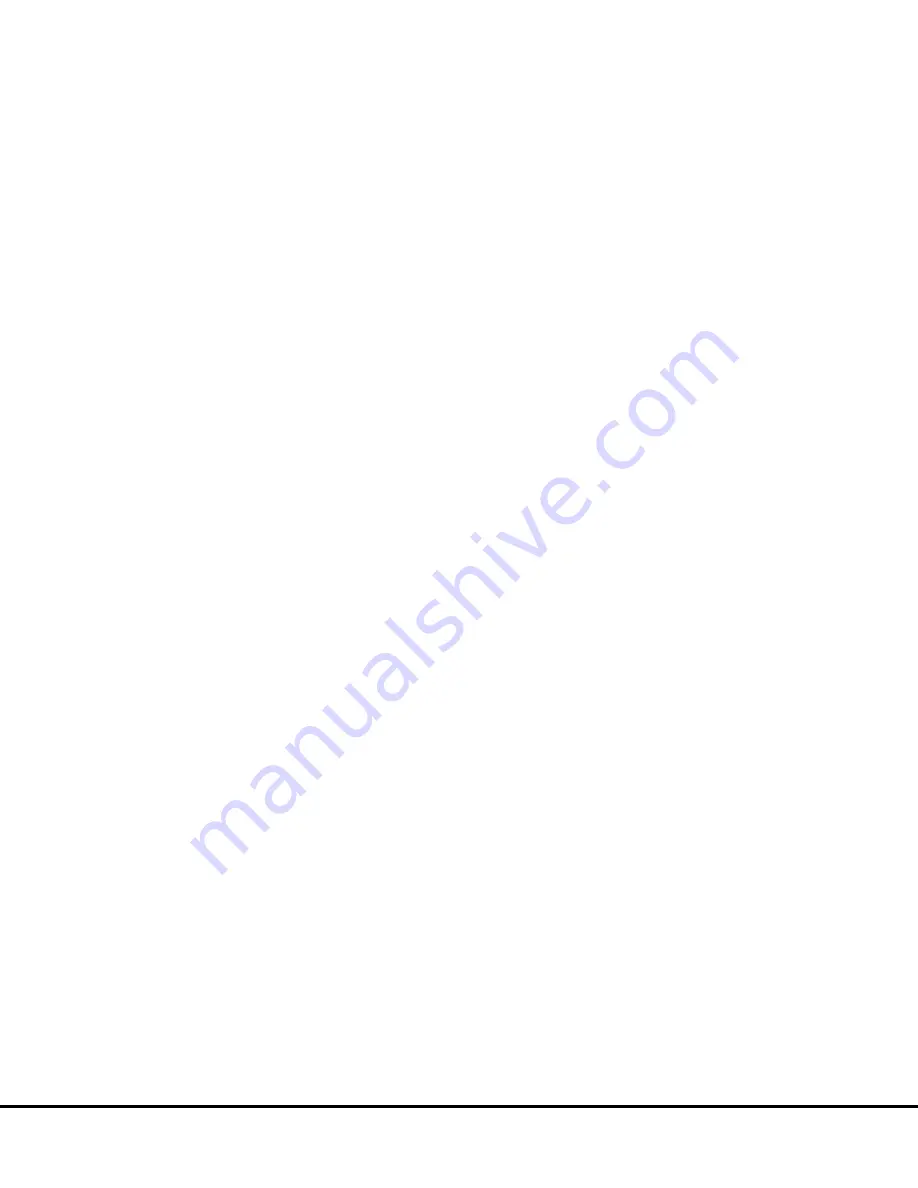
POWER UP OPERATION (Figure 7-6)
The hoist pilot valve spool is moved to the Power Up
position when the operator moves the lever rearward
in the cab. The pilot supply oil coming in port (12) is
prevented from returning to the tank and, instead, is
directed out port (14) through hoist limit solenoid (13)
in the bleeddown manifold and into port (14) of the
hoist valve.
From there it goes to the top of the head end spool (8),
builds pressure on the end of the spool, causes the
spool to move down compressing the bottom spring,
and connects the high pressure passage (19) to head
end port (9). Working oil flow in the high pressure
passage is now allowed to flow through the spool (8)
and out port (9) to extend the hoist cylinders.
Even though a small amount of oil flows through the
check poppet in the top of Spool (8), raise pilot pres-
sure at ports (14) increases to slightly higher pressure
than the required hoist cylinder pressure. As a result,
the pilot supply pressure in ports (12) also increases
causing back pressure to occur in the spring area of
the flow control valve (2). This overcomes the pilot
pressure on the other end of the flow control valve
causing it to close and direct the incoming pump oil
through the head end spool (8) to the hoist cylinders
to extend them. At this time, oil flow to the brake cooling
circuit is stopped.
If at any time the resistance to the flow of the pump oil
coming into the inlet section causes the pressure to
increase to 2500 psi (17,238 kPa), the pilot pressure
against hoist relief valve (1) causes it to open and allow
flow to exit out port (23) to the brake cooling circuit and
to return to the tank.
As the hoist cylinders extend, oil in the annulus area
of all three stages must exit sequentially from the
cylinders. Initially, the rod end spool (7) ports are
closed. As the returning oil entering port (5) builds low
pressure, it flows through the check-poppet in the top
of the spool, through Ports (15), through the pilot valve
spool, and out port (10) of the pilot valve to the bleed-
down manifold and to the tank.
No pressure is present on the top of spool (7). Cylinder
return pressure passes through the check-poppet in
the bottom of spool (7) to build pressure under the
spool which moves the spool upward compressing the
top spring. This movement allows the returning cylin-
der oil to flow into the low pressure passage (20) to
the primary low pressure relief valve (22). Approxi-
mately 26 psi (179 kPa) causes this valve to open,
allowing the oil to flow out port (10) to the tank.
If the load passing over the tail of the body during
dumping attempts to cause the body to raise faster
than the oil being supplied by the pump, the oil return-
ing from the annulus area of the hoist cylinders passing
through the conterbalance valve manifold controls how
fast the hoist cylinders can extend due to the external
force of the load. The speed is controlled by counter-
balance valve.
During the normal raise process, the raise pilot pres-
sure supplied to the counterbalance valve (24) will
open the cylinder return ports fully any time raise
pressure is above 666 psi (4,600 kPa). As the load
shifts toward the tail of the body, the raise pressure
decreases. As it drops below 666 psi (4,600 kPa), the
valve starts restricting oil flow causing a backpressure
to the annulus area. If raise pressure were to drop to
0 psi (kPa), return pressure would increase to 3000 psi
(20,400 kPa) maximum.
When the operator releases the hoist lever, the valves
change to the HOLD position. If the body raises to the
position that activates the hoist limit switch located
above the right rear suspension before the operator
releases the lever, the hoist limit solenoid (13) is ener-
gized. The solenoid valve closes the raise pilot Port
(14) on the hoist and releases the hoist pilot valve raise
pilot pressure at port (14) to tank, allowing the head
end spool (8) to center and shut off supply of oil to the
hoist cylinders. This prevents maximum extension of
the hoist cylinders.
L7-8
Hoist Circuit
L07023
Summary of Contents for 930E-2
Page 1: ......
Page 2: ......
Page 4: ...NOTES ...
Page 8: ...KOMATSU MODEL 930E Dump Truck A 4 Introduction A00017 03 01 ...
Page 10: ...NOTES A1 2 Index A01001 2 94 ...
Page 12: ...930E MAJOR COMPONENTS A2 2 Major Component Description A02055 ...
Page 35: ...START HERE Walk Around Inspection A03017 General Safety and Operating Instructions A3 21 ...
Page 46: ...NOTES A3 32 General Safety and Operating Instructions A03017 ...
Page 78: ...NOTES B1 2 Index B01016 ...
Page 88: ...NOTES B3 6 Dump Body B03013 03 01 ...
Page 92: ...NOTES B4 4 Fuel Tank B04015 ...
Page 94: ...NOTES C1 2 Index C01021 03 01 ...
Page 118: ...NOTES C5 6 Air Filtration System C05013 5 98 ...
Page 126: ...NOTES D2 6 24VDC Electric Supply System D02018 ...
Page 142: ...NOTES D3 16 24VDC System Components D03019 04 01 ...
Page 146: ...FIGURE 2 1 PROPULSION SYSTEM DIAGRAM E2 2 Electrical Propulsion System Components E02014 3 01 ...
Page 196: ...NOTES E2 52 Electrical Propulsion System Components E02014 3 01 ...
Page 240: ...NOTES E3 44 AC Drive System Electrical Checkout Procedure 3 01 E03015 Release 17 Software ...
Page 242: ...NOTES G1 2 Index G01017 ...
Page 250: ...NOTES G2 8 Tires and Rims G02015 ...
Page 274: ...NOTES H1 2 Index H01013 04 01 ...
Page 282: ...NOTES H2 8 Front Suspensions H02013 2 01 ...
Page 288: ...NOTES H3 6 Rear Suspensions H03013 ...
Page 334: ...NOTES J3 32 Brake Circuit Component Service J03019 1 99 ...
Page 378: ...NOTES L2 8 Hydraulic System L02028 ...
Page 401: ...FIGURE 4 5 FLOW AMPLIFIER VALVE L04031 Steering Circuit L4 7 ...
Page 403: ...FIGURE 4 6 FLOW AMPLIFIER NO STEER L04031 Steering Circuit L4 9 ...
Page 405: ...FIGURE 4 7 FLOW AMPLIFIER LEFT STEER L04031 Steering Circuit L4 11 ...
Page 407: ...FIGURE 4 8 FLOW AMPLIFIER RIGHT STEER L04031 Steering Circuit L4 13 ...
Page 409: ...FIGURE 4 9 FLOW AMPLIFIER NO STEER EXTERNAL SHOCK LOAD L04031 Steering Circuit L4 15 ...
Page 414: ...NOTES L4 20 Steering Circuit L04031 ...
Page 422: ...NOTES L5 8 Steering Control Unit L05021 ...
Page 429: ...L06021 Steering Circuit Component Repair L6 7 ...
Page 450: ...NOTES L6 28 Steering Circuit Component Repair L06021 ...
Page 466: ...NOTES L7 16 Hoist Circuit L07023 ...
Page 492: ...NOTES L9 6 Hydraulic System Filters L09008 ...
Page 504: ...NOTES L10 12 Hydraulic Check out Procedure L10012 ...
Page 508: ...NOTES M1 2 Index M01034 03 01 ...
Page 518: ...NOTES M2 3 10 Ansul Checkfire Electric Detection and Actuation System M02003 ...
Page 524: ...NOTES M5 4 Wiggins Quick Fill Fuel System M05002 10 96 ...
Page 532: ...NOTES M8 8 Special Tools M08012 9 99 ...
Page 560: ...NOTES M9 28 Air Conditioning System M09010 6 97 for HFC 134a Refrigerant ...
Page 618: ...M20 20 Payload Meter II M20007 10 00 ...
Page 619: ...M20007 10 00 Payload Meter II M20 21 ...
Page 627: ...M20007 10 00 Payload Meter II M20 29 ...
Page 634: ...NOTES N1 2 Index N01020 03 01 ...
Page 654: ...NOTES N3 6 Cab Components N03011 7 98 ...
Page 660: ...NOTES N4 6 Operator Comfort N04020 ...
Page 686: ...NOTES N5 26 Operator Cab Controls N05044 ...
Page 688: ...NOTES P1 2 Index P01024 ...
Page 691: ...P02034 Lubrication and Service P2 3 ...
Page 722: ......
Page 723: ......
Page 724: ......
Page 725: ......
Page 726: ......
Page 727: ......
Page 728: ......
Page 729: ......
Page 730: ......
Page 731: ......
Page 732: ......
Page 733: ......
Page 734: ......
Page 735: ......
Page 736: ......
Page 737: ...NOTES R1 2 930E Schematics R01048 with Cummins QSK60 Series Engine ...
Page 738: ......
Page 739: ......