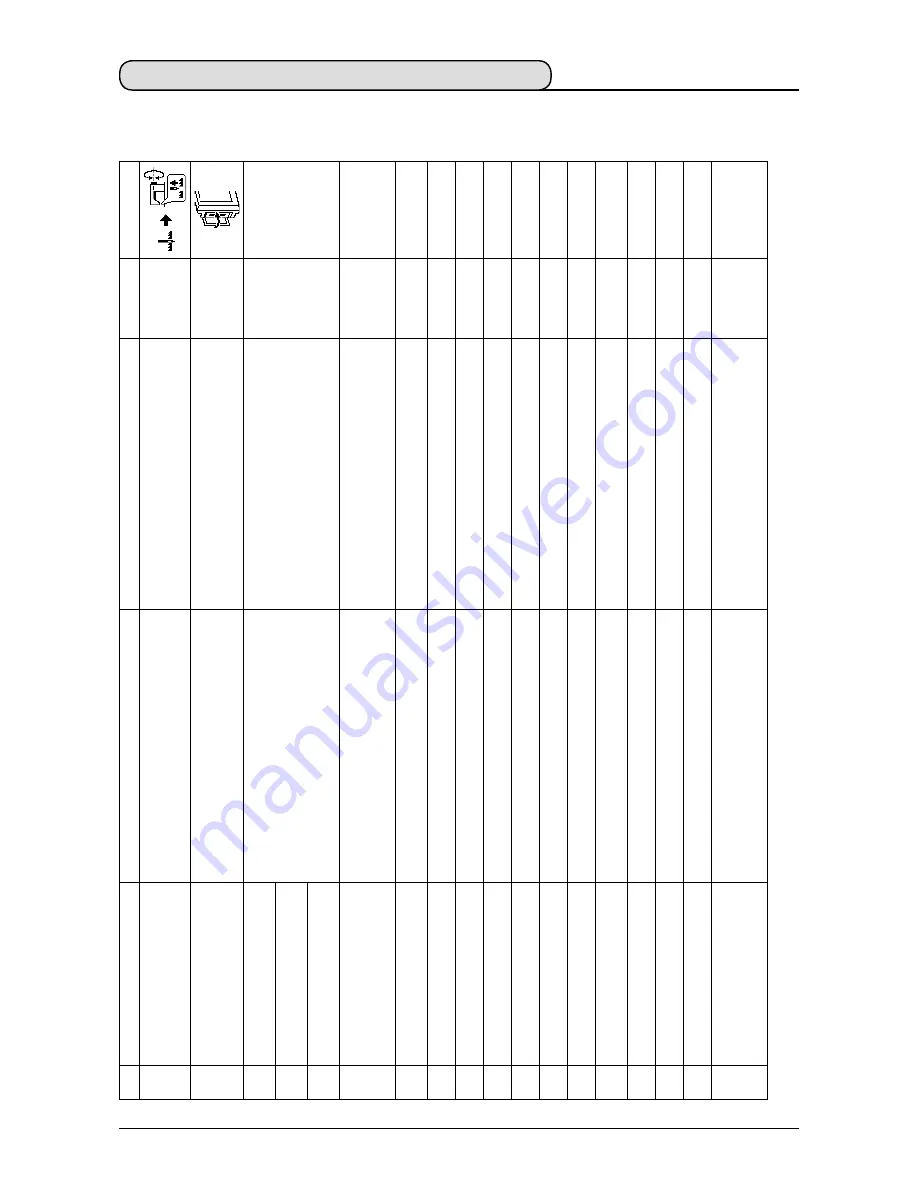
142
11–1. Error code list (Error display in panel)
There are the following error codes in this device. These error codes interlock (or limit function) and inform
the problem so that the problem is not enlarged when any problem is discovered. When you request our
service, please confirm the error codes.
No.
Description of error detected
Cause
Item to be checked or corrective measure
Mirror LED flash
Pictograph display
-
U
P
po
si
tio
n
de
te
ct
io
n
er
ro
r
when turning ON the power
• When
needle
position
is
not
UP
position
at
the
time of turning ON the power
.
• S
et
to
U
P
po
si
tio
n
by
tu
rn
in
g
ha
nd
w
he
el
by
hand. • Connect synchronizer connector
.
-
-
Media cover open
• Lid of media slot is open.
• Close the lid.
-
003
D
is
co
nn
ec
tio
n
of
sy
nc
hr
on
iz
er
connector
• W
he
n
po
si
tio
n
de
te
ct
io
n
si
gn
al
is
no
t i
np
ut
te
d
from the sewing machine head synchronizer
.
• When the synchronizer has broken.
• C
he
ck
th
e
sy
nc
hr
on
iz
er
co
nn
ec
to
r
(C
N
30
)
fo
r
loose connection and disconnection. • C
he
ck
w
he
th
er
t
he
s
yn
ch
ro
ni
ze
r
co
rd
h
as
broken
since
the
cord
is
caught
in
the
machine
head or the like.
-
004
S
yn
ch
ro
ni
ze
r
lo
w
er
p
os
iti
on
sensor failure
005
S
yn
ch
ro
ni
ze
r
up
pe
r
po
si
tio
n
sensor failure
007
Overload of motor
• When the machine head is locked. • W
he
n
se
w
in
g
ex
tra
-h
ea
vy
m
at
er
ia
l b
ey
on
d
th
e
guarantee of the machine head. • When the motor does not run.
• C
he
ck
wh
et
he
r
th
e
th
re
ad
ha
s
be
en
en
ta
ng
le
d
in the motor pulley
.
• Check
the
motor
output
connector
(4P)
for
loose
connection and disconnection.
-
008
Machine head connector failure
• W
he
n
th
e
m
ac
hi
ne
h
ea
d
co
nn
ec
to
r
is
n
ot
properly read.
• Check
the
machine
head
connector
(CN54)
for
loose connection and disconnection.
-
01
1
Media not inserted
• Media is not inserted.
• T
urn OFF the power
.
-
012
Read error
• Data read from media is not possible.
• T
urn OFF the power
.
-
013
W
rite error
• Data write to media is not possible.
• T
urn OFF the power
.
-
015
Format error
• Formatting cannot be performed.
• T
urn OFF the power
.
-
016
External media capacity over
• Capacity of media is short.
• T
urn OFF the power
.
-
019
File size over
• File is too big.
• T
urn OFF the power
.
-
024
Pattern data size over
• Number
of
stitches
and
data
amount
which
can
be handled with device are over
.
• T
urn OFF the power
.
-
032
File compatibility error
• There is no file compatibility
.
• T
urn OFF the power
.
-
040
Travel limit over
• Sewing data has exceeded sewing possible area.
• T
urn OFF the power
.
-
042
Operation error
• Operation of sewing data cannot be performed.
• T
urn OFF the power
.
-
053
Execution
of
panel
backup
data
initialization (Not error)
• When
model
code
of
panel
does
not
agree
with
that of control box. W
he
n
ex
ec
ut
in
g
in
iti
al
iz
at
io
n
op
er
at
io
n
wi
th
th
e
panel.
• T
urn OFF the power
.
-