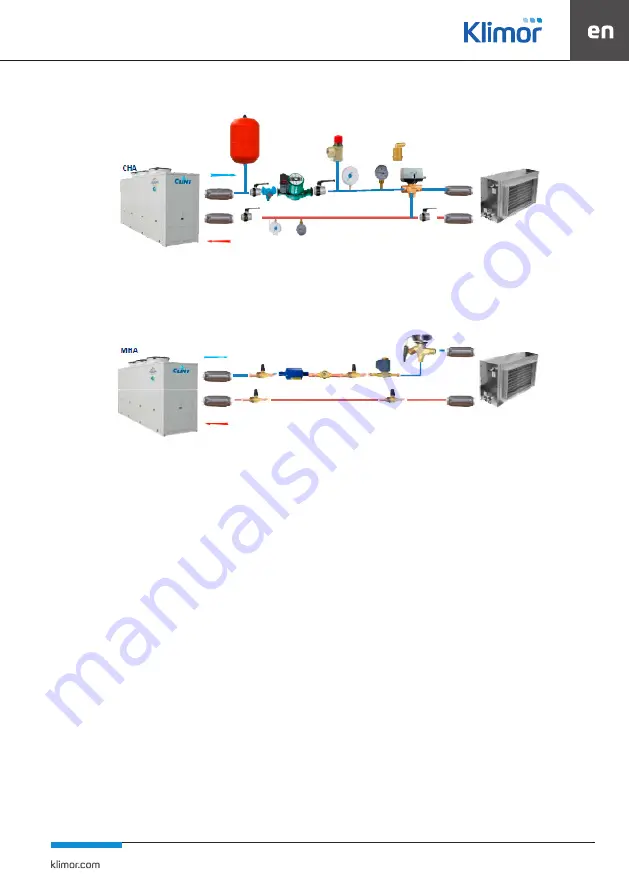
91
4.8.3 Recommended water cooler mode design
Fig. 69
Example of connecting a water cooler
4.8.4. Recommended DX cooler mode design
Fig. No. 70
Connection of DX Cooling coils
DX cooler
4.8.5 Operating recommendations for water exchangers
The state of contamination of the water exchanger lamellas
should be checked at least every 12 months, but it is recom-
mended when replacing the filters.
When the exchanger is contaminated, it should be cleaned
with a vacuum cleaner with a soft suction nozzle on the
side of air inlet or blown through with compressed air on
the side of air outlet. It is also possible to wash it with warm
water and cleaning agent that does not cause aluminium
corrosion. When filling the installation, it should be remem-
bered to bleed the exchanger at all times.
Every 12 months the condensers should be checked for cle-
anliness of the condenser, the drip tray, and the condensate
drainability and trap condition. If the drop separator is so-
iled, wash it with warm water with washing agents.
Before the winter period, if the medium is chilled water and
the exchanger will not work, drain the water if the exchan-
ger is exposed to direct cold air flow.
4.8.6 Operating recommendations for exchangers for direct evap-
oration
Operation analogous to a water cooler, with the following
proviso: washing the cooler with direct evaporation of DX
with hot water requires prior suction of the refrigerant from
the cooling system. Otherwise, gas pressure may increase,
which may damage the cooling installation.
In case of marks of sedimentation in the drip tray, wash it
with water with the addition of a descaling agent. Rinse the
condenser drain tray with warm water and detergent, and
even with a decalcification agent if required.
4.8.7 Pomp group
In terms of delivery, it is possible to supply a pump group,
to supply the heating coil, as a replace-ment option for only
three-way valves with actuator
The technical documentation OMM of the pump group is
added together with the device in a separate document.
Summary of Contents for EVO - H
Page 60: ...SERWIS SERVICE 48 587839954 48 500087227 serwis klimor com...
Page 118: ...SERWIS SERVICE 48 587839954 48 500087227 serwis klimor com...
Page 119: ...EVO S EVO H KLIMOR...
Page 127: ...125 14 11 12 13 3 2 15 16 15 16 17 17 18 18 RR OMM KL RR ASM GUILS Klimor...
Page 130: ...128 EVO S EVO H 25 26 c 200x200 300x200 27 27 d 0230 0090 300x200 28 28 0230 0090...
Page 132: ...130 EVO S EVO H 2900 a 50 31 b 150 32 c 33 2900 b c...
Page 141: ...139 43 8 1200 600 230 50 36 310 x 230 x 125 4 3 2 E G4 ISO COARSE 60 6...
Page 142: ...140 EVO S EVO H 44 45 46 100 C 47 48 49...
Page 143: ...141 4 3 3 SR 50 230 50 60 CA 1 2 CG 3 2 CG 3 1 CA 4 3 4 52 51...
Page 144: ...142 EVO S EVO H 53 54 55 4...
Page 145: ...143 56 4 3 5 G4 ISO COARSE 60 6 57 57 58 INOX 2 3 Power supply LED C 3x2 5 2x2 5 C 2x1 5...
Page 146: ...144 EVO S EVO H 59 60 C 4 4 WH CuAl 4 8 1 4 5 EH 60 4 5 1 4...
Page 149: ...147 62 3 5 4 5 6 7 63 8 4 9 64 63 64 4 7 2 12 5 5...
Page 157: ...155 150 4 12 1 CPR PR 6 12 50 0 C 4 13 RG 55 76 Cu Al Cu Al 23 DN63 PN Klimor Klimor 230 50...
Page 167: ...165 4 14 2 3 4 14 3 Klimor 5 6 6 1 KT 8 100 C...
Page 168: ...166 EVO S EVO H 7 12 PN EN 13779 2008 12 2000 24 4000 24 4000 3 6 12 30 C 130 C 4...
Page 169: ...167 8 30 1 2 3 DX 4 5 6 7...
Page 171: ...169 10 KLIMOR EVO KLIMOR EVO a b 10 10 c IP54 d c e 83 84 f IP65 85 86 32 A 50 0 1 1...
Page 173: ...171 11 7 11 8 11 9 91 11 10 DIN 1946 4 DIN 1946 4 DIN 1946 4 DIN 1946 4 3 I 2 4 0 8 80 20 1...
Page 174: ...172 EVO S EVO H 11 11 m in HEPA...
Page 175: ...173 m in HEPA EN ISO 14644 1 3...
Page 176: ...174 EVO S EVO H 12...
Page 177: ......