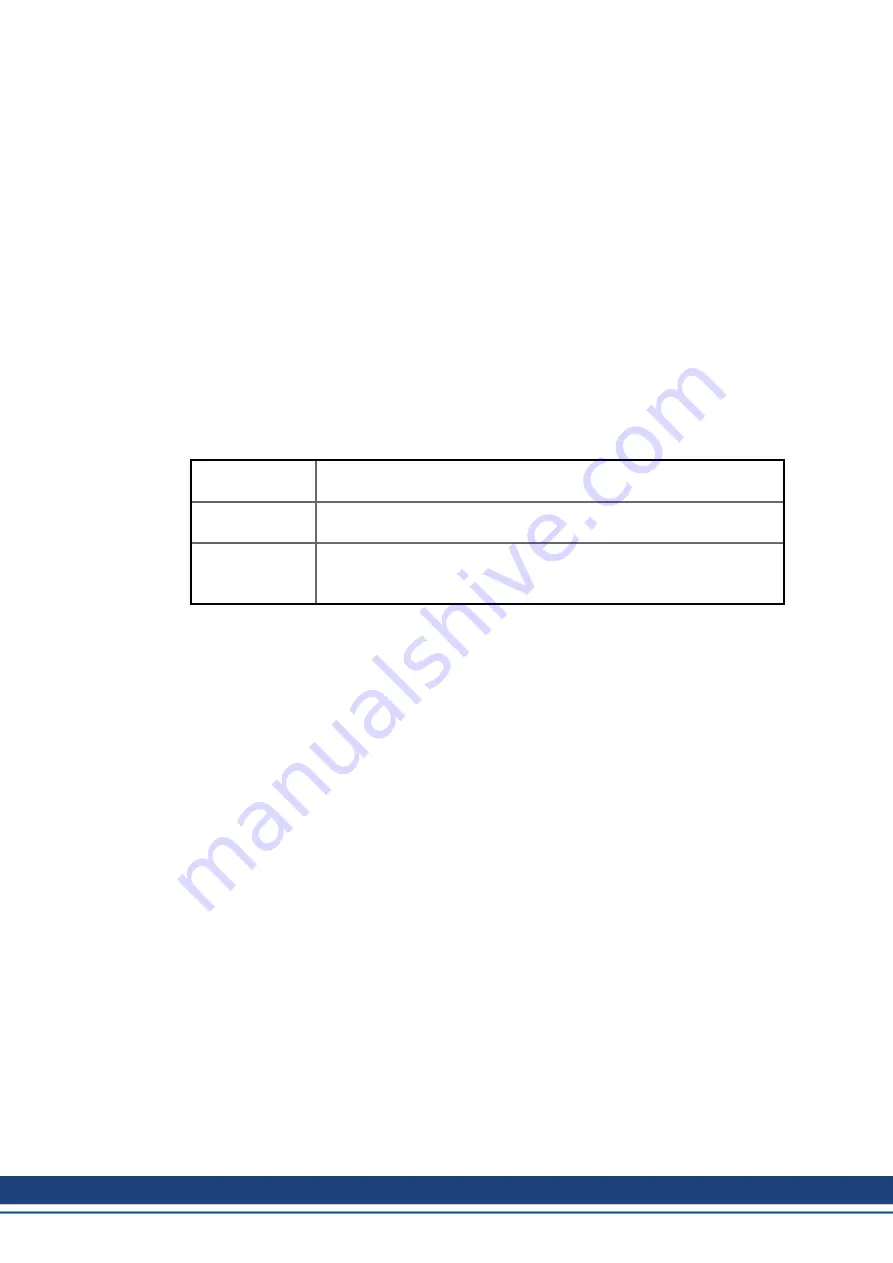
AKD Installation | 7 Technical description and data
7.14 Switch-On and Switch-Off Behavior
This chapter describes the switch-on and switch-off behavior of the AKD.
Behavior of “holding brake” function
Drives with an enabled holding brake function have a special timing for switching on and off
the output stage (
# 118). Events that remove the DRV.ACTIVE signal trigger the holding
brake to apply. As with all electronic circuits, the general rule applies that there is a possibility
of the internal holding brake module failing.
Functional safety, e.g. with hanging load (vertical axes), requires an additional mechanical
brake which must be safely operated, for example by a safety control.
If velocity drops below threshold
CS.VTHRESH
or timeout occurs during a stop procedure,
the brake is applied. Set parameter MOTOR.BRAKEIMM to 1 with vertical axes, to apply the
motor holding brake (
# 118) immediately after faults or Hardware Disable.
Behavior when undervoltage condition is present
The behavior in an undervoltage condition depends on the VBUS.UVMODE setting.
VBUS.UVMODE
DC Bus Undervoltage Mode. Consult the
WorkBench Online Help
for
configuring the parameter.
0
The drive will report a F502 undervoltage fault any time an undervoltage
condition occurs.
1 (default)
The drive will report a warning n502 if not enabled. The drive will report a
fault if the drive is enabled when the condition occurs, or an attempt is
made to enable while an under voltage condition occurs.
Safety function STO
With the functional safe function STO, the drive can be secured on standstill using its internal
electronics so that even when power is being supplied, the drive shaft is protected against
unintentional restart. The chapter “Safe Torque Off (STO)” describes how to use the STO
function (
46
Kollmorgen | kdn.kollmorgen.com | October 2017