the truck’s next in-
spection period. Install new brushes if necessary.
Insure that all brush pigtail screws are tight.
7. Perform a megohmmeter test. Refer to the truck’s
Vehicle Test Instructions for the correct proce-
dure. If Megger readings are less than 2.0 me-
gohms, the problem could be an accumulation of
moisture in motor or alternator. If this is the case,
the faulty component will have to be isolated and
dried out using procedures recommended in the
G.E.Service Manual.
8. Perform a thorough inspection of the Motorized
Wheels, alternator, blowers and control compart-
ments. Look for:
a. Rust or dirt accumulation on machine surfaces
b. Damaged insulation
c. An accumulation of moisture or debris
d. Loose wiring and cables
e. Any rust on electrical connectors in the control
compartment
f. Any loose cards in the card panels
g. Any accumulation of moisture or debris in duct-
work.
Clean and make repairs as necessary.
9. Check retarding grids and insulators for loose
connections and dirt accumulation. Clean and
make corrections as necessary.
10. Where applicable, check exciter drive belts for
cracks, and deterioration. If acceptable, set belt
tension to specification.
11. Before starting engine, turn on control power.
Check that contactors and relays pick up and drop
out normally.
12. Perform a start-up procedure on the complete
system to insure maximum performance during
service. Refer to the truck’s Vehicle Test Instruc-
tions for the complete test procedure.
A07003
Storage Procedures
A7-15
Summary of Contents for 930E-2
Page 1: ......
Page 2: ......
Page 4: ...NOTES ...
Page 8: ...KOMATSU MODEL 930E Dump Truck A 4 Introduction A00017 03 01 ...
Page 10: ...NOTES A1 2 Index A01001 2 94 ...
Page 12: ...930E MAJOR COMPONENTS A2 2 Major Component Description A02055 ...
Page 35: ...START HERE Walk Around Inspection A03017 General Safety and Operating Instructions A3 21 ...
Page 46: ...NOTES A3 32 General Safety and Operating Instructions A03017 ...
Page 78: ...NOTES B1 2 Index B01016 ...
Page 88: ...NOTES B3 6 Dump Body B03013 03 01 ...
Page 92: ...NOTES B4 4 Fuel Tank B04015 ...
Page 94: ...NOTES C1 2 Index C01021 03 01 ...
Page 118: ...NOTES C5 6 Air Filtration System C05013 5 98 ...
Page 126: ...NOTES D2 6 24VDC Electric Supply System D02018 ...
Page 142: ...NOTES D3 16 24VDC System Components D03019 04 01 ...
Page 146: ...FIGURE 2 1 PROPULSION SYSTEM DIAGRAM E2 2 Electrical Propulsion System Components E02014 3 01 ...
Page 196: ...NOTES E2 52 Electrical Propulsion System Components E02014 3 01 ...
Page 240: ...NOTES E3 44 AC Drive System Electrical Checkout Procedure 3 01 E03015 Release 17 Software ...
Page 242: ...NOTES G1 2 Index G01017 ...
Page 250: ...NOTES G2 8 Tires and Rims G02015 ...
Page 274: ...NOTES H1 2 Index H01013 04 01 ...
Page 282: ...NOTES H2 8 Front Suspensions H02013 2 01 ...
Page 288: ...NOTES H3 6 Rear Suspensions H03013 ...
Page 334: ...NOTES J3 32 Brake Circuit Component Service J03019 1 99 ...
Page 378: ...NOTES L2 8 Hydraulic System L02028 ...
Page 401: ...FIGURE 4 5 FLOW AMPLIFIER VALVE L04031 Steering Circuit L4 7 ...
Page 403: ...FIGURE 4 6 FLOW AMPLIFIER NO STEER L04031 Steering Circuit L4 9 ...
Page 405: ...FIGURE 4 7 FLOW AMPLIFIER LEFT STEER L04031 Steering Circuit L4 11 ...
Page 407: ...FIGURE 4 8 FLOW AMPLIFIER RIGHT STEER L04031 Steering Circuit L4 13 ...
Page 409: ...FIGURE 4 9 FLOW AMPLIFIER NO STEER EXTERNAL SHOCK LOAD L04031 Steering Circuit L4 15 ...
Page 414: ...NOTES L4 20 Steering Circuit L04031 ...
Page 422: ...NOTES L5 8 Steering Control Unit L05021 ...
Page 429: ...L06021 Steering Circuit Component Repair L6 7 ...
Page 450: ...NOTES L6 28 Steering Circuit Component Repair L06021 ...
Page 466: ...NOTES L7 16 Hoist Circuit L07023 ...
Page 492: ...NOTES L9 6 Hydraulic System Filters L09008 ...
Page 504: ...NOTES L10 12 Hydraulic Check out Procedure L10012 ...
Page 508: ...NOTES M1 2 Index M01034 03 01 ...
Page 518: ...NOTES M2 3 10 Ansul Checkfire Electric Detection and Actuation System M02003 ...
Page 524: ...NOTES M5 4 Wiggins Quick Fill Fuel System M05002 10 96 ...
Page 532: ...NOTES M8 8 Special Tools M08012 9 99 ...
Page 560: ...NOTES M9 28 Air Conditioning System M09010 6 97 for HFC 134a Refrigerant ...
Page 618: ...M20 20 Payload Meter II M20007 10 00 ...
Page 619: ...M20007 10 00 Payload Meter II M20 21 ...
Page 627: ...M20007 10 00 Payload Meter II M20 29 ...
Page 634: ...NOTES N1 2 Index N01020 03 01 ...
Page 654: ...NOTES N3 6 Cab Components N03011 7 98 ...
Page 660: ...NOTES N4 6 Operator Comfort N04020 ...
Page 686: ...NOTES N5 26 Operator Cab Controls N05044 ...
Page 688: ...NOTES P1 2 Index P01024 ...
Page 691: ...P02034 Lubrication and Service P2 3 ...
Page 722: ......
Page 723: ......
Page 724: ......
Page 725: ......
Page 726: ......
Page 727: ......
Page 728: ......
Page 729: ......
Page 730: ......
Page 731: ......
Page 732: ......
Page 733: ......
Page 734: ......
Page 735: ......
Page 736: ......
Page 737: ...NOTES R1 2 930E Schematics R01048 with Cummins QSK60 Series Engine ...
Page 738: ......
Page 739: ......