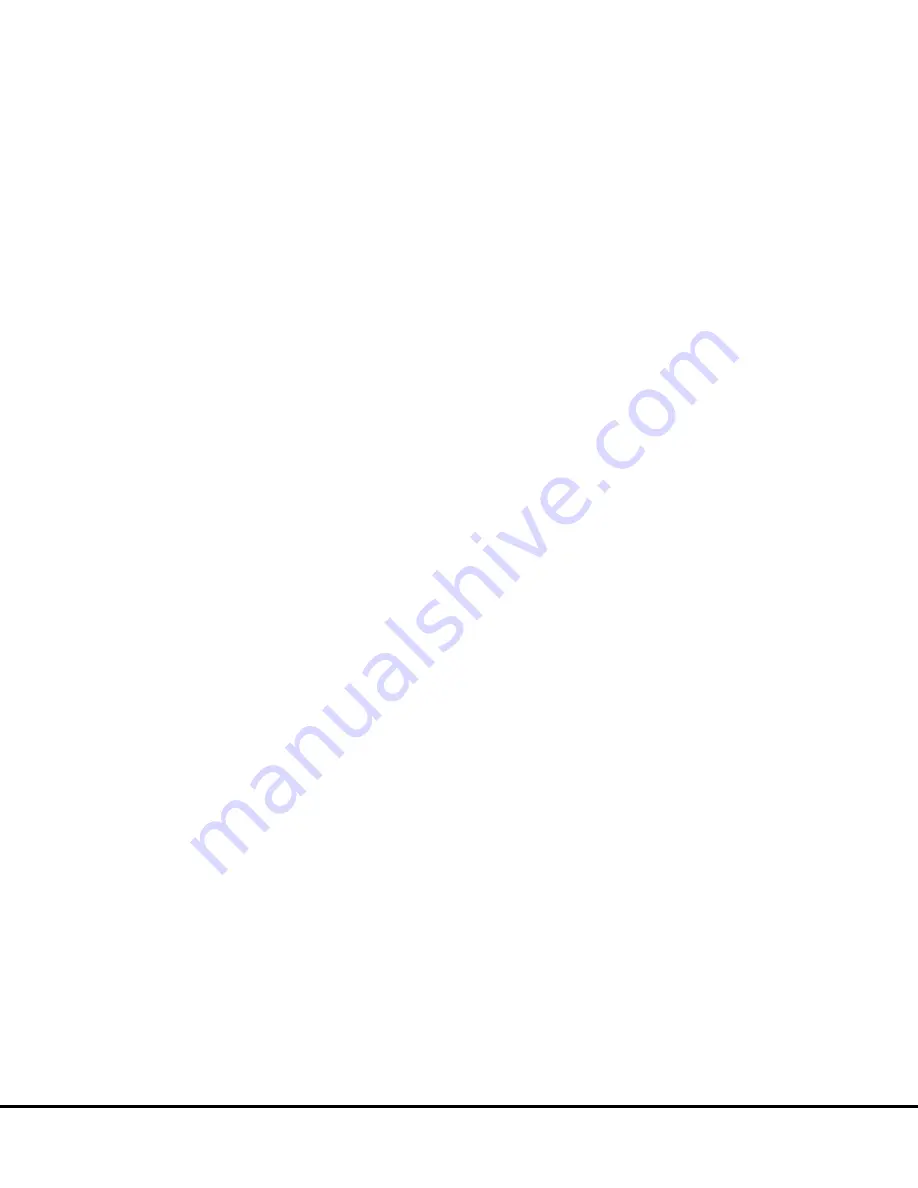
Propel Torque Control
This software function commands the appropriate mo-
tor torque to the inverters during propel. The torque
command is primarily a function of the accel pedal
position and is limited by the physical constraints of the
system.
Each wheel torque is computed independently be-
cause the wheels may be operating at different
speeds. Each torque command is adjusted to account
for the following constraints:
•
Speed Override
The propulsion system will attempt to limit truck
speed to the design envelope of the wheel motors.
As such, the torque command will be modulated as
the truck speed approaches the motor overspeed
limit so that this limit is not exceeded if possible.
Note, however, that steady state operation is kept
as close to the overspeed limit as possible without
exceeding it.
•
Motor Torque Limits
The torque command will be constrained to the
operating envelope of the inverters and the traction
motors. The maximum torque that can be com-
manded is dependent on motor speed and on DC
link voltage.
•
Gear Stress
The torque commanded will not exceed that which
will produce excess gear stress.
•
Horsepower Available
The horsepower available will be estimated from
the engine speed. Parasitic loads are taken into
account. The torque will be limited such that the
engine does not overload.
•
Jerk Limit
The torque command will be slew-rate limited to
prevent jerking motion.
•
Wheel Spin
In the event that the inverters detect a wheel spin
condition and reduce torque in the slipping wheel,
the motor torque in the other wheel may be in-
creased within the above constraints such that as
much of the total desired torque as possible is
maintained.
Retard Torque Control
The retard system converts braking torque from the
wheel motors to energy dissipated in the resistor grid.
The requested retard torque is based on the following
three sources:
•
Retard Foot Pedal or Lever
The maximum short time retard torque (at any
speed, hence the constant torque level) will be
scaled (linearly) by the retard foot pedal input
(RPINHI) to produce the foot pedal retard torque
call.
•
Overspeed
While overspeed is active, the full available retard
torque will be requested.
•
Retard Speed Control
While RSC is active, the RSC retard torque call will
be adjusted to control truck speed to the RSC set
point. Retard speed control will not request any
retard torque if RSC is not active.
The maximum torque call from the above three
sources will be selected as the retard torque call.
Retard Torque Limits are as follows:
1. The retard torque call will be limited to the maxi-
mum torque level based on speed.
2. The retard torque call will be limited to the maxi-
mum torque level available within the thermal
constraints of the motors.
3. The retard torque call will be limited as needed to
prevent overvoltage on the DC link.
4. While in retard, the minimum retard torque call will
provide enough power to support at least one grid
with 600 volts on the DC link. Retard will be
dropped if the torque call falls below this value.
5. At low speed, the available retard torque will be
ramped to zero.
Wheel Slide Control
The inverters prevent wheel slide by limiting torque to
maintain wheel speeds above preset limits. These
preset limits are a function of truck speed and the
allowable creep; additional compensation will be ap-
plied to provide for differences between wheel speeds
during turns.
E02014 3/01
Electrical Propulsion System Components
E2-35
Summary of Contents for 930E-2
Page 1: ......
Page 2: ......
Page 4: ...NOTES ...
Page 8: ...KOMATSU MODEL 930E Dump Truck A 4 Introduction A00017 03 01 ...
Page 10: ...NOTES A1 2 Index A01001 2 94 ...
Page 12: ...930E MAJOR COMPONENTS A2 2 Major Component Description A02055 ...
Page 35: ...START HERE Walk Around Inspection A03017 General Safety and Operating Instructions A3 21 ...
Page 46: ...NOTES A3 32 General Safety and Operating Instructions A03017 ...
Page 78: ...NOTES B1 2 Index B01016 ...
Page 88: ...NOTES B3 6 Dump Body B03013 03 01 ...
Page 92: ...NOTES B4 4 Fuel Tank B04015 ...
Page 94: ...NOTES C1 2 Index C01021 03 01 ...
Page 118: ...NOTES C5 6 Air Filtration System C05013 5 98 ...
Page 126: ...NOTES D2 6 24VDC Electric Supply System D02018 ...
Page 142: ...NOTES D3 16 24VDC System Components D03019 04 01 ...
Page 146: ...FIGURE 2 1 PROPULSION SYSTEM DIAGRAM E2 2 Electrical Propulsion System Components E02014 3 01 ...
Page 196: ...NOTES E2 52 Electrical Propulsion System Components E02014 3 01 ...
Page 240: ...NOTES E3 44 AC Drive System Electrical Checkout Procedure 3 01 E03015 Release 17 Software ...
Page 242: ...NOTES G1 2 Index G01017 ...
Page 250: ...NOTES G2 8 Tires and Rims G02015 ...
Page 274: ...NOTES H1 2 Index H01013 04 01 ...
Page 282: ...NOTES H2 8 Front Suspensions H02013 2 01 ...
Page 288: ...NOTES H3 6 Rear Suspensions H03013 ...
Page 334: ...NOTES J3 32 Brake Circuit Component Service J03019 1 99 ...
Page 378: ...NOTES L2 8 Hydraulic System L02028 ...
Page 401: ...FIGURE 4 5 FLOW AMPLIFIER VALVE L04031 Steering Circuit L4 7 ...
Page 403: ...FIGURE 4 6 FLOW AMPLIFIER NO STEER L04031 Steering Circuit L4 9 ...
Page 405: ...FIGURE 4 7 FLOW AMPLIFIER LEFT STEER L04031 Steering Circuit L4 11 ...
Page 407: ...FIGURE 4 8 FLOW AMPLIFIER RIGHT STEER L04031 Steering Circuit L4 13 ...
Page 409: ...FIGURE 4 9 FLOW AMPLIFIER NO STEER EXTERNAL SHOCK LOAD L04031 Steering Circuit L4 15 ...
Page 414: ...NOTES L4 20 Steering Circuit L04031 ...
Page 422: ...NOTES L5 8 Steering Control Unit L05021 ...
Page 429: ...L06021 Steering Circuit Component Repair L6 7 ...
Page 450: ...NOTES L6 28 Steering Circuit Component Repair L06021 ...
Page 466: ...NOTES L7 16 Hoist Circuit L07023 ...
Page 492: ...NOTES L9 6 Hydraulic System Filters L09008 ...
Page 504: ...NOTES L10 12 Hydraulic Check out Procedure L10012 ...
Page 508: ...NOTES M1 2 Index M01034 03 01 ...
Page 518: ...NOTES M2 3 10 Ansul Checkfire Electric Detection and Actuation System M02003 ...
Page 524: ...NOTES M5 4 Wiggins Quick Fill Fuel System M05002 10 96 ...
Page 532: ...NOTES M8 8 Special Tools M08012 9 99 ...
Page 560: ...NOTES M9 28 Air Conditioning System M09010 6 97 for HFC 134a Refrigerant ...
Page 618: ...M20 20 Payload Meter II M20007 10 00 ...
Page 619: ...M20007 10 00 Payload Meter II M20 21 ...
Page 627: ...M20007 10 00 Payload Meter II M20 29 ...
Page 634: ...NOTES N1 2 Index N01020 03 01 ...
Page 654: ...NOTES N3 6 Cab Components N03011 7 98 ...
Page 660: ...NOTES N4 6 Operator Comfort N04020 ...
Page 686: ...NOTES N5 26 Operator Cab Controls N05044 ...
Page 688: ...NOTES P1 2 Index P01024 ...
Page 691: ...P02034 Lubrication and Service P2 3 ...
Page 722: ......
Page 723: ......
Page 724: ......
Page 725: ......
Page 726: ......
Page 727: ......
Page 728: ......
Page 729: ......
Page 730: ......
Page 731: ......
Page 732: ......
Page 733: ......
Page 734: ......
Page 735: ......
Page 736: ......
Page 737: ...NOTES R1 2 930E Schematics R01048 with Cummins QSK60 Series Engine ...
Page 738: ......
Page 739: ......