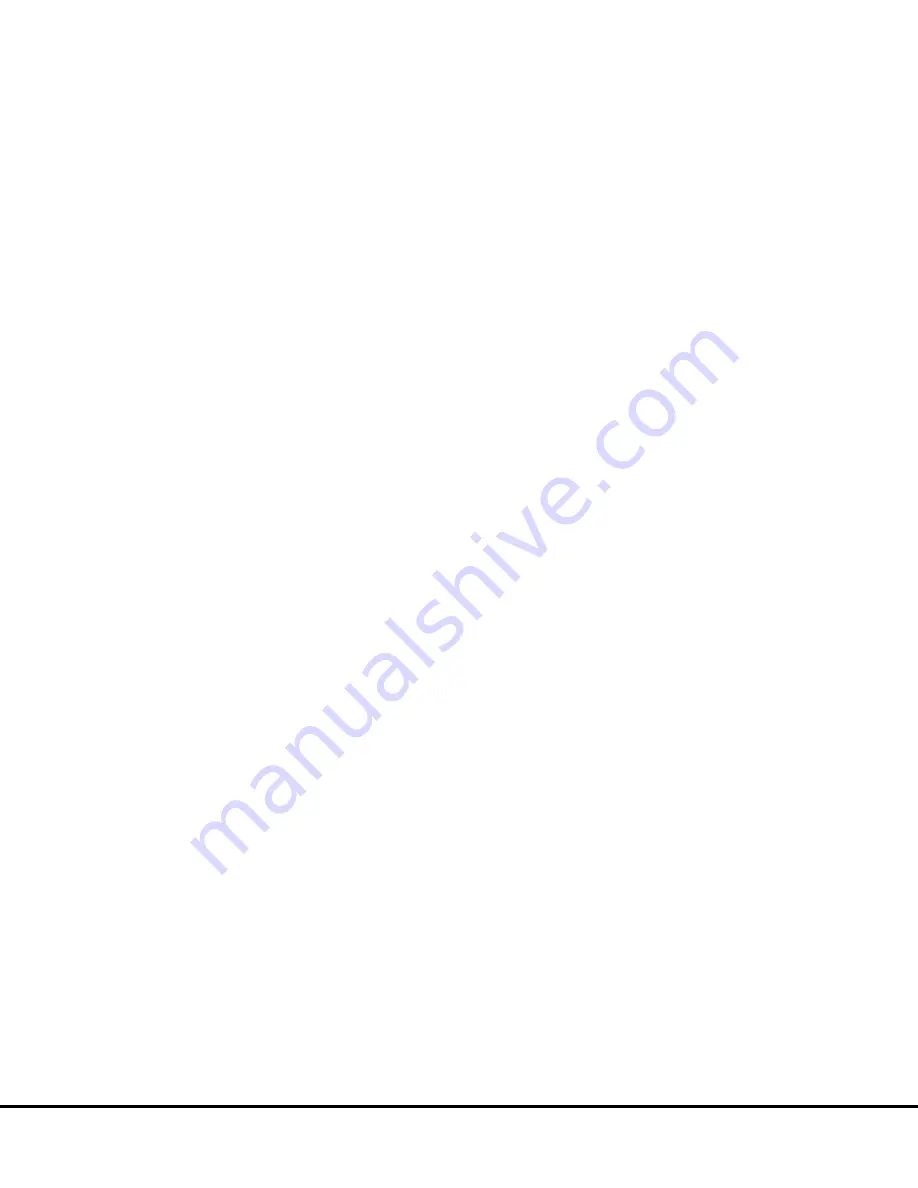
PSC SOFTWARE FUNCTIONS
The operation of the AC Drive System is regulated by
a software program which resides in the Propulsion
System Control Panel’s memory. The software pro-
gram also contains instructions to test and fault isolate
the system.
This section describes the PSC software program and
its functions without regard to hardware.
INPUT PROCESSING
This function reads in all external inputs for use by the
PSC. The Input Processing function performs any
signal conditioning required and computes the re-
quired derived inputs.
STATE MANAGEMENT
State Machine
As part of the total software package, a particular
group of regulatory software commands is included
called a “state machine”. The state machine controls
the various functions of truck operation.
The software implements the state machine by keep-
ing track of which state the truck is in, and which state
the truck is allowed to move into if the operator re-
quests a different mode of operation. Each software
state is defined as follows:
Startup/Shutdown State:
The purpose of this state is to ensure the system is in
a desired known state upon startup or shutdown. This
is an unpowered state.
NOTE: Powered and unpowered refer to the state of
the DC link; 600 volts or more on the DC link equals
“powered”. 50 volts or less on the DC link equals
“unpowered”.
Test State:
The purpose of this state is to provide an environment
for the verification of system functionality. Test state
will support a variety of activities, including:
1. Waiting for the engine to start (if needed).
2. Automatic testing on initial system startup or
following rest state.
3. Application of power to the DC link.
4. Externally initiated testing to clear a fault, set
temporary variables, or for maintenance pur-
poses.
NOTE: The Test state may be either powered or
unpowered at a given point in time, depending on
which activities are being performed.
Ready State:
Ready state is the default powered state. The system
will be in this state whenever the engine and control
system are ready to provide power, but none is re-
quested.
Ready state also is the state where the DC link is
discharged in preparation for Shutdown, Rest, or in
reaction to certain event conditions. Therefore, Ready
state should not be considered strictly a powered state
(as are Propel and Retard described below).
Rest State:
Rest is an unpowered state whose purpose is to
conserve fuel while the truck idles for an extended
period of time. Rest state also provides an environ-
ment where maintenance personnel can control the
engine without causing power to be applied to the DC
link.
Propel State:
The purpose of this state is to provide the power
system configuration and overall environment for en-
gine-powered propulsion. This is strictly a powered
state, i.e., the system will not be allowed to maintain
propel state without sufficient power on the DC link.
E2-30
Electrical Propulsion System Components
E02014 3/01
Summary of Contents for 930E-2
Page 1: ......
Page 2: ......
Page 4: ...NOTES ...
Page 8: ...KOMATSU MODEL 930E Dump Truck A 4 Introduction A00017 03 01 ...
Page 10: ...NOTES A1 2 Index A01001 2 94 ...
Page 12: ...930E MAJOR COMPONENTS A2 2 Major Component Description A02055 ...
Page 35: ...START HERE Walk Around Inspection A03017 General Safety and Operating Instructions A3 21 ...
Page 46: ...NOTES A3 32 General Safety and Operating Instructions A03017 ...
Page 78: ...NOTES B1 2 Index B01016 ...
Page 88: ...NOTES B3 6 Dump Body B03013 03 01 ...
Page 92: ...NOTES B4 4 Fuel Tank B04015 ...
Page 94: ...NOTES C1 2 Index C01021 03 01 ...
Page 118: ...NOTES C5 6 Air Filtration System C05013 5 98 ...
Page 126: ...NOTES D2 6 24VDC Electric Supply System D02018 ...
Page 142: ...NOTES D3 16 24VDC System Components D03019 04 01 ...
Page 146: ...FIGURE 2 1 PROPULSION SYSTEM DIAGRAM E2 2 Electrical Propulsion System Components E02014 3 01 ...
Page 196: ...NOTES E2 52 Electrical Propulsion System Components E02014 3 01 ...
Page 240: ...NOTES E3 44 AC Drive System Electrical Checkout Procedure 3 01 E03015 Release 17 Software ...
Page 242: ...NOTES G1 2 Index G01017 ...
Page 250: ...NOTES G2 8 Tires and Rims G02015 ...
Page 274: ...NOTES H1 2 Index H01013 04 01 ...
Page 282: ...NOTES H2 8 Front Suspensions H02013 2 01 ...
Page 288: ...NOTES H3 6 Rear Suspensions H03013 ...
Page 334: ...NOTES J3 32 Brake Circuit Component Service J03019 1 99 ...
Page 378: ...NOTES L2 8 Hydraulic System L02028 ...
Page 401: ...FIGURE 4 5 FLOW AMPLIFIER VALVE L04031 Steering Circuit L4 7 ...
Page 403: ...FIGURE 4 6 FLOW AMPLIFIER NO STEER L04031 Steering Circuit L4 9 ...
Page 405: ...FIGURE 4 7 FLOW AMPLIFIER LEFT STEER L04031 Steering Circuit L4 11 ...
Page 407: ...FIGURE 4 8 FLOW AMPLIFIER RIGHT STEER L04031 Steering Circuit L4 13 ...
Page 409: ...FIGURE 4 9 FLOW AMPLIFIER NO STEER EXTERNAL SHOCK LOAD L04031 Steering Circuit L4 15 ...
Page 414: ...NOTES L4 20 Steering Circuit L04031 ...
Page 422: ...NOTES L5 8 Steering Control Unit L05021 ...
Page 429: ...L06021 Steering Circuit Component Repair L6 7 ...
Page 450: ...NOTES L6 28 Steering Circuit Component Repair L06021 ...
Page 466: ...NOTES L7 16 Hoist Circuit L07023 ...
Page 492: ...NOTES L9 6 Hydraulic System Filters L09008 ...
Page 504: ...NOTES L10 12 Hydraulic Check out Procedure L10012 ...
Page 508: ...NOTES M1 2 Index M01034 03 01 ...
Page 518: ...NOTES M2 3 10 Ansul Checkfire Electric Detection and Actuation System M02003 ...
Page 524: ...NOTES M5 4 Wiggins Quick Fill Fuel System M05002 10 96 ...
Page 532: ...NOTES M8 8 Special Tools M08012 9 99 ...
Page 560: ...NOTES M9 28 Air Conditioning System M09010 6 97 for HFC 134a Refrigerant ...
Page 618: ...M20 20 Payload Meter II M20007 10 00 ...
Page 619: ...M20007 10 00 Payload Meter II M20 21 ...
Page 627: ...M20007 10 00 Payload Meter II M20 29 ...
Page 634: ...NOTES N1 2 Index N01020 03 01 ...
Page 654: ...NOTES N3 6 Cab Components N03011 7 98 ...
Page 660: ...NOTES N4 6 Operator Comfort N04020 ...
Page 686: ...NOTES N5 26 Operator Cab Controls N05044 ...
Page 688: ...NOTES P1 2 Index P01024 ...
Page 691: ...P02034 Lubrication and Service P2 3 ...
Page 722: ......
Page 723: ......
Page 724: ......
Page 725: ......
Page 726: ......
Page 727: ......
Page 728: ......
Page 729: ......
Page 730: ......
Page 731: ......
Page 732: ......
Page 733: ......
Page 734: ......
Page 735: ......
Page 736: ......
Page 737: ...NOTES R1 2 930E Schematics R01048 with Cummins QSK60 Series Engine ...
Page 738: ......
Page 739: ......