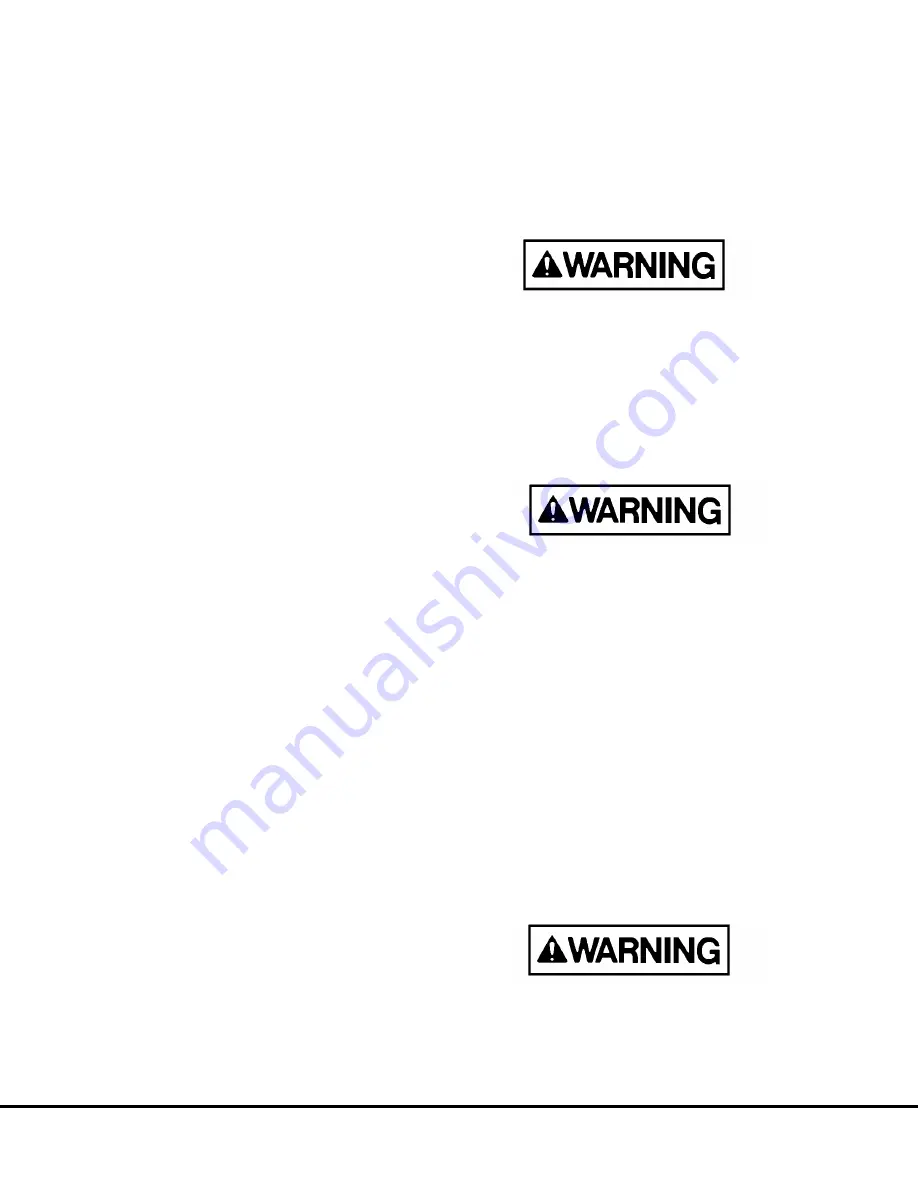
3. Be certain outlet valves (3) and inlet valve (4) are
closed (turned completely clockwise).
4. Turn swivel nut (small hex) on charging valve 3
full turns counterclockwise to unseat valve.
5. Attach charging valve adapters (2) to each sus-
pension charging valve stem.
6. Turn “T” handles (1) clockwise (this will depress
core of charging valve and open gas chamber of
suspension).
7. Open both outlet valves (3).
By selective opening and closing of outlet valves (3),
and inlet valve (4), suspensions may be charged sepa-
rately or together.
Removal of Charging Kit
1. Close both outlet valves (3).
2. Turn “T” handles (1) counterclockwise to release
charging valve cores.
3. Remove charging valve adapters (2) from charg-
ing valves.
4. Tighten swivel nut (small hex) on charging valve.
5. Install charging valve caps and protective covers
on both suspensions.
SUPPORT BLOCKS FOR OILING AND
CHARGING DIMENSIONS
Prior to starting oiling and charging procedures, sup-
ports should be fabricated which will maintain the
correct exposed piston rod extensions.
Exposed piston rod extensions are specified for both
oil level and nitrogen charging for HYDRAIR
®
II sus-
pensions. These dimensions are listed in the Tables
below Figures 4-2 and 4-4. Measure dimensions from
face of cylinder gland to machined surface on spindle
on front suspension. Measure from face of cylinder
gland to piston flange on rear suspension. Do NOT
include capscrew heads in measurements.
Support blocks may be made in various forms. Mild
steel materials are recommended. Square stock or
pipe segments [1 in. (25 mm) minimum] may be used.
Blocks must be capable of supporting the weight of the
truck during oiling and charging procedures while
avoiding contact with plated surfaces and seals on the
suspension. Refer to Figure 4-2 for front suspension
support block placement and Figure 4-4 for rear sup-
port block placement.
FRONT SUSPENSION
1. Park unloaded truck on a hard level surface. Block
wheels, apply parking brake.
2. Thoroughly clean area around charging valve on
the suspensions. Remove protective covers from
charging valves.
All HYDRAIR
®
II suspensions are charged with
compressed nitrogen gas with sufficient pressure
to cause injury or damage if improperly handled.
Follow all the safety notes, cautions and warnings
in these procedures to prevent accidents during
servicing and charging.
Front Suspension Oiling
When blocks are in place on a suspension, they
must be secured with a strap or other means to
insure the blocks stay in place while being used.
An unsecured block could fly loose as weight is
applied, presenting the possibility of serious in-
jury to nearby personnel and/or damage to the
equipment. Overhead clearance may be reduced
rapidly and suddenly when nitrogen pressure is
released!
1 . Position and secure oiling height dimension
blocks in place (Figure 4-2). When nitrogen pres-
sure is released, suspensions will lower to rest on
the blocks. Take care that blocks do not mar or
scratch plated surface of the piston nor damage
the wiper seals in the lower bearing retainer.
Support blocks must seat on the spindle and the
cylinder housing. Place 2 blocks (180° apart) on
each side of suspension to provide stability.
Wear a face mask or goggles while relieving nitro-
gen pressure.
H4-2
Oiling and Charging Procedures
H04005 9/99
730E, 830E, and 930E
Summary of Contents for 930E-2
Page 1: ......
Page 2: ......
Page 4: ...NOTES ...
Page 8: ...KOMATSU MODEL 930E Dump Truck A 4 Introduction A00017 03 01 ...
Page 10: ...NOTES A1 2 Index A01001 2 94 ...
Page 12: ...930E MAJOR COMPONENTS A2 2 Major Component Description A02055 ...
Page 35: ...START HERE Walk Around Inspection A03017 General Safety and Operating Instructions A3 21 ...
Page 46: ...NOTES A3 32 General Safety and Operating Instructions A03017 ...
Page 78: ...NOTES B1 2 Index B01016 ...
Page 88: ...NOTES B3 6 Dump Body B03013 03 01 ...
Page 92: ...NOTES B4 4 Fuel Tank B04015 ...
Page 94: ...NOTES C1 2 Index C01021 03 01 ...
Page 118: ...NOTES C5 6 Air Filtration System C05013 5 98 ...
Page 126: ...NOTES D2 6 24VDC Electric Supply System D02018 ...
Page 142: ...NOTES D3 16 24VDC System Components D03019 04 01 ...
Page 146: ...FIGURE 2 1 PROPULSION SYSTEM DIAGRAM E2 2 Electrical Propulsion System Components E02014 3 01 ...
Page 196: ...NOTES E2 52 Electrical Propulsion System Components E02014 3 01 ...
Page 240: ...NOTES E3 44 AC Drive System Electrical Checkout Procedure 3 01 E03015 Release 17 Software ...
Page 242: ...NOTES G1 2 Index G01017 ...
Page 250: ...NOTES G2 8 Tires and Rims G02015 ...
Page 274: ...NOTES H1 2 Index H01013 04 01 ...
Page 282: ...NOTES H2 8 Front Suspensions H02013 2 01 ...
Page 288: ...NOTES H3 6 Rear Suspensions H03013 ...
Page 334: ...NOTES J3 32 Brake Circuit Component Service J03019 1 99 ...
Page 378: ...NOTES L2 8 Hydraulic System L02028 ...
Page 401: ...FIGURE 4 5 FLOW AMPLIFIER VALVE L04031 Steering Circuit L4 7 ...
Page 403: ...FIGURE 4 6 FLOW AMPLIFIER NO STEER L04031 Steering Circuit L4 9 ...
Page 405: ...FIGURE 4 7 FLOW AMPLIFIER LEFT STEER L04031 Steering Circuit L4 11 ...
Page 407: ...FIGURE 4 8 FLOW AMPLIFIER RIGHT STEER L04031 Steering Circuit L4 13 ...
Page 409: ...FIGURE 4 9 FLOW AMPLIFIER NO STEER EXTERNAL SHOCK LOAD L04031 Steering Circuit L4 15 ...
Page 414: ...NOTES L4 20 Steering Circuit L04031 ...
Page 422: ...NOTES L5 8 Steering Control Unit L05021 ...
Page 429: ...L06021 Steering Circuit Component Repair L6 7 ...
Page 450: ...NOTES L6 28 Steering Circuit Component Repair L06021 ...
Page 466: ...NOTES L7 16 Hoist Circuit L07023 ...
Page 492: ...NOTES L9 6 Hydraulic System Filters L09008 ...
Page 504: ...NOTES L10 12 Hydraulic Check out Procedure L10012 ...
Page 508: ...NOTES M1 2 Index M01034 03 01 ...
Page 518: ...NOTES M2 3 10 Ansul Checkfire Electric Detection and Actuation System M02003 ...
Page 524: ...NOTES M5 4 Wiggins Quick Fill Fuel System M05002 10 96 ...
Page 532: ...NOTES M8 8 Special Tools M08012 9 99 ...
Page 560: ...NOTES M9 28 Air Conditioning System M09010 6 97 for HFC 134a Refrigerant ...
Page 618: ...M20 20 Payload Meter II M20007 10 00 ...
Page 619: ...M20007 10 00 Payload Meter II M20 21 ...
Page 627: ...M20007 10 00 Payload Meter II M20 29 ...
Page 634: ...NOTES N1 2 Index N01020 03 01 ...
Page 654: ...NOTES N3 6 Cab Components N03011 7 98 ...
Page 660: ...NOTES N4 6 Operator Comfort N04020 ...
Page 686: ...NOTES N5 26 Operator Cab Controls N05044 ...
Page 688: ...NOTES P1 2 Index P01024 ...
Page 691: ...P02034 Lubrication and Service P2 3 ...
Page 722: ......
Page 723: ......
Page 724: ......
Page 725: ......
Page 726: ......
Page 727: ......
Page 728: ......
Page 729: ......
Page 730: ......
Page 731: ......
Page 732: ......
Page 733: ......
Page 734: ......
Page 735: ......
Page 736: ......
Page 737: ...NOTES R1 2 930E Schematics R01048 with Cummins QSK60 Series Engine ...
Page 738: ......
Page 739: ......