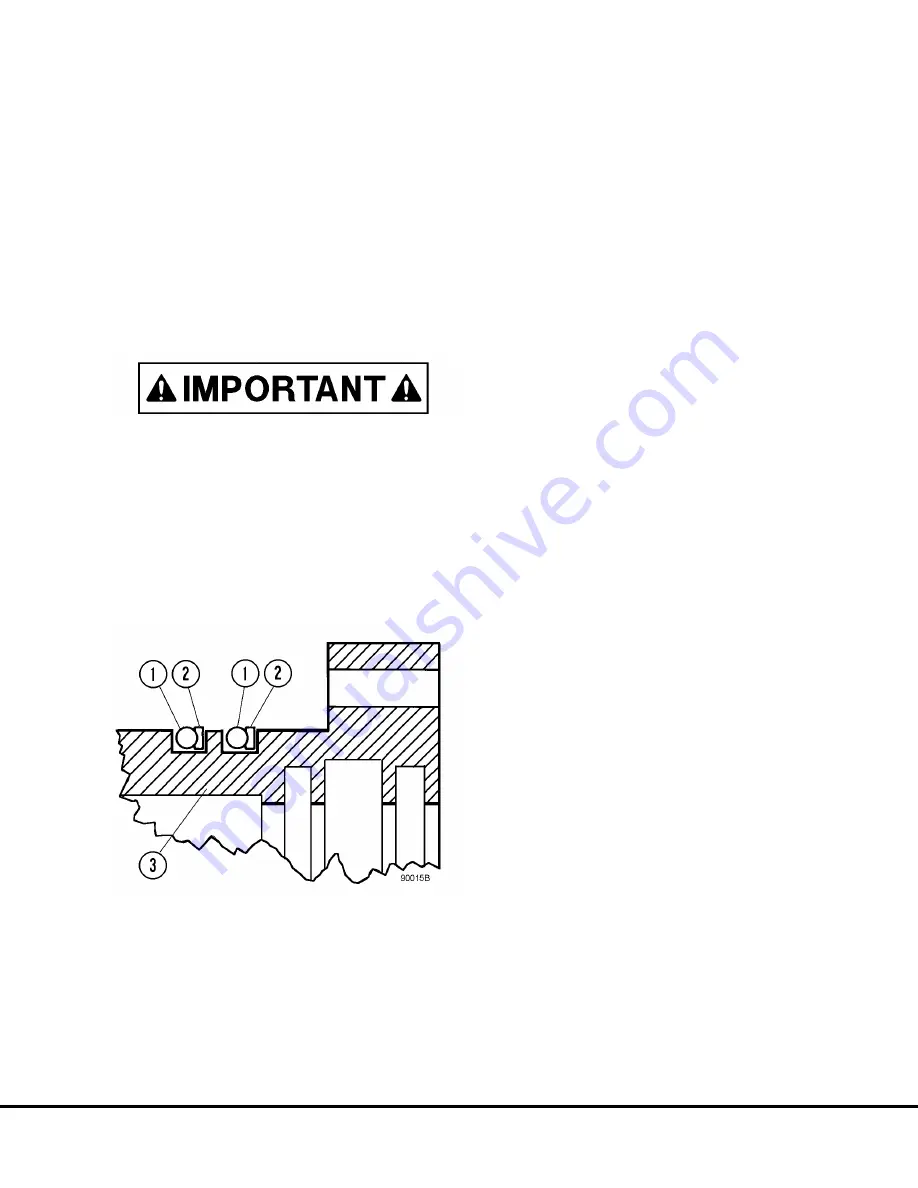
Assembly
NOTE: All parts must be completely dry and free of
foreign material. Lubricate all interior parts with clean
HYDRAIR
®
suspension oil (see Oil Specification un-
der “Oiling and Charging Procedure”).
Take care not to damage the machined or plated
surfaces, O-rings or seals when installing piston
assembly.
1. Install new rod seal (28, Figure 2-8), step seal
(27), and rod wiper (29).
When installing backup rings with rod seal (28)
and step seal (27), be certain radius is positioned
toward the seal and the white dot is positioned
away from the seal as shown in Figure 2-8.
2. Install new O-rings (22) and backup rings (23) in
their appropriate grooves in the bearing retainer
(18).
NOTE: Backup rings must be positioned toward bear-
ing retainer bolt flange as shown in Figure 2-9.
3. Install lower bearing (18) into lubricated suspen-
sion housing. Install capscrews and hardened
lockwashers (20 & 21) through bearing flange and
into tapped holes in housing. Tighten to 500 ft.
lbs. (678 N.m) torque.
4. Install new backup rings and O-rings (15, Figure
2-7) in end cap grooves. Backup rings must be
positioned toward the flange on the end cap.
5. Install new bearing (14) on upper bearing retainer
(5).
6. Slide upper bearing retainer assembly over cap
structure rod (16).
7. Install key (13) and piston stop (12) on cap struc-
ture rod. Make sure piston stop is fully seated
against the rod shoulder. Install locknut (11)
against piston stop. Tighten locknut one half turn
further, until hole for the roll pin (10) is in align-
ment. Install roll pin.
8. Attach a lifting device to top side of end cap
assembly. Lower assembly down on piston (7).
Insert steel balls (9) in holes in piston prior to fully
seating bearing on top of piston. A small amount
of petroleum jelly will prevent the balls from drop-
ping out during assembly.
9. Install upper bearing retainer (5) onto piston rod.
Secure bearing in place with NEW capscrews (3)
and hardened washers (4). Tighten capscrews to
500 ft. lbs. (678 N.m) torque.
NOTE: ALWAYS use new capscrews (3, Figure 2-7)
during assembly. Used capscrews will be stressed and
fatigued because of loads imposed on these cap-
screws during operation.
10. Apply a light coating of petroleum jelly to the seals,
wiper and bearings. With suspension housing in a
vertical position, carefully lower the piston rod and
end cap assembly into the bore of the cylinder
housing to its fully retracted position
11. Install capscrews and hardened washers (1 & 2)
and tighten to 500 ft. lbs. (678 N.m) torque.
12. Install bottom plug (19, Figure 2-8) and tighten to
13 ft. lbs. (17.5 N.m) torque.
NOTE: If suspension is to be stored, put in two pints
(1.0 l) of a rust preventive oil. This oil must be drained
when suspension is put into service.
13. Install charging valve and new O-ring (5, Figure
2-1). Lubricate O-rings with clean HYDRAIR
®
oil
before threading into end cap. Tighten large hex
of charging valve to 16.5 ft. lbs. (27.4 N.m) torque.
FIGURE 2-9. BACK-UP RING PLACEMENT
1. O-Ring
2. Backup Ring
3. Bearing Retainer
H02013 2/01
Front Suspensions
H2-7
Summary of Contents for 930E-2
Page 1: ......
Page 2: ......
Page 4: ...NOTES ...
Page 8: ...KOMATSU MODEL 930E Dump Truck A 4 Introduction A00017 03 01 ...
Page 10: ...NOTES A1 2 Index A01001 2 94 ...
Page 12: ...930E MAJOR COMPONENTS A2 2 Major Component Description A02055 ...
Page 35: ...START HERE Walk Around Inspection A03017 General Safety and Operating Instructions A3 21 ...
Page 46: ...NOTES A3 32 General Safety and Operating Instructions A03017 ...
Page 78: ...NOTES B1 2 Index B01016 ...
Page 88: ...NOTES B3 6 Dump Body B03013 03 01 ...
Page 92: ...NOTES B4 4 Fuel Tank B04015 ...
Page 94: ...NOTES C1 2 Index C01021 03 01 ...
Page 118: ...NOTES C5 6 Air Filtration System C05013 5 98 ...
Page 126: ...NOTES D2 6 24VDC Electric Supply System D02018 ...
Page 142: ...NOTES D3 16 24VDC System Components D03019 04 01 ...
Page 146: ...FIGURE 2 1 PROPULSION SYSTEM DIAGRAM E2 2 Electrical Propulsion System Components E02014 3 01 ...
Page 196: ...NOTES E2 52 Electrical Propulsion System Components E02014 3 01 ...
Page 240: ...NOTES E3 44 AC Drive System Electrical Checkout Procedure 3 01 E03015 Release 17 Software ...
Page 242: ...NOTES G1 2 Index G01017 ...
Page 250: ...NOTES G2 8 Tires and Rims G02015 ...
Page 274: ...NOTES H1 2 Index H01013 04 01 ...
Page 282: ...NOTES H2 8 Front Suspensions H02013 2 01 ...
Page 288: ...NOTES H3 6 Rear Suspensions H03013 ...
Page 334: ...NOTES J3 32 Brake Circuit Component Service J03019 1 99 ...
Page 378: ...NOTES L2 8 Hydraulic System L02028 ...
Page 401: ...FIGURE 4 5 FLOW AMPLIFIER VALVE L04031 Steering Circuit L4 7 ...
Page 403: ...FIGURE 4 6 FLOW AMPLIFIER NO STEER L04031 Steering Circuit L4 9 ...
Page 405: ...FIGURE 4 7 FLOW AMPLIFIER LEFT STEER L04031 Steering Circuit L4 11 ...
Page 407: ...FIGURE 4 8 FLOW AMPLIFIER RIGHT STEER L04031 Steering Circuit L4 13 ...
Page 409: ...FIGURE 4 9 FLOW AMPLIFIER NO STEER EXTERNAL SHOCK LOAD L04031 Steering Circuit L4 15 ...
Page 414: ...NOTES L4 20 Steering Circuit L04031 ...
Page 422: ...NOTES L5 8 Steering Control Unit L05021 ...
Page 429: ...L06021 Steering Circuit Component Repair L6 7 ...
Page 450: ...NOTES L6 28 Steering Circuit Component Repair L06021 ...
Page 466: ...NOTES L7 16 Hoist Circuit L07023 ...
Page 492: ...NOTES L9 6 Hydraulic System Filters L09008 ...
Page 504: ...NOTES L10 12 Hydraulic Check out Procedure L10012 ...
Page 508: ...NOTES M1 2 Index M01034 03 01 ...
Page 518: ...NOTES M2 3 10 Ansul Checkfire Electric Detection and Actuation System M02003 ...
Page 524: ...NOTES M5 4 Wiggins Quick Fill Fuel System M05002 10 96 ...
Page 532: ...NOTES M8 8 Special Tools M08012 9 99 ...
Page 560: ...NOTES M9 28 Air Conditioning System M09010 6 97 for HFC 134a Refrigerant ...
Page 618: ...M20 20 Payload Meter II M20007 10 00 ...
Page 619: ...M20007 10 00 Payload Meter II M20 21 ...
Page 627: ...M20007 10 00 Payload Meter II M20 29 ...
Page 634: ...NOTES N1 2 Index N01020 03 01 ...
Page 654: ...NOTES N3 6 Cab Components N03011 7 98 ...
Page 660: ...NOTES N4 6 Operator Comfort N04020 ...
Page 686: ...NOTES N5 26 Operator Cab Controls N05044 ...
Page 688: ...NOTES P1 2 Index P01024 ...
Page 691: ...P02034 Lubrication and Service P2 3 ...
Page 722: ......
Page 723: ......
Page 724: ......
Page 725: ......
Page 726: ......
Page 727: ......
Page 728: ......
Page 729: ......
Page 730: ......
Page 731: ......
Page 732: ......
Page 733: ......
Page 734: ......
Page 735: ......
Page 736: ......
Page 737: ...NOTES R1 2 930E Schematics R01048 with Cummins QSK60 Series Engine ...
Page 738: ......
Page 739: ......