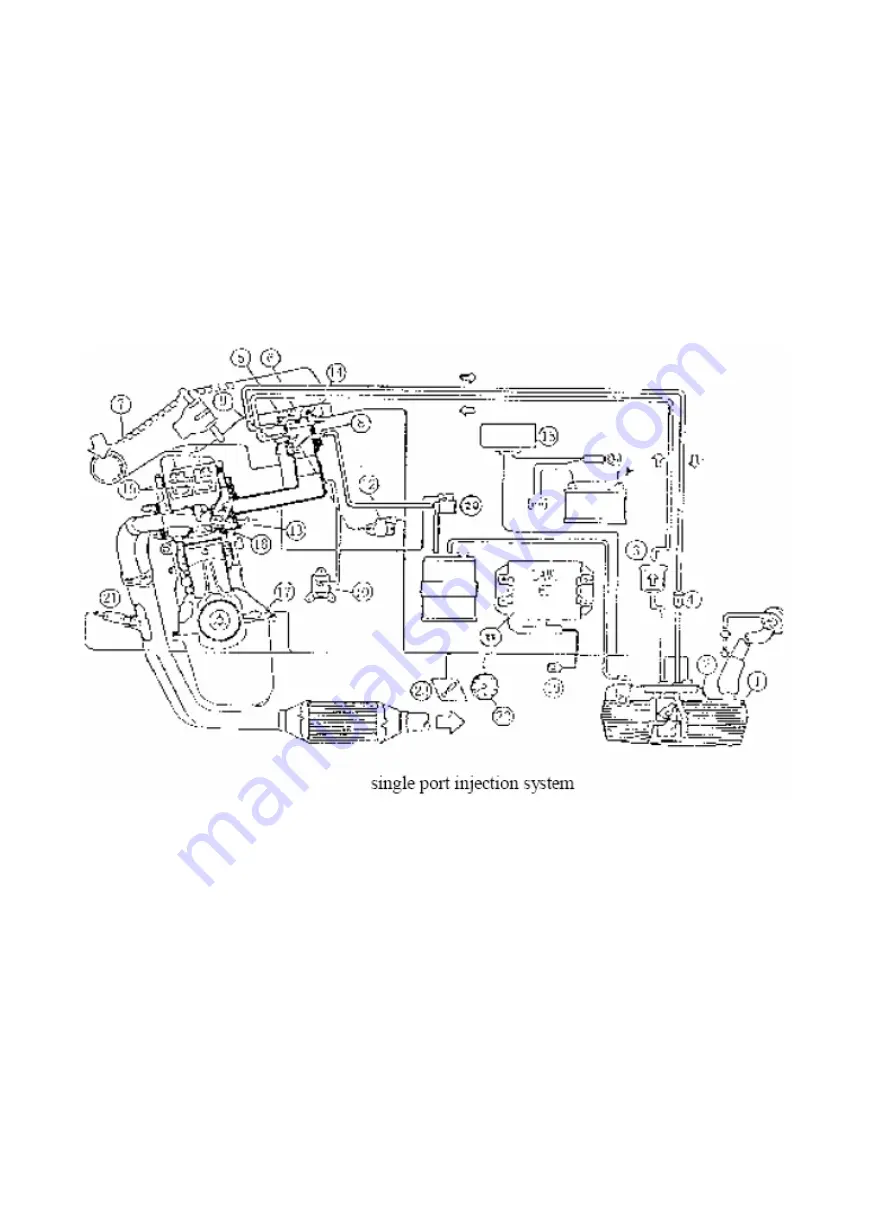
101
CAC480M Engine
’
s single port injection system
[
1
]
. Summarize
The system, referred as “
λ
Speed Density”type (running speed, air density, mixture control), is
designed to perform the control for injection and distributorless ignition. According to the following figure
(figure 159) of Single Port Injection System, three basic parts are included as the following:
1.
“I.A.W.6F
。
”Injection System ECU.
2.
“20MM12”Single Port Injection System throttle valve body.
3.
Two “BAE 800 AK”Ignition coil. The whole system includes fuel pump, fuel filter, RPM
sensor, absolute pressure sensor,
λ
sensor and so on.
Fig.159
1. Fuel tank
2. Fuel pump
3. Fuel filter
4. Check valve
5. Fuel pressure regulator
6. Fuel injector
7. Air filter
8. Fuel vapor connecting pipe
9.Engine idle speed actuator 10. Absolute pressure sensor
11. Injection/ignition system ECU
12. Throttle valve position sensor
13. Water sensor
14. Intake temperature sensor
15. Injection/ignition system dual relay
16. Ignition coil
17. Tacho / TDC sensor
18. Spark plug
19. CHECK-UP1 diagnostic port
20. Fuel vapor recirculation solenoid
21.
λ
sensor
22. Tachometer
23. IAW system warning indicator