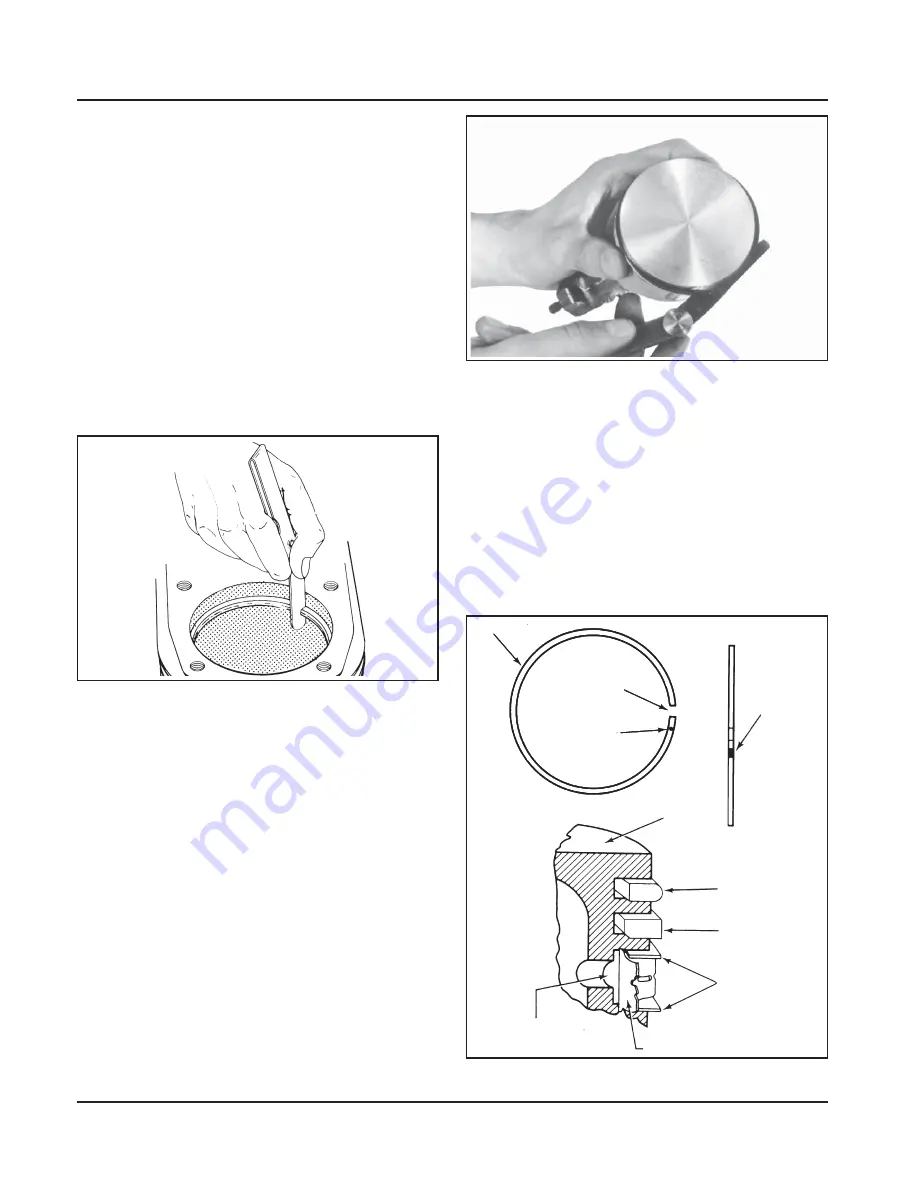
10.10
Section 10
Inspection and Reconditioning
Some important points to remember when servicing
piston rings:
1. If the cylinder bore does not need reboring and
if the old piston is within wear limits and free
of score or scuff marks, the old piston may be
reused.
2. Remove old rings and clean up grooves.
Never
reuse old rings
.
3. Before installing the rings on the piston, place
each of the top two rings in its running area in the
cylinder bore and check the end gap (see Figure
10-8). This gap should be
0.77 mm (0.030 in.)
max
. in a used cylinder bore and
0.3/0.5 mm
(0.012/0.020 in.)
in a new cylinder bore.
Figure 10-9. Measuring Piston Ring Side
Clearance.
Install Piston Rings
To install piston rings, proceed as follows:
NOTE: Rings must be installed correctly. Ring
installation instructions are usually included
with new ring sets. Follow instructions
carefully. Use a piston ring expander to install
rings. Install the bottom (oil control) ring fi rst
and the top compression ring last. Refer to
Figure 10-10.
Figure 10-8. Measuring Piston Ring End Gap.
4. After installing the new compression (top and
middle) rings on the piston, check piston-to-ring
side clearance using a feeler gauge. Compare
readings against the indicated specifi cations. If
the side clearance is greater than the maximum
specifi ed, a new piston
must
be used. Refer to
Figure 10-9.
Top Compression Ring-to-Groove Side Clearance
CV11-14, CV460-465 .... 0.034/0.100 mm (0.0013/0.0039 in.)
CV15,16, CV490-495 .... 0.060/0.105 mm (0.0024/0.0041 in.)
Middle Compression Ring-to-Groove Side Clearance
CV11-14, CV460-465 .... 0.040/0.080 mm (0.0016/0.0031 in.)
CV15,16, CV490-495 .... 0.040/0.085 mm (0.0016/0.0033 in.)
Figure 10-10. Piston Ring Installation.
Piston Ring
Piston
Top Compression
Ring
Center Compression
Ring
Rails
Expander
Oil Control Ring
(Three Piece)
End Gap
Dykem
Stripe
‘‘Pip’’ Mark
Summary of Contents for CV11-16
Page 1: ...1 SERVICE MANUAL VERTICAL CRANKSHAFT CV11 16 CV460 465 CV490 495...
Page 2: ......
Page 4: ......
Page 22: ...2 4 Section 2 Special Tools...
Page 30: ...4 4 Section 4 Air Cleaner and Air Intake System...
Page 56: ...6 6 Section 6 Lubrication System...
Page 112: ...9 16 Section 9 Disassembly...
Page 148: ...11 24 Section 11 Reassembly...
Page 149: ......