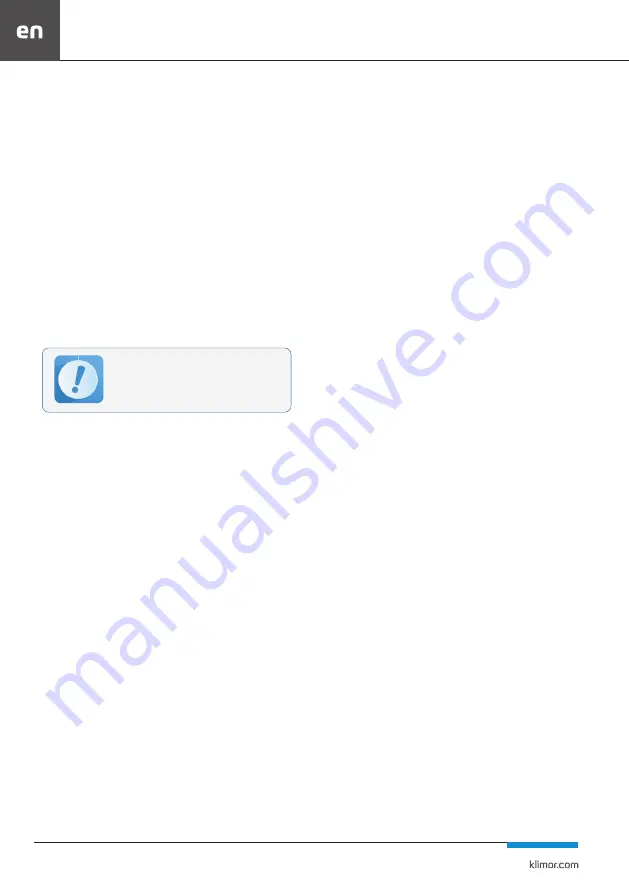
96
EVO-S, EVO-H
MODULAR AIR HANDLING UNITS
OPERATION AND MAINTENANCE MANUAL
4.12 PR cross-flow exchanger / CPR high efficiency hybrid heat
recovery system
The cross-exchanger allows heat recovery from the outlet
air with an efficiency of up to 75% and the high efficiency
hybrid kit up to 92%.
The main components are: cross-flow exchanger or hybrid
exchanger, by-pass, two-section damper, condensate tray
and condenser. The cross-flow exchanger is made of thin
extruded aluminium plates, which form ducts for intake
and outlet air. The warm outlet air flow from the room flows
through the exchanger channels heating its plates. The in-
take air stream flows in a perpendicular direction to the out-
let air stream, taking heat from the exchanger plates.
Heat recovery on the cross-flow exchanger does not require
any energy supply from outside, the exchanger has no mov-
ing parts, which ensures its high reliability.
The intake and outlet air streams are separated from each
other. The internal tightness is determined at 99.5-99.9%
In the outlet part, behind the exchanger, there is a condens-
er and a condensate tray.
The exchangers for the size of the unit 0930 and larger are
supplied in parts due to their dimensions.
KLIMOR employees are required to install them.
The by-pass mounted on the exchanger is to enable it to be
bypassed by the flowing air. Air is directed through the by-
pass during the summer and in the anti-frost process.
Protection of the exchanger against the effects of excessive
cooling and frosting takes place in the exhaust part of the
exchanger.
The protection consists of:
• actuator of the cross-flower damper
• differential pressure sensor before and behind the ex-
changer
• regulator
When the pre-set pressure drop on the pressure switch
is reached, as a result of the exchanger defrosting, the
controller sends a signal to the actuator and the damp-
er on the exchanger closes and the air flow is opened
through the by-pass. This happens until the exchanger
is heated up and the frost dissolves. From this moment
on, the damper on the exchanger starts to open, passing
through the exchanger an increasing flow of fresh air.
ATTENTION: The cross- or high-efficiency hybrid heat
exchanger is supplied as standard without an anti-frost
system. The type of system is determined by the ven-
tilation and automation system designer. A pressure
system is recommended. The pressure switch setting
should be 150% of the design air pressure drop on the
outlet side of the exchanger. The value of pressure drop
is given in the technical data of the air handling unit.
4.12.1 Operation of the CPR and PR exchanger
The cross-flow exchanger should be inspected every 6/12
month. Aluminium lamellas get soiled, and excess soil may
accumulate on the plate edges (down to a depth of 50mm).
Before cleaning cross-flow exchanger sections, the neigh-
bouring sections should be secured. Clean with a vacuum
cleaner with a soft suction nozzle on the side of air inlets or
blow through with air in the direction opposite to the airflow
in the exchanger. It is acceptable to wash the lamellas with
water and cleaning agent that does not cause aluminium cor-
rosion or to rinse them with a water jet under heavy pressure
(for considerable dirt).
When performing all the operations, care should be taken
so as not to deform the aluminium plates. If maintenance
and cleaning of the exchanger is done in outdoor tempera-
ture below 0ºC, the unit should be completely dried before
restart. In addition, the operation and cleanliness of the
dampers, the condition of the condenser and drip tray and
the drainability of the condensate drain should be checked
during the inspection.
4.13 Design with RG intermediary cooling system
A heat recovery system with an intermediary medium al-
lows for heat recovery of up to 55%, and in the juice version
up to 76%.
It completely separates the outlet air flow from the supply air
and can be installed in separate units: intake and outlet AHU.
The set includes two Cu-Al heat exchangers and a hydraulic
system with a circulation pump. The design of the heat ex-
changers is similar to Cu-Al water heaters and coolers.
The exchanger placed in the outlet air flow (cooler) collects
heat from the air and transfers it to the medium. The medi-
um is a water solution of ethylene or propylene glycol, circu-
lating in the pipes connecting the two heat exchangers. The
exchanger, placed in the intake air flow, acts as a preheater,
transferring heat from the medium to the air. The exchanger
on the outlet is equipped with a condenser and the section
is additionally equipped with a condensate drip tray with an
outlet stub directed to the operating side.
Glycol system versions:
The exchangers are mounted in a set of SE units.
Glycol system is a complete equipment: circulation pump,
expansion vessel, pipelines, pressure gauges, valves. The
equipment is located outside or inside the unit casing and
fits into the length of the set.
The supplly and exhaust AHU units are located at a dis-
tance from each other.
Heat recovery exchangers are installed in the supply and
exhaust AHU. The glycol installation is located outside the
air handling units. Depending on the length of the pipelines
and the complexity of the installation, which increases the
glycol flow resistance, the power of the pump motors in re-
lation to those given in Table 23 may be increased.
The installation is made of PP pipes in the welding system,
and for diameters larger than DN63 the installation can be
made of galvanized pipes and is bolted.
Remember to install the trap on the outlet
stub of the tray in accordance with the notes
in point 3.5.3.
Summary of Contents for EVO - H
Page 60: ...SERWIS SERVICE 48 587839954 48 500087227 serwis klimor com...
Page 118: ...SERWIS SERVICE 48 587839954 48 500087227 serwis klimor com...
Page 119: ...EVO S EVO H KLIMOR...
Page 127: ...125 14 11 12 13 3 2 15 16 15 16 17 17 18 18 RR OMM KL RR ASM GUILS Klimor...
Page 130: ...128 EVO S EVO H 25 26 c 200x200 300x200 27 27 d 0230 0090 300x200 28 28 0230 0090...
Page 132: ...130 EVO S EVO H 2900 a 50 31 b 150 32 c 33 2900 b c...
Page 141: ...139 43 8 1200 600 230 50 36 310 x 230 x 125 4 3 2 E G4 ISO COARSE 60 6...
Page 142: ...140 EVO S EVO H 44 45 46 100 C 47 48 49...
Page 143: ...141 4 3 3 SR 50 230 50 60 CA 1 2 CG 3 2 CG 3 1 CA 4 3 4 52 51...
Page 144: ...142 EVO S EVO H 53 54 55 4...
Page 145: ...143 56 4 3 5 G4 ISO COARSE 60 6 57 57 58 INOX 2 3 Power supply LED C 3x2 5 2x2 5 C 2x1 5...
Page 146: ...144 EVO S EVO H 59 60 C 4 4 WH CuAl 4 8 1 4 5 EH 60 4 5 1 4...
Page 149: ...147 62 3 5 4 5 6 7 63 8 4 9 64 63 64 4 7 2 12 5 5...
Page 157: ...155 150 4 12 1 CPR PR 6 12 50 0 C 4 13 RG 55 76 Cu Al Cu Al 23 DN63 PN Klimor Klimor 230 50...
Page 167: ...165 4 14 2 3 4 14 3 Klimor 5 6 6 1 KT 8 100 C...
Page 168: ...166 EVO S EVO H 7 12 PN EN 13779 2008 12 2000 24 4000 24 4000 3 6 12 30 C 130 C 4...
Page 169: ...167 8 30 1 2 3 DX 4 5 6 7...
Page 171: ...169 10 KLIMOR EVO KLIMOR EVO a b 10 10 c IP54 d c e 83 84 f IP65 85 86 32 A 50 0 1 1...
Page 173: ...171 11 7 11 8 11 9 91 11 10 DIN 1946 4 DIN 1946 4 DIN 1946 4 DIN 1946 4 3 I 2 4 0 8 80 20 1...
Page 174: ...172 EVO S EVO H 11 11 m in HEPA...
Page 175: ...173 m in HEPA EN ISO 14644 1 3...
Page 176: ...174 EVO S EVO H 12...
Page 177: ......