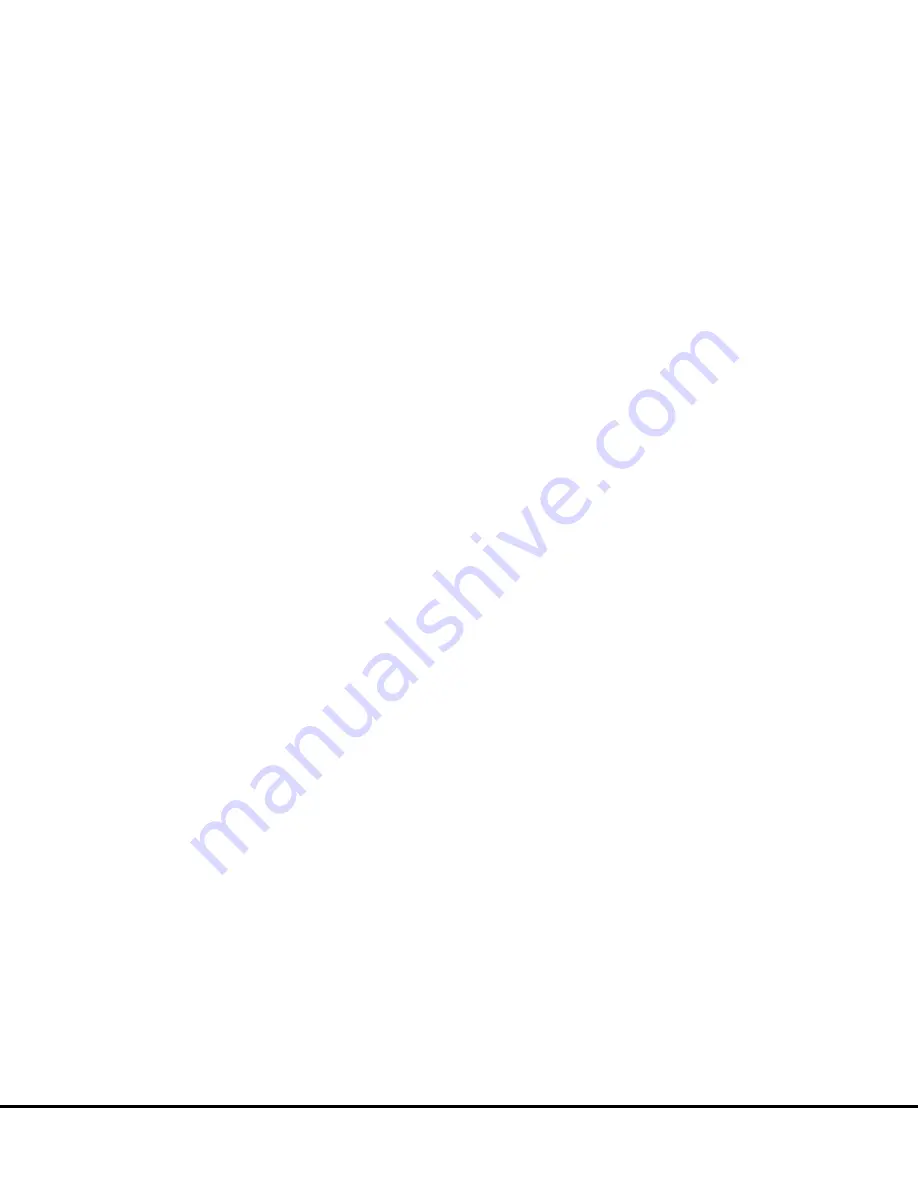
Event Logging And Storage
This software function is responsible for the recording
of event information. There are two basic levels of
event storage: event history buffer and data packs.
The event history buffer provides a minimum set of
information for a large number of events, while data
packs provide extensive information for a limited num-
ber of events.
The following requirements apply to both data packs
and the event history buffer:
1. Fault information is maintained until overwritten,
it is not cleared out following a reset. This allows
the user to examine data associated with events
that have been reset, as long as there have not
been so many new events as to necessitate reuse
of the storage space.
2. If a given event is active (logged and not reset),
logging of duplicate events (duplicate is defined
as having the same event and sub-id numbers)
will not be allowed. If the event is reset and
subsequently reoccurs, it may be logged again.
Likewise, if an event reoccurs with a different
sub-id from the original occurrence, the event
may be logged again.
Event History Buffer
Event history buffer is defined as a collection of event
history records.
A buffer contains 300 entries filled with event numbers
occurring in chronological order. Also included in this
buffer will be all the input and output values, time the
event occurred, reset time, state information, etc., for
each event. This buffer is filled continuously and over-
written (if necessary).
Limits (accept-limit) are placed on the amount of space
which a given event code may consume. This prevents
a frequently occurring event from using the memory
space at the expense of a less frequent event. This
data may be cleared (after downloading for trou-
bleshooting) at each maintenance interval.
Data Packs
A data pack is defined as an extended collection of
information relevant to a given event.
NOTE: The concepts of lockout, soft reset, and accept
limit do not apply to data packs.
Thirty (30) data packs are stored with each containing
100 frames of real time snapshot data. Snapshot data
is defined as a collection of key data parameter values
for a single point in time). The purpose of each data
pack is to show a little “movie” of what happened
before and after a fault.
The time interval between snapshots is default to 50
ms, but each data pack may be programmed via the
DID (or PTU) from 10 ms to 1 sec. (In multiples of 10
ms). The “TIME 0:00 frame #” at which the fault is
logged is default to frame #60, but each data pack is
programmable from 1 to 100.
In the above default cases, data is stored for 3 seconds
(2.95 second is actual) before the fault and 2 seconds
after the fault.
A data pack status structure is assigned to each data
pack plus any programmable settings. This status
structure is used by the TCI (or PTU) to check for
available data (event number, id, and status, should
be set to zero if data pack is not frozen), as well as for
control of the data packs.
If a data pack is unfrozen (not holding any particular
fault data), it is continually updated each 100 frames,
organized in a circular queue, with new real time
snapshot data. When a fault occurs, the frame number
at which the event occurred is used as a reference to
mark the end of the data pack, and data is collected
until the data pack is full. Only when the data pack is
full will the event number, id and status be updated in
the status structure.
All logic control variables are saved in battery backed
RAM, in case a fault occurs and battery power is cycled
before the data pack is filled with data (the software
allows for proper recovery and then continues to fill the
data pack). Maintenance personnel, by way of the DID
(or PTU), can assign the data pack to hold only certain
event numbers (for the case where it is desired to
collect data on a particular fault).
However, in the default case, faults will be stored as
they come until all data packs are frozen (holding fault
data). When all data packs are frozen, the data pack
with the fault that was RESET first (either automatically
or by the DID/PTU), if any, will be unfrozen and will
start storing new data in case a new fault occurs.
E2-38
Electrical Propulsion System Components
E02014 3/01
Summary of Contents for 930E-2
Page 1: ......
Page 2: ......
Page 4: ...NOTES ...
Page 8: ...KOMATSU MODEL 930E Dump Truck A 4 Introduction A00017 03 01 ...
Page 10: ...NOTES A1 2 Index A01001 2 94 ...
Page 12: ...930E MAJOR COMPONENTS A2 2 Major Component Description A02055 ...
Page 35: ...START HERE Walk Around Inspection A03017 General Safety and Operating Instructions A3 21 ...
Page 46: ...NOTES A3 32 General Safety and Operating Instructions A03017 ...
Page 78: ...NOTES B1 2 Index B01016 ...
Page 88: ...NOTES B3 6 Dump Body B03013 03 01 ...
Page 92: ...NOTES B4 4 Fuel Tank B04015 ...
Page 94: ...NOTES C1 2 Index C01021 03 01 ...
Page 118: ...NOTES C5 6 Air Filtration System C05013 5 98 ...
Page 126: ...NOTES D2 6 24VDC Electric Supply System D02018 ...
Page 142: ...NOTES D3 16 24VDC System Components D03019 04 01 ...
Page 146: ...FIGURE 2 1 PROPULSION SYSTEM DIAGRAM E2 2 Electrical Propulsion System Components E02014 3 01 ...
Page 196: ...NOTES E2 52 Electrical Propulsion System Components E02014 3 01 ...
Page 240: ...NOTES E3 44 AC Drive System Electrical Checkout Procedure 3 01 E03015 Release 17 Software ...
Page 242: ...NOTES G1 2 Index G01017 ...
Page 250: ...NOTES G2 8 Tires and Rims G02015 ...
Page 274: ...NOTES H1 2 Index H01013 04 01 ...
Page 282: ...NOTES H2 8 Front Suspensions H02013 2 01 ...
Page 288: ...NOTES H3 6 Rear Suspensions H03013 ...
Page 334: ...NOTES J3 32 Brake Circuit Component Service J03019 1 99 ...
Page 378: ...NOTES L2 8 Hydraulic System L02028 ...
Page 401: ...FIGURE 4 5 FLOW AMPLIFIER VALVE L04031 Steering Circuit L4 7 ...
Page 403: ...FIGURE 4 6 FLOW AMPLIFIER NO STEER L04031 Steering Circuit L4 9 ...
Page 405: ...FIGURE 4 7 FLOW AMPLIFIER LEFT STEER L04031 Steering Circuit L4 11 ...
Page 407: ...FIGURE 4 8 FLOW AMPLIFIER RIGHT STEER L04031 Steering Circuit L4 13 ...
Page 409: ...FIGURE 4 9 FLOW AMPLIFIER NO STEER EXTERNAL SHOCK LOAD L04031 Steering Circuit L4 15 ...
Page 414: ...NOTES L4 20 Steering Circuit L04031 ...
Page 422: ...NOTES L5 8 Steering Control Unit L05021 ...
Page 429: ...L06021 Steering Circuit Component Repair L6 7 ...
Page 450: ...NOTES L6 28 Steering Circuit Component Repair L06021 ...
Page 466: ...NOTES L7 16 Hoist Circuit L07023 ...
Page 492: ...NOTES L9 6 Hydraulic System Filters L09008 ...
Page 504: ...NOTES L10 12 Hydraulic Check out Procedure L10012 ...
Page 508: ...NOTES M1 2 Index M01034 03 01 ...
Page 518: ...NOTES M2 3 10 Ansul Checkfire Electric Detection and Actuation System M02003 ...
Page 524: ...NOTES M5 4 Wiggins Quick Fill Fuel System M05002 10 96 ...
Page 532: ...NOTES M8 8 Special Tools M08012 9 99 ...
Page 560: ...NOTES M9 28 Air Conditioning System M09010 6 97 for HFC 134a Refrigerant ...
Page 618: ...M20 20 Payload Meter II M20007 10 00 ...
Page 619: ...M20007 10 00 Payload Meter II M20 21 ...
Page 627: ...M20007 10 00 Payload Meter II M20 29 ...
Page 634: ...NOTES N1 2 Index N01020 03 01 ...
Page 654: ...NOTES N3 6 Cab Components N03011 7 98 ...
Page 660: ...NOTES N4 6 Operator Comfort N04020 ...
Page 686: ...NOTES N5 26 Operator Cab Controls N05044 ...
Page 688: ...NOTES P1 2 Index P01024 ...
Page 691: ...P02034 Lubrication and Service P2 3 ...
Page 722: ......
Page 723: ......
Page 724: ......
Page 725: ......
Page 726: ......
Page 727: ......
Page 728: ......
Page 729: ......
Page 730: ......
Page 731: ......
Page 732: ......
Page 733: ......
Page 734: ......
Page 735: ......
Page 736: ......
Page 737: ...NOTES R1 2 930E Schematics R01048 with Cummins QSK60 Series Engine ...
Page 738: ......
Page 739: ......