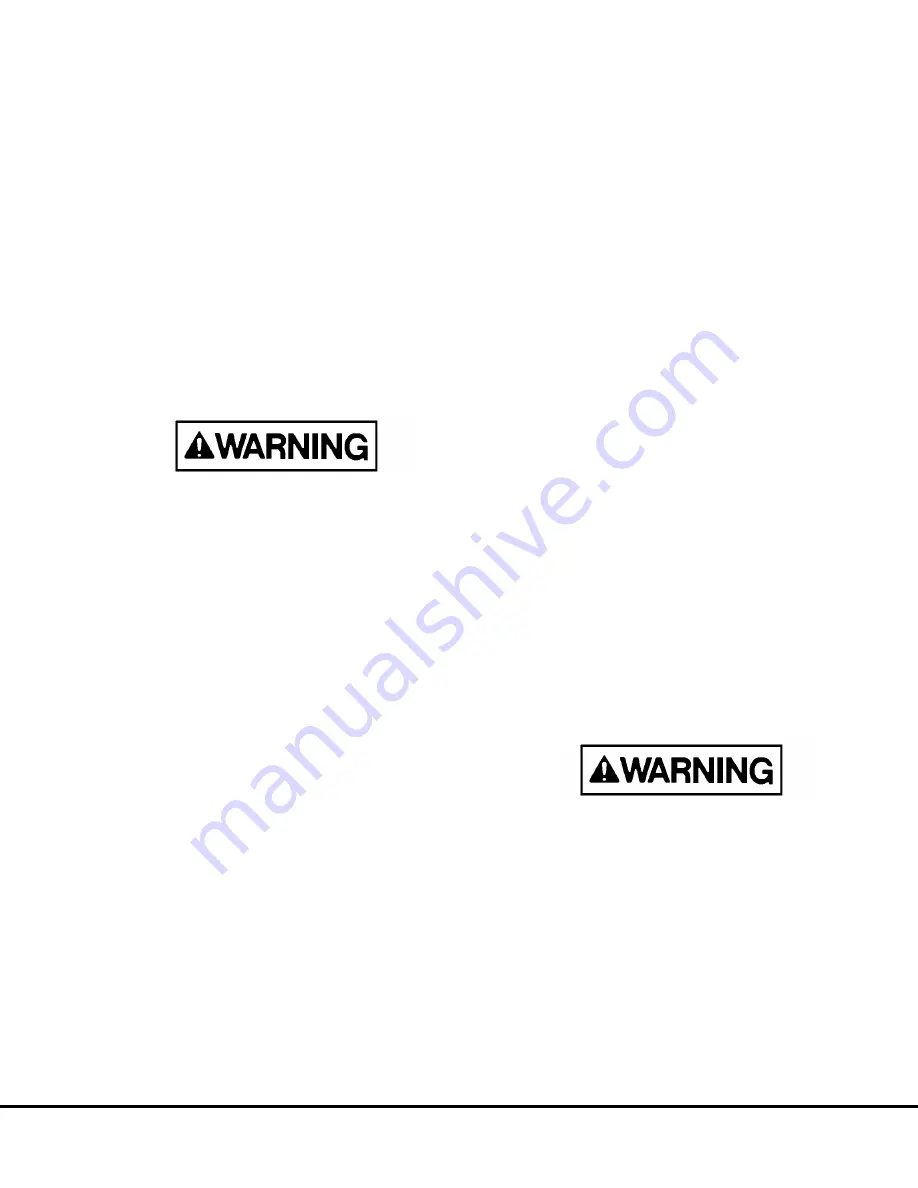
4. Circulate the coolant by operating the engine until
normal operating temperature is reached 160° -
185° F ( 71° - 85° C).
5. Stop the engine.
6. Drain the engine crankcase, then reinstall and
tighten the drain plug. Install new lubricating oil
filter elements and gaskets.
7. Fill the crankcase to the proper level with a 30-
weight preservative lubricating oil MIL-L-21260C,
Grade 2.
8. Drain the fuel tank. Refill with enough clean No. 1
diesel fuel or pure kerosene to permit the engine
to operate for about ten (10) minutes. If it isn’t
convenient to drain the fuel tank use a separate
portable supply of the recommended fuel.
If engines in vehicle are stored where condensa-
tion of water in the fuel tank may be a problem, add
pure, waterless isopropyl alcohol (isopropanol) to
the fuel at a ratio of one pint to 125 gallons(473 L)
of fuel, or 0.010% by volume. Where biological
contamination of fuel may be a problem, add a
biocide such as Biobor JF, or equivalent to the fuel.
When using a biocide, follow the manufacturer’s
concentration recommendations, and observe all
cautions and warnings.
9. Drain and disassemble the fuel filter and strainer.
Discard the used elements and gaskets. Fill the
cavity between the element and shell with No. 1
diesel fuel or pure kerosene, and reinstall on the
engine. If spin-on fuel filters and strainers are
used, discard the used cartridges, fill the new
ones with No. 1 diesel fuel or pure kerosene, and
reinstall on the engine.
10. Operate the engine for five (5) minutes to circulate
the clean fuel oil throughout the fuel system.
11. Service the air cleaner.
12. Turbocharger bearings are pressure lubricated
through the external oil line leading from the en-
gine cylinder block while the engine is operating.
However, the turbocharger air inlet and turbine
outlet connections should be sealed off with mois-
ture resistant tape.
13. Apply a rust preventive compound to all exposed
non-painted surfaces.
14. Drain the engine cooling system.
15. Drain the preservative oil from the engine crank-
case. Reinstall and tighten the drain plug.
16. Remove and clean the batteries and battery cables
with baking soda-water solution and rinse them
with fresh water. Do not allow the soda solution to
enter the battery. Add distilled water to the electro-
lyte, if necessary, and fully charge the battery.
Store the battery in a cool (never below 32° F or 0°
C) dry place. Keep the battery fully charged and
check the level and the specific gravity of the
electrolyte regularly. Never set batteries on con-
crete floor. Place on wooded blocks.
17. Insert heavy paper strips between the pulleys and
belts to prevent sticking.
18. Seal all engine openings, including the exhaust
outlet, with moisture resistant tape. Use card-
board, plywood or metal covers where practical.
19. Clean and dry the exterior painted surfaces of the
engine and spray with a suitable liquid automotive
body wax, a synthetic resin varnish or a rust pre-
ventive compound.
20. Protect the engine with a good weather-resistant
tarpaulin and store it under cover, preferably in a
dry building with temperatures above freezing.
Outdoor storage of engines is not recommended.
However, in some cases outdoor storage may be un-
avoidable. If units must be kept out-off-doors, follow
the preparation and storage instructions already given.
Protect units with quality, weather-resistant tarpaulins
(or other suitable covers) arranged to provide air cir-
culation.
Do not use plastic sheeting for outdoor storage.
Plastic may be used for indoor storage. However,
when used outdoors, moisture can condense on
the inside of the plastic and cause ferrous metal
surfaces to rust and/or pit aluminum surfaces. If a
unit is stored outside for any extended period of
time, severe corrosion damage can result.
The stored engine should be inspected periodically. If
there are any indication of rust or corrosion, corrective
steps must be taken to prevent damage to the engine
parts. Perform a complete inspection at the end of one
year and apply additional treatment, as required.
A07003
Storage Procedures
A7-11
Summary of Contents for 930E-2
Page 1: ......
Page 2: ......
Page 4: ...NOTES ...
Page 8: ...KOMATSU MODEL 930E Dump Truck A 4 Introduction A00017 03 01 ...
Page 10: ...NOTES A1 2 Index A01001 2 94 ...
Page 12: ...930E MAJOR COMPONENTS A2 2 Major Component Description A02055 ...
Page 35: ...START HERE Walk Around Inspection A03017 General Safety and Operating Instructions A3 21 ...
Page 46: ...NOTES A3 32 General Safety and Operating Instructions A03017 ...
Page 78: ...NOTES B1 2 Index B01016 ...
Page 88: ...NOTES B3 6 Dump Body B03013 03 01 ...
Page 92: ...NOTES B4 4 Fuel Tank B04015 ...
Page 94: ...NOTES C1 2 Index C01021 03 01 ...
Page 118: ...NOTES C5 6 Air Filtration System C05013 5 98 ...
Page 126: ...NOTES D2 6 24VDC Electric Supply System D02018 ...
Page 142: ...NOTES D3 16 24VDC System Components D03019 04 01 ...
Page 146: ...FIGURE 2 1 PROPULSION SYSTEM DIAGRAM E2 2 Electrical Propulsion System Components E02014 3 01 ...
Page 196: ...NOTES E2 52 Electrical Propulsion System Components E02014 3 01 ...
Page 240: ...NOTES E3 44 AC Drive System Electrical Checkout Procedure 3 01 E03015 Release 17 Software ...
Page 242: ...NOTES G1 2 Index G01017 ...
Page 250: ...NOTES G2 8 Tires and Rims G02015 ...
Page 274: ...NOTES H1 2 Index H01013 04 01 ...
Page 282: ...NOTES H2 8 Front Suspensions H02013 2 01 ...
Page 288: ...NOTES H3 6 Rear Suspensions H03013 ...
Page 334: ...NOTES J3 32 Brake Circuit Component Service J03019 1 99 ...
Page 378: ...NOTES L2 8 Hydraulic System L02028 ...
Page 401: ...FIGURE 4 5 FLOW AMPLIFIER VALVE L04031 Steering Circuit L4 7 ...
Page 403: ...FIGURE 4 6 FLOW AMPLIFIER NO STEER L04031 Steering Circuit L4 9 ...
Page 405: ...FIGURE 4 7 FLOW AMPLIFIER LEFT STEER L04031 Steering Circuit L4 11 ...
Page 407: ...FIGURE 4 8 FLOW AMPLIFIER RIGHT STEER L04031 Steering Circuit L4 13 ...
Page 409: ...FIGURE 4 9 FLOW AMPLIFIER NO STEER EXTERNAL SHOCK LOAD L04031 Steering Circuit L4 15 ...
Page 414: ...NOTES L4 20 Steering Circuit L04031 ...
Page 422: ...NOTES L5 8 Steering Control Unit L05021 ...
Page 429: ...L06021 Steering Circuit Component Repair L6 7 ...
Page 450: ...NOTES L6 28 Steering Circuit Component Repair L06021 ...
Page 466: ...NOTES L7 16 Hoist Circuit L07023 ...
Page 492: ...NOTES L9 6 Hydraulic System Filters L09008 ...
Page 504: ...NOTES L10 12 Hydraulic Check out Procedure L10012 ...
Page 508: ...NOTES M1 2 Index M01034 03 01 ...
Page 518: ...NOTES M2 3 10 Ansul Checkfire Electric Detection and Actuation System M02003 ...
Page 524: ...NOTES M5 4 Wiggins Quick Fill Fuel System M05002 10 96 ...
Page 532: ...NOTES M8 8 Special Tools M08012 9 99 ...
Page 560: ...NOTES M9 28 Air Conditioning System M09010 6 97 for HFC 134a Refrigerant ...
Page 618: ...M20 20 Payload Meter II M20007 10 00 ...
Page 619: ...M20007 10 00 Payload Meter II M20 21 ...
Page 627: ...M20007 10 00 Payload Meter II M20 29 ...
Page 634: ...NOTES N1 2 Index N01020 03 01 ...
Page 654: ...NOTES N3 6 Cab Components N03011 7 98 ...
Page 660: ...NOTES N4 6 Operator Comfort N04020 ...
Page 686: ...NOTES N5 26 Operator Cab Controls N05044 ...
Page 688: ...NOTES P1 2 Index P01024 ...
Page 691: ...P02034 Lubrication and Service P2 3 ...
Page 722: ......
Page 723: ......
Page 724: ......
Page 725: ......
Page 726: ......
Page 727: ......
Page 728: ......
Page 729: ......
Page 730: ......
Page 731: ......
Page 732: ......
Page 733: ......
Page 734: ......
Page 735: ......
Page 736: ......
Page 737: ...NOTES R1 2 930E Schematics R01048 with Cummins QSK60 Series Engine ...
Page 738: ......
Page 739: ......