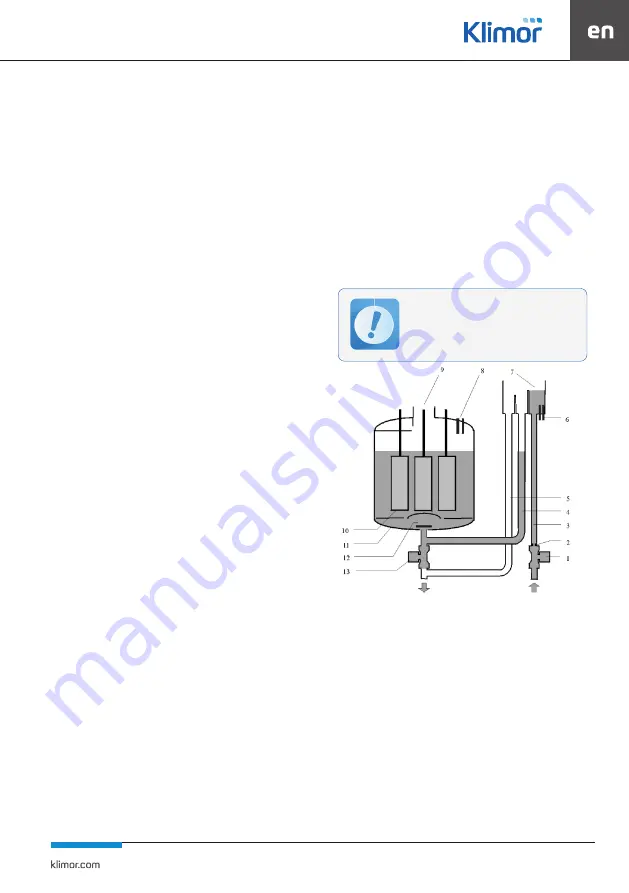
87
Scope of actions to be performed by the installation com-
pany:
1. Assembling and starting the air handling unit.
2. Installing the air handling unit temperature sensor (instal-
lation on the connected duct behind the module at a dis-
tance of approx. 3 m).
3. Execution of passages in protective sleeves through the
air handling unit cover for gas pipe and condensate pipe.
4. Mounting the burner.
5. Building the gas installation supplying the burner, ac-
cording to the burner OMM, venting and starting the instal-
lation (gas pressure according to the burner OMM).
6. Installing the exhaust stack. Depending on the type of
gas module, the exhaust stack can also be brought out to
the opposite side of the operator
7. Mounting outside of the unit a Ø20 condense pipe and,
if necessary, connection to the condense installation on the
building.
8. Electrical connections:
a. Cable for supplying the control switchboard mounted on the
module.
b. Burner power supply cable.
c. Burner control cables.
d. Control cable - power control 0÷10V.
e. Control cable - start/stop signal.
f. Cable for supply air temperature sensor.
g. Optional cable to indicate operation and failure of the mod-
ule to the air handling unit controller.
Additionally:
• Safe access to the module and the air handling unit must
be provided on site in accordance with health and safety
rules
• The user must be present when performing any work on
the device.
• After the service has been carried out, training will be giv-
en to a person designated by the user in the operation and
use of the installed equipment.
• Temperature below -5°C as well as precipitation make it
impossible to start up the device.
• It is recommended to use condensate neutralizers if such
a requirement is made by the designer or the local Envi-
ronmental Protection Department (upon request from the
Service Department).
• After the installation is adjusted, the opening of the bypass
damper (if any) should be adjusted to the flow rate speci-
fied in the Head Office Data Sheet.
4.7 SH Humidification
The task of humidifiers is to bring the relative air humidity
to the required value. The process is carried out by means of
steam humidifying.
Humidifiers with an electric steam generator
Humidifiers with an electric steam generator use the flow of
current between the electrodes immersed in water to heat
up the water and generate steam.
Water containing minerals is required for the current to
flow between the electrodes. The composition of the water
should be as follows:
Required water parameters:
• pH value: 7÷8.5
• conductivity: 350÷1250 uS/cm
• hardness: 100÷400 mg/l CaCo3
• iron and magnet: 0,2 mg/l Fe+Mg
• silica: max. 20 mg/l SiO2
• no organic pollution
• supply pressure: 1÷6 bar
• temperature: 1÷40°C
• Water flow according to the requirements of a specific
generator
Figure 61
Construction of an electric steam generator
1. Electromagnetic supply valve
2. Flow limiter
3. Power supply cable
4. Filling line
5. Overflow pipe
6. Electrodes for measuring conductivity
7. Supply tank
8. Protection against high water levels
9. Steam outlet
10. Electrodes
11. Cylinder
12. Water filters
13. Electromagnetic drain valve
If mineral concentrations in the water are hi-
gher than those given, the electrodes will be
damaged more quickly and lower ones will
reduce the efficiency of the steam generator.
Summary of Contents for EVO - H
Page 60: ...SERWIS SERVICE 48 587839954 48 500087227 serwis klimor com...
Page 118: ...SERWIS SERVICE 48 587839954 48 500087227 serwis klimor com...
Page 119: ...EVO S EVO H KLIMOR...
Page 127: ...125 14 11 12 13 3 2 15 16 15 16 17 17 18 18 RR OMM KL RR ASM GUILS Klimor...
Page 130: ...128 EVO S EVO H 25 26 c 200x200 300x200 27 27 d 0230 0090 300x200 28 28 0230 0090...
Page 132: ...130 EVO S EVO H 2900 a 50 31 b 150 32 c 33 2900 b c...
Page 141: ...139 43 8 1200 600 230 50 36 310 x 230 x 125 4 3 2 E G4 ISO COARSE 60 6...
Page 142: ...140 EVO S EVO H 44 45 46 100 C 47 48 49...
Page 143: ...141 4 3 3 SR 50 230 50 60 CA 1 2 CG 3 2 CG 3 1 CA 4 3 4 52 51...
Page 144: ...142 EVO S EVO H 53 54 55 4...
Page 145: ...143 56 4 3 5 G4 ISO COARSE 60 6 57 57 58 INOX 2 3 Power supply LED C 3x2 5 2x2 5 C 2x1 5...
Page 146: ...144 EVO S EVO H 59 60 C 4 4 WH CuAl 4 8 1 4 5 EH 60 4 5 1 4...
Page 149: ...147 62 3 5 4 5 6 7 63 8 4 9 64 63 64 4 7 2 12 5 5...
Page 157: ...155 150 4 12 1 CPR PR 6 12 50 0 C 4 13 RG 55 76 Cu Al Cu Al 23 DN63 PN Klimor Klimor 230 50...
Page 167: ...165 4 14 2 3 4 14 3 Klimor 5 6 6 1 KT 8 100 C...
Page 168: ...166 EVO S EVO H 7 12 PN EN 13779 2008 12 2000 24 4000 24 4000 3 6 12 30 C 130 C 4...
Page 169: ...167 8 30 1 2 3 DX 4 5 6 7...
Page 171: ...169 10 KLIMOR EVO KLIMOR EVO a b 10 10 c IP54 d c e 83 84 f IP65 85 86 32 A 50 0 1 1...
Page 173: ...171 11 7 11 8 11 9 91 11 10 DIN 1946 4 DIN 1946 4 DIN 1946 4 DIN 1946 4 3 I 2 4 0 8 80 20 1...
Page 174: ...172 EVO S EVO H 11 11 m in HEPA...
Page 175: ...173 m in HEPA EN ISO 14644 1 3...
Page 176: ...174 EVO S EVO H 12...
Page 177: ......