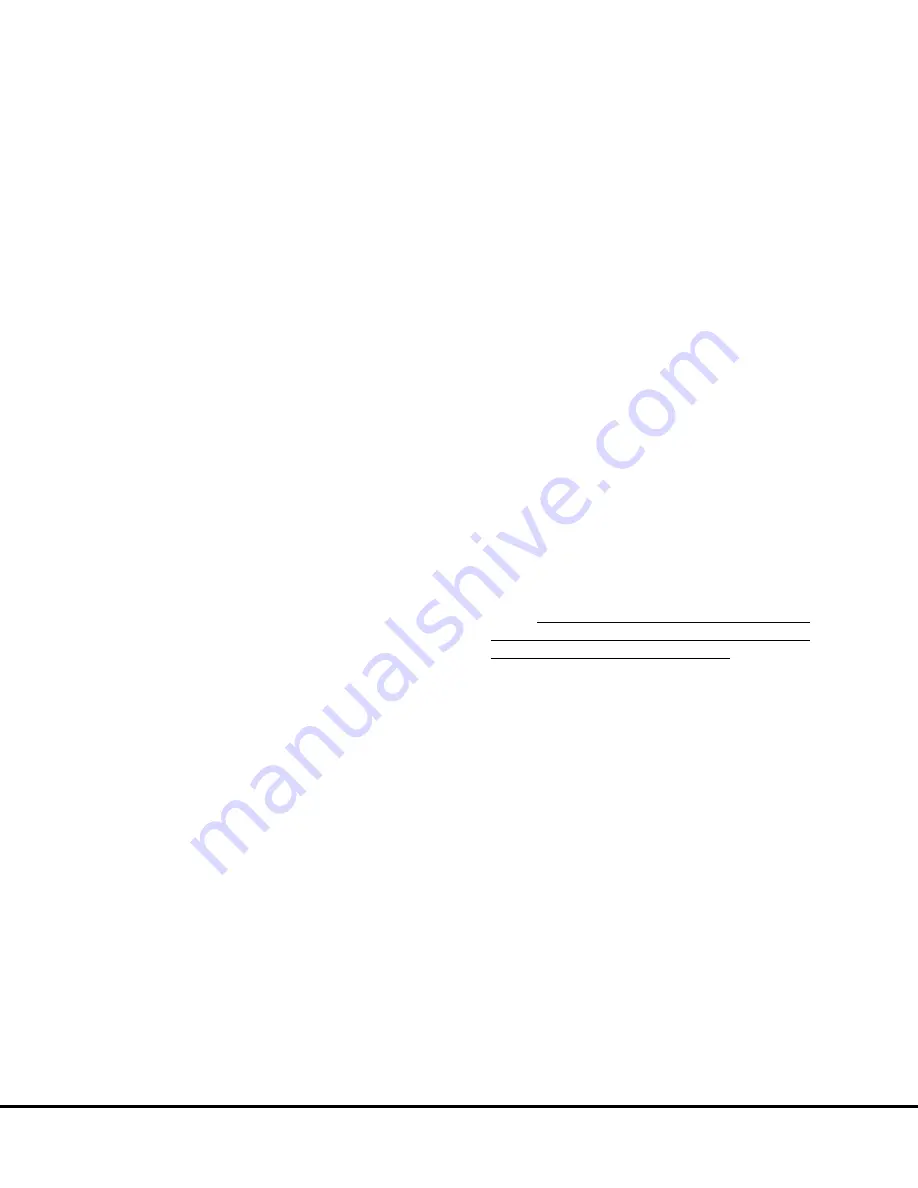
BF4822 STATOR SERVICE TOOL INSTRUCTIONS
Function of Service Tool
This tool has been designed to remove and install
stators in alternators. The user of this tool must be
familiar with basic disassembly and reassembly tech-
niques of dual stator alternators. Proper assembly and
use of this tool will result in correct placement of stators
inside the shell (indexing of stator, with respect to
stator leads). Read through these instructions to
familiarize yourself with the names of various tool
components prior to attempting stator removal or
installation.
STATOR REMOVAL AND REPLACEMENT
Shell Assembly Preparation (Refer to Figure 13-41)
The field coil and shell studs must be removed from
the shell assembly before a stator can be removed.
REMINDER: A narrow, 1 – 3” wide, support ring is in
the tool package (not pictured). This ring is used when
necessary, to provide additional tool height to prevent
the jack screw from protruding through the bottom
thrust plate and preventing proper tool use.
1. Position the bottom thrust plate in work area.
2. Place the first support ring on the bottom thrust
plate.Make sure the support ring seats in the
mating groove in the bottom thrust plate.
3. Place the shell assembly on the support ring with
the stator to be removed, facing up.
4. Place the second support ring on top of the shell
assembly.Reach inside the support ring and po-
sition the stator leads inside and away from the
top of the shell assembly.
Pressure Plate Set-up (Refer to Figure 13-42)
5. Thread the 3/8” diameter guide pin into the pres-
sure plate, from the hub side of the pressure plate.
The threaded hub on the pressure plate faces up,
toward the top thrust plate.
6. Lay the top thrust plate on the pressure plate as
you pass the guide pin through the curved slot in
the top thrust plate.
7. After properly placing the thrust washer (not
shown on drawing) on the jack screw, insert the
jack screw through the top thrust plate and thread
the jack screw into the pressure plate about 1”.
8. Lift the top thrust plate up and off the guide pin.
Turn the top thrust plate so that the guide pin does
not re-enter the slot.Lower the top thrust plate and
allow it to rest on top of the guide pin.
9. Lubricate approximately 1” of the jack screw
where it enters the pressure plate with white lube
or a wheel bearing type of grease. Also place a
dab of this grease on both sides of the thrust
washer that is placed under the hex head of the
jack screw.
10. Position the stator leads so that they will not snag
on the pressure plate when the pressure plate is
being inserted into, then through, the stator. Bend
the stator leads over the top of the support ring
(this will help to eliminate interference).
11. Wrap a clean shop towel around the jack screw
and lift the pressure plate/jack screw/top thrust
plate assembly. Insert the pressure plate into and
through the top stator assembly. Position the
pressure plate in the space between the two
stators, where the field coil had been. Turn the
pressure plate to align the poles of the pressure
plate with the poles of the stator. This is easily
done by grasping both the jack screw and guide
pin and twisting. The pressure plate will then
rotate. Before releasing the assembly, make sure
the top thrust plate will once again rest on the end
of the guide pin, not the support ring.
12. Position the stator leads inside the support ring.
Firmly grab the top thrust plate at the outer edge,
twist slightly until the guide pin enters the curved
slot. Lower the top thrust plate onto the support
ring. The top of the support ring should enter the
mating groove in the top thrust plate.
13. Thread the jack screw in, until the head of the jack
screw contacts the top thrust plate.
14. Look through the large diameter holes (torque arm
holes) in the thrust plate to confirm the proper
seating of the pressure plate steps against the
stator. Adjust the pressure plate as necessary.
NOTE: The pressure plate is properly seated when the
outer edge of the pressure plate presses against the
field coil mounting tabs on the stator. Make sure that
ALL field coil mounting tabs are in contact with the
pressure plate.
15. Continue threading the jack screw in, until signifi-
cant resistance is felt. Check position of the pres-
sure plate again.
M13-26
Niehoff Alternator Overhaul Manual
M13003 04/01
Summary of Contents for 930E-2
Page 1: ......
Page 2: ......
Page 4: ...NOTES ...
Page 8: ...KOMATSU MODEL 930E Dump Truck A 4 Introduction A00017 03 01 ...
Page 10: ...NOTES A1 2 Index A01001 2 94 ...
Page 12: ...930E MAJOR COMPONENTS A2 2 Major Component Description A02055 ...
Page 35: ...START HERE Walk Around Inspection A03017 General Safety and Operating Instructions A3 21 ...
Page 46: ...NOTES A3 32 General Safety and Operating Instructions A03017 ...
Page 78: ...NOTES B1 2 Index B01016 ...
Page 88: ...NOTES B3 6 Dump Body B03013 03 01 ...
Page 92: ...NOTES B4 4 Fuel Tank B04015 ...
Page 94: ...NOTES C1 2 Index C01021 03 01 ...
Page 118: ...NOTES C5 6 Air Filtration System C05013 5 98 ...
Page 126: ...NOTES D2 6 24VDC Electric Supply System D02018 ...
Page 142: ...NOTES D3 16 24VDC System Components D03019 04 01 ...
Page 146: ...FIGURE 2 1 PROPULSION SYSTEM DIAGRAM E2 2 Electrical Propulsion System Components E02014 3 01 ...
Page 196: ...NOTES E2 52 Electrical Propulsion System Components E02014 3 01 ...
Page 240: ...NOTES E3 44 AC Drive System Electrical Checkout Procedure 3 01 E03015 Release 17 Software ...
Page 242: ...NOTES G1 2 Index G01017 ...
Page 250: ...NOTES G2 8 Tires and Rims G02015 ...
Page 274: ...NOTES H1 2 Index H01013 04 01 ...
Page 282: ...NOTES H2 8 Front Suspensions H02013 2 01 ...
Page 288: ...NOTES H3 6 Rear Suspensions H03013 ...
Page 334: ...NOTES J3 32 Brake Circuit Component Service J03019 1 99 ...
Page 378: ...NOTES L2 8 Hydraulic System L02028 ...
Page 401: ...FIGURE 4 5 FLOW AMPLIFIER VALVE L04031 Steering Circuit L4 7 ...
Page 403: ...FIGURE 4 6 FLOW AMPLIFIER NO STEER L04031 Steering Circuit L4 9 ...
Page 405: ...FIGURE 4 7 FLOW AMPLIFIER LEFT STEER L04031 Steering Circuit L4 11 ...
Page 407: ...FIGURE 4 8 FLOW AMPLIFIER RIGHT STEER L04031 Steering Circuit L4 13 ...
Page 409: ...FIGURE 4 9 FLOW AMPLIFIER NO STEER EXTERNAL SHOCK LOAD L04031 Steering Circuit L4 15 ...
Page 414: ...NOTES L4 20 Steering Circuit L04031 ...
Page 422: ...NOTES L5 8 Steering Control Unit L05021 ...
Page 429: ...L06021 Steering Circuit Component Repair L6 7 ...
Page 450: ...NOTES L6 28 Steering Circuit Component Repair L06021 ...
Page 466: ...NOTES L7 16 Hoist Circuit L07023 ...
Page 492: ...NOTES L9 6 Hydraulic System Filters L09008 ...
Page 504: ...NOTES L10 12 Hydraulic Check out Procedure L10012 ...
Page 508: ...NOTES M1 2 Index M01034 03 01 ...
Page 518: ...NOTES M2 3 10 Ansul Checkfire Electric Detection and Actuation System M02003 ...
Page 524: ...NOTES M5 4 Wiggins Quick Fill Fuel System M05002 10 96 ...
Page 532: ...NOTES M8 8 Special Tools M08012 9 99 ...
Page 560: ...NOTES M9 28 Air Conditioning System M09010 6 97 for HFC 134a Refrigerant ...
Page 618: ...M20 20 Payload Meter II M20007 10 00 ...
Page 619: ...M20007 10 00 Payload Meter II M20 21 ...
Page 627: ...M20007 10 00 Payload Meter II M20 29 ...
Page 634: ...NOTES N1 2 Index N01020 03 01 ...
Page 654: ...NOTES N3 6 Cab Components N03011 7 98 ...
Page 660: ...NOTES N4 6 Operator Comfort N04020 ...
Page 686: ...NOTES N5 26 Operator Cab Controls N05044 ...
Page 688: ...NOTES P1 2 Index P01024 ...
Page 691: ...P02034 Lubrication and Service P2 3 ...
Page 722: ......
Page 723: ......
Page 724: ......
Page 725: ......
Page 726: ......
Page 727: ......
Page 728: ......
Page 729: ......
Page 730: ......
Page 731: ......
Page 732: ......
Page 733: ......
Page 734: ......
Page 735: ......
Page 736: ......
Page 737: ...NOTES R1 2 930E Schematics R01048 with Cummins QSK60 Series Engine ...
Page 738: ......
Page 739: ......