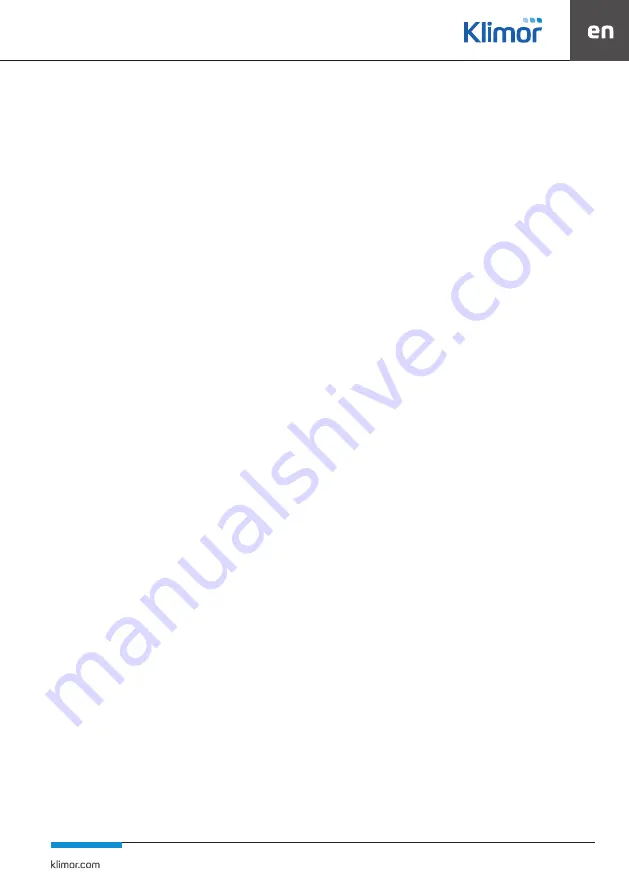
113
11.11 Information about cleaning techniques and disinfectant used
A significant impact on the quality of air supplied to the
room is the hygienic condition of venti-lation installations,
including air handling units. In order to maintain air purity
at the required level, it is necessary to carry out periodic cle-
aning and disinfection of all elements of the venti-lation and
air conditioning system, m.in intakes, elements of AHU and
ventilation ducts. Dusts are deposited on their surfaces, etc.
impurities, leading to the development of microorganisms.
Contaminants are created by layers of dry dust that can
be easily cleaned by brushing and vacuuming. In damp or
greasy areas, contaminants form a durable, difficult-to-re-
move structure that is the source of many microorganisms.
Microbes have the ability to adhere to the surface, creating
the so-called biofilm, which allows them to survive even in
difficult conditions of development.
Biofilm is a three-dimensional structure, composed of living
organisms, including bacteria, fungi and even algae and an
amorphous substance created by these microorganisms.
Biofilm removal is an activity that requires the use of che-
micals with a strong biofilm-destroying capacity. Washing
and disinfecting agents with low surface tension, with the
ability to penetrate into the biofilm and decompose the
porous structure, which is a habitat of microorganisms and
the ability to dissolve fats should be used. They must be bio-
degradable, i.e. harmless to humans and the surrounding
environment.
Cleaning should be carried out in the supply and exhaust
parts of the installation and with the venti-lation unit tur-
ned off. Remember to provide personal protective equip-
ment for people carrying out these activities. It is advisable
to carry out all work during periods of interruptions in the
use of ventilated premises. If this is not possible, special pre-
cautions should be taken.
During periodic cleaning of ventilation and air conditioning
installations of rooms where people are staying, it is forbid-
den to use chemicals with toxic effects on the human body.
Dust and biological particles should be collected using va-
cuum cleaners equipped with HEPA filters.
Various methods are used to clean installations, including
air handling units. The choice of the most appropriate one
depends on the type of impurities, the type of cleaned and
disinfected elements and the construction and placement
of the ventilation system.
Among the most commonly used methods, the following
are distinguished:
• mechanical methods – manual cleaning with brushes and
cloths or electric / pneumatic rotary brushes,
• methods using compressed air,
• methods using water (high-pressure washers) or water va-
por (steam washers),
• methods using specialized chemicals, including biocides
and ozone,
• methods using ultrasonic devices, methods using dry ice,
• combined methods.
The cleaning and disinfection process is preceded by a
preliminary assessment of the condition of the ventilation
and air conditioning installations. These activities make it
possible to use inspection windows and interior lighting as
well as inspection panels, through which inspection devi-
ces with cameras or borescopes can be used to observe the
inside area.
After a preliminary inspection of the installation condition,
proceed to the removal of impurities using the appropriate
method. In the case of cleaning ventilation ducts and empty
sections of air handling units, mechanical brushing is a typi-
cal and often used method. This involves removing a layer
of impurities from dirty surfaces and suctioning them with
a vacuum cleaner. This procedure can be carried out manu-
ally or with the use of special rotary brushes. The variety,
complexity and access to individual elements of the instal-
lation requires the use of a wide range of brushes. During
cleaning, rags and cloths are also used.
The use of specialized washing and disinfecting agents
supports the process of removing impurities and all kinds
of microorganisms. Greased elements require to use of spe-
cial detergents when washing. And more and more often
cleaning devices using dry ice are used.
After cleaning all surfaces and elements of the installation,
proceed to disinfection. The scope of disinfection should
be determined by a hygiene specialist. Most often, places
that pose a potential epidemiological threat are subject to
disinfection. In special cases, the entire ventilation and air
conditioning system is subject to disinfection. The disin-
fectants used must be characterized by high efficiency of
neutralizing biological contaminants and negligible harm-
ful effects on the human body. They must not react with the
construction materials of equipment and installations.
An effective method of disinfection is the use of UV radia-
tion. It is indicated primarily in places with the highest pro-
bability of developing microorganisms, in the surrounded
of coolers, humidifiers and air filters.
During the operation of the devices, an important element
is the periodic replacement of air filters, while maintaining
the basic parameters, like filtration class, nominal air flow,
initial and final pressure drop and dimensions. Pressure
drop is the basic criterion for assessing the quality status of
air filters. In ventilation and air conditioning devices, pressu-
re switches or differential pressure sensors are installed to
assess the degree of contamination of filters. There are da-
mage in the filters that are not always detected by sensors,
e.g. leaks and holes in filters. This type of damage is detec-
ted during periodic inspections.
The final stage of cleaning and disinfection of ventilation
and air conditioning equipment is to obtain a positive result
Summary of Contents for EVO - H
Page 60: ...SERWIS SERVICE 48 587839954 48 500087227 serwis klimor com...
Page 118: ...SERWIS SERVICE 48 587839954 48 500087227 serwis klimor com...
Page 119: ...EVO S EVO H KLIMOR...
Page 127: ...125 14 11 12 13 3 2 15 16 15 16 17 17 18 18 RR OMM KL RR ASM GUILS Klimor...
Page 130: ...128 EVO S EVO H 25 26 c 200x200 300x200 27 27 d 0230 0090 300x200 28 28 0230 0090...
Page 132: ...130 EVO S EVO H 2900 a 50 31 b 150 32 c 33 2900 b c...
Page 141: ...139 43 8 1200 600 230 50 36 310 x 230 x 125 4 3 2 E G4 ISO COARSE 60 6...
Page 142: ...140 EVO S EVO H 44 45 46 100 C 47 48 49...
Page 143: ...141 4 3 3 SR 50 230 50 60 CA 1 2 CG 3 2 CG 3 1 CA 4 3 4 52 51...
Page 144: ...142 EVO S EVO H 53 54 55 4...
Page 145: ...143 56 4 3 5 G4 ISO COARSE 60 6 57 57 58 INOX 2 3 Power supply LED C 3x2 5 2x2 5 C 2x1 5...
Page 146: ...144 EVO S EVO H 59 60 C 4 4 WH CuAl 4 8 1 4 5 EH 60 4 5 1 4...
Page 149: ...147 62 3 5 4 5 6 7 63 8 4 9 64 63 64 4 7 2 12 5 5...
Page 157: ...155 150 4 12 1 CPR PR 6 12 50 0 C 4 13 RG 55 76 Cu Al Cu Al 23 DN63 PN Klimor Klimor 230 50...
Page 167: ...165 4 14 2 3 4 14 3 Klimor 5 6 6 1 KT 8 100 C...
Page 168: ...166 EVO S EVO H 7 12 PN EN 13779 2008 12 2000 24 4000 24 4000 3 6 12 30 C 130 C 4...
Page 169: ...167 8 30 1 2 3 DX 4 5 6 7...
Page 171: ...169 10 KLIMOR EVO KLIMOR EVO a b 10 10 c IP54 d c e 83 84 f IP65 85 86 32 A 50 0 1 1...
Page 173: ...171 11 7 11 8 11 9 91 11 10 DIN 1946 4 DIN 1946 4 DIN 1946 4 DIN 1946 4 3 I 2 4 0 8 80 20 1...
Page 174: ...172 EVO S EVO H 11 11 m in HEPA...
Page 175: ...173 m in HEPA EN ISO 14644 1 3...
Page 176: ...174 EVO S EVO H 12...
Page 177: ......