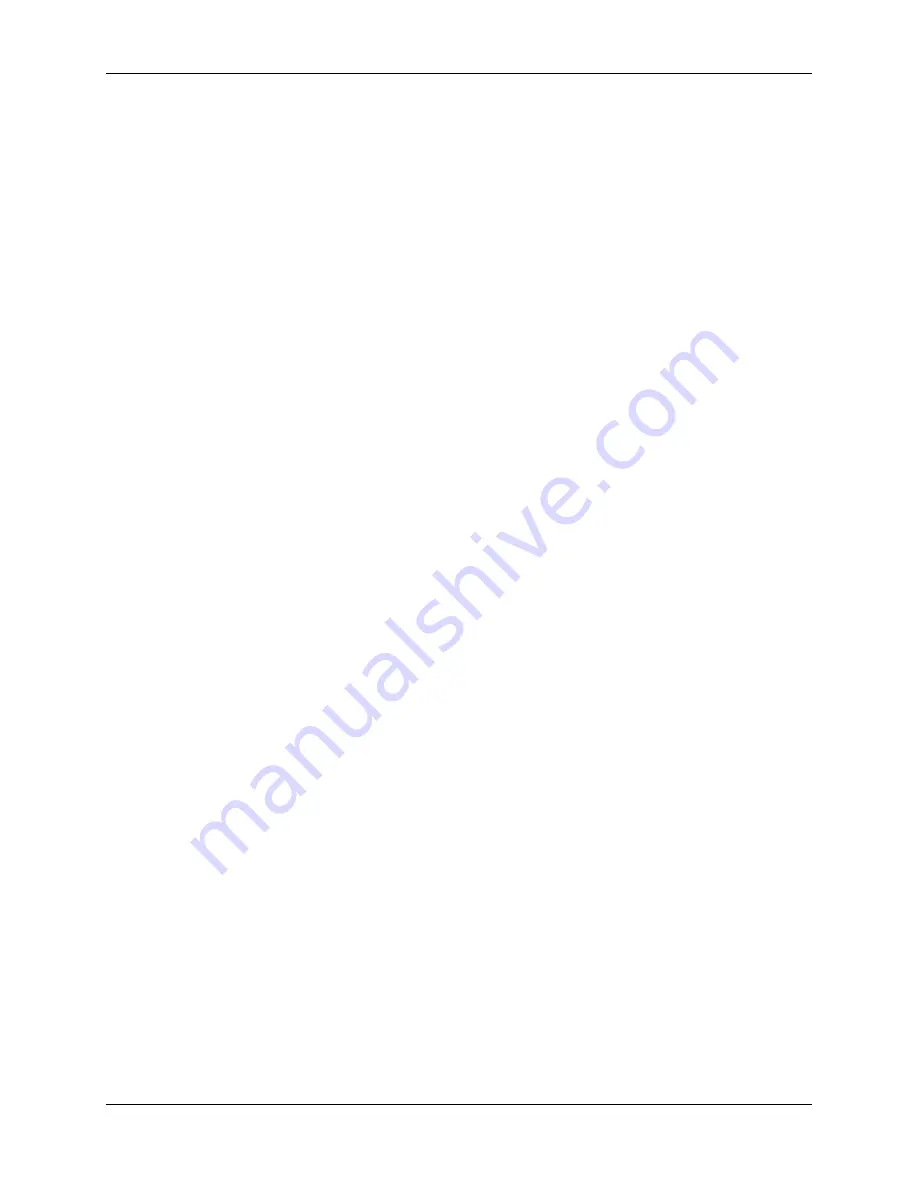
Operation
Spirit200a User’s Manual Rev J
This information is subject to the controls of the Export Administration Regulations [EAR]. This information shall not be provided to
non-U.S. persons or transferred by any means to any location outside the United States contrary to the requirements of the EAR.
4-20
Piercing Thick Materials
Care must be taken when piercing thick materials in order to prevent
damage to the shield cap and nozzle. As with all thicknesses, the pierce
height must be set high enough so the metal ejected while piercing does
not come into contact with the shield cap. Also, some of the material
ejected during the pierce may adhere to the top side of the plate and form
a ring of solidified material around the pierce point. Action must be taken
so the torch does not move from the pierce height down to the cutting
height and come into contact with this solidified metal. The torch should
not move from the pierce height down to the cutting height until the x/y
machine has moved the torch away from the pierce point. One way to
accomplish this may be to program the pierce time on the torch height
control system to a value that is longer than the x/y machine motion delay
time. On very thick materials, an edge start or moving pierce may be
required to prevent damage to the torch consumables. With a moving
pierce, the x/y machine should begin moving at approximately 5–10
inches/minute (125–250 mm/min) as soon as the arc transfers to the plate.
After the arc completely penetrates the plate, the torch should be
positioned at the proper cutting height and the x/y machine speed should
be increased to the correct level. With an edge start, the torch should be
positioned at the edge of the material prior to starting the arc.